Continuous Improvement (CI) in welding is an essential process that boosts efficiency, safety, and quality in various industrial applications. CI in welding involves an ongoing effort to refine and elevate welding procedures to ensure optimal performance and output, meeting the highest industry standards. This is crucial for companies that depend on reliable and durable welds in manufacturing sectors such as automotive, aerospace, and construction. In this article, we will delve into the experience and expertise required in this field, emphasizing the authoritativeness and trustworthiness of established practices in CI welding.
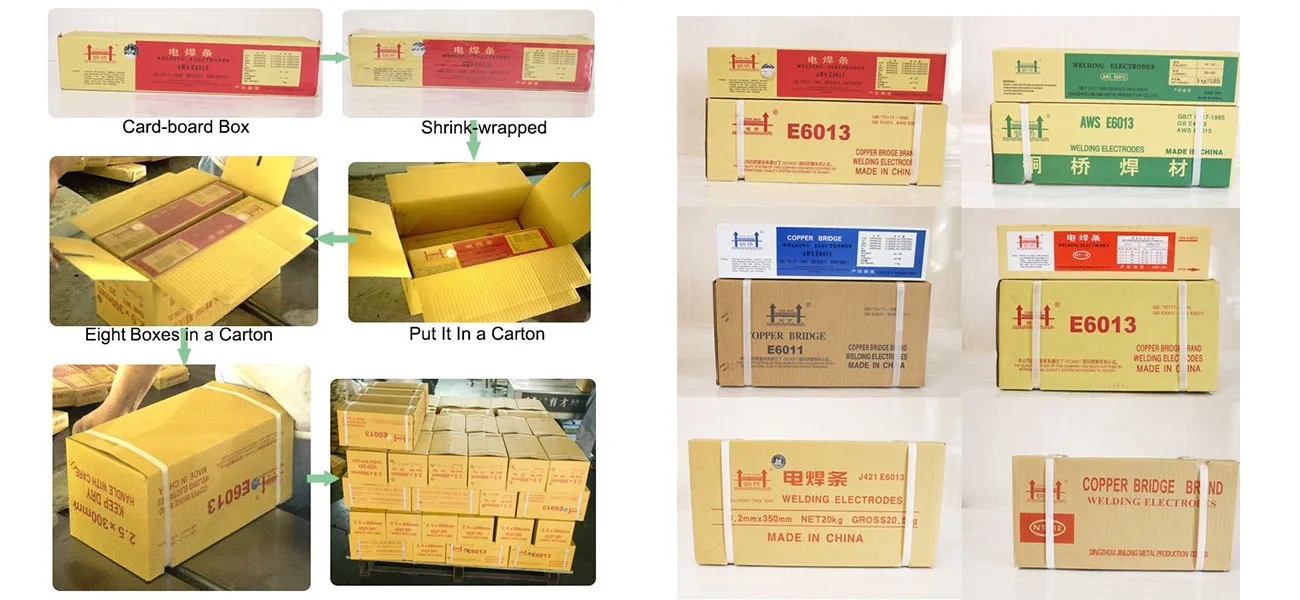
Welding as a craft has evolved dramatically over the years, driven by the need for innovation and efficiency in manufacturing processes. Today, organizations are increasingly adopting CI methodologies such as Lean, Six Sigma, and Total Quality Management (TQM). These methodologies aim to identify inefficiencies and eliminate them altogether. Within welding, this could mean everything from reducing material waste and energy consumption to minimizing the occurrence of defects and rework.
Expertise in CI welding requires a deep understanding of both traditional welding techniques and innovative technologies. Proficient welders and engineers consistently revisit and revise their welding practices through rigorous analysis and feedback. They utilize data and metrics collected from the welding process to identify patterns and areas for improvement, employing advanced technologies such as automation and machine learning for even greater precision and control.
