Choosing the right cast iron welding rod size is crucial for successful welds in different applications. As an experienced welder or a DIY enthusiast exploring the mechanics of welding, understanding the significance of rod sizes can enhance your work’s quality and durability.
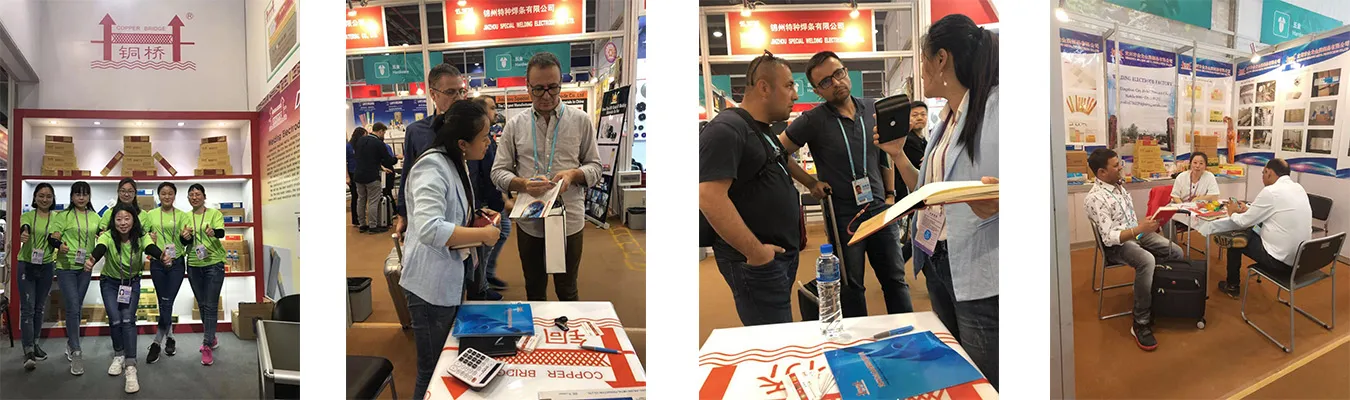
Experience shows that the size of a welding rod impacts not just the seam's quality but also the project's efficiency. For instance, larger rods are more suitable for bigger projects or thicker materials, as they facilitate a deeper penetration creating stronger joints. However, smaller diameters are ideal for more delicate tasks or thin materials, providing precision and minimizing heat distortion.
In terms of expertise, it's essential to know which sizes suit specific cast iron types. Cast iron varieties such as gray cast iron or ductile iron display different welding behaviors. Gray cast iron, for instance, tends to crack easily because of its high carbon content. Using a 3/32-inch or 2.5 mm rod offers more control and less heat input, reducing the risk of cracking. Conversely, ductile iron benefits from larger rods like 1/8-inch or 3.2 mm, allowing for efficient joining without sacrificing flexibility or strength.
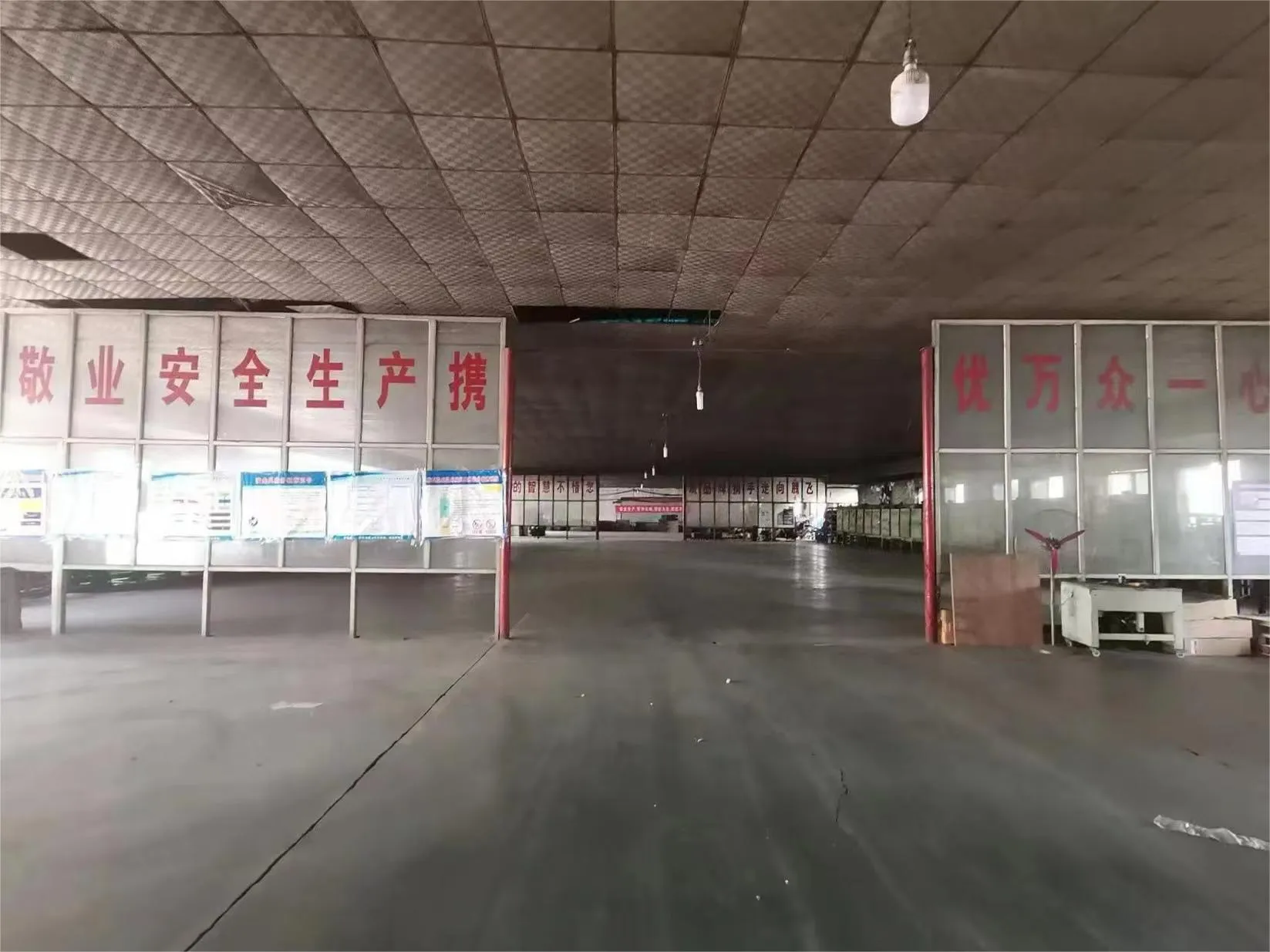
Authoritativeness in this field often comes from established welding authorities and material experts. Many recommend ESt (Nickel) rods for cast iron due to their compatibility and ability to produce malleable welds. The choice of size, like the 1/8-inch rod, balances between providing enough filler material and maintaining control over the welding process for both heavy-duty and mid-range applications.
cast iron welding rod sizes