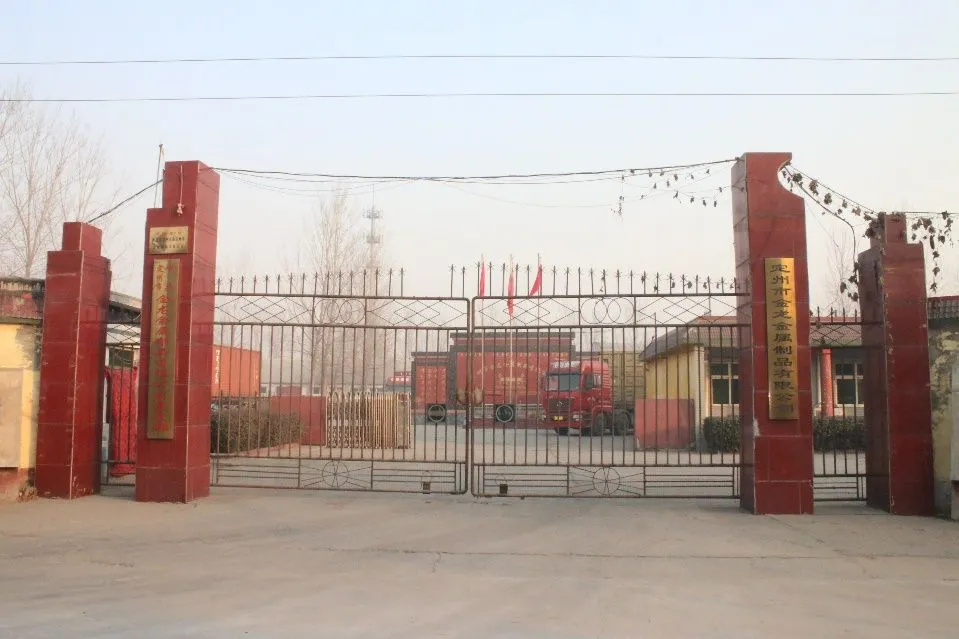
Authoritativeness in CI welding is rooted in adherence to international standards and practices, such as those defined by the American Welding Society (AWS) and the International Organization for Standardization (ISO). These standards provide a framework for quality and safety, and organizations that follow them are often viewed as leaders in the industry. By aligning with these standards, companies demonstrate a commitment to excellence that transcends individual projects and establishes long-term credibility with clients and stakeholders.
Trustworthiness in welding is paramount, as the strength and integrity of welds can significantly impact the safety and functionality of the final product. In industries where the stakes are high, such as aerospace or automotive, a failed weld can lead to catastrophic outcomes. Therefore, implementing CI ensures that materials and processes are not only compliant with industry standards but are also continually inspected and refined. This commitment to quality reassures clients that they are receiving a product that meets the strictest requirements for durability and performance.
ci welding
One of the most significant advancements in CI welding is the integration of automation and robotics. These technologies provide unparalleled precision and repeatability, reducing the variability inherent in manual welding processes. Automated systems can consistently perform high-quality welds, increasing both productivity and consistency. Moreover, the incorporation of real-time data monitoring systems allows for instant analysis and adjustment, greatly reducing the likelihood of errors.
Another exciting frontier in CI welding is the use of additive manufacturing techniques, such as 3D printing. This technology allows for the complex geometries and bespoke components that were previously impossible or economically unfeasible. By incorporating CI principles, these processes can be fine-tuned to reduce waste and enhance quality.
The feedback loop is a critical component of CI. Encouraging a culture where welders and engineers can share insights and suggest improvements fosters an environment of openness and innovation. This culture is pivotal in maintaining a cycle of consistent improvement, where every team member understands the impact of their contributions to the overall success of the company.
Finally, continuous training and certification play a vital role in maintaining expertise within the field of CI welding. Regular workshops, courses, and accreditation opportunities ensure that workers are up to date with the latest technologies, standards, and techniques. This ongoing education not only enhances an employee’s technical abilities but also reinforces a company's commitment to quality and safety.
To conclude, CI in welding is not a one-time effort but a sustained journey toward excellence and reliability. Organizations that invest in CI welding practices cultivate an environment where innovation, quality, and trustworthiness flourish. By leveraging the latest technologies and adhering to stringent standards, they not only meet but often exceed the expectations of their customers. This commitment to continuous improvement fosters a culture of excellence, ensuring that their products are both safe and reliable, ultimately solidifying their reputation as industry leaders.