Trustworthiness is built upon using proven techniques and listening to feedback from experienced professionals. It's advised by seasoned welders that practicing on scrap material before working on significant projects can perfect one's skill set and prevent costly errors. Testing how different sizes react with specific cast iron materials allows for adjustments in technique, ensuring that the end results meet the highest quality standards.
When matching rod sizes to specific welding machines, consideration of the machine's output and capability is essential. Larger machines, typically used in commercial or industrial settings, can handle larger rod sizes more effectively, whereas smaller, home-use machines may struggle. It’s vital to verify the compatibility to prevent overloading your equipment, which can lead to inefficient welding and damage to your tools.
An often-overlooked factor is the project environment itself. For outdoor or on-site welding jobs where environmental factors like wind could affect the arc, a larger rod size could provide steadier performance against variable conditions. Conversely, in controlled indoor environments, smaller rods could suffice, providing precision and maintaining the aesthetics of the welds.
In conclusion, determining the ideal cast iron welding rod size is not just a step in preparation, but an integral part of the welding process itself. By understanding the influence of rod size on different types of cast iron and project conditions, not only can better weld results be achieved, but the integrity and longevity of your work will also be significantly enhanced. For anyone serious about developing their craft, investing time in testing and training with different welding rods is invaluable, ensuring readiness to tackle any project with confidence and expertise.