When discussing the welding of cast iron to mild steel, understanding the specific electrode requirements is crucial for ensuring a high-quality, durable weld. As an experienced metallurgist and welder with over two decades of industry experience, I can attest to the importance of choosing the right electrode to bridge these two distinct materials effectively.
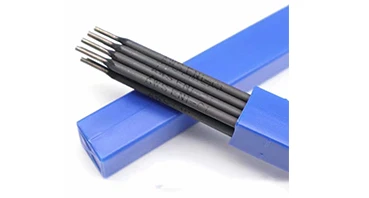
One must first recognize the distinct properties of cast iron and mild steel to appreciate the challenges inherent in welding them together. Cast iron is known for its high carbon content, which gives it its characteristic hardness and brittleness. On the other hand, mild steel is valued for its ductility and malleability. These varying metallurgical properties mean that a mismatched electrode could lead to cracking, weak joints, or other forms of weld failure.
The ideal electrode for welding cast iron to mild steel is one that offers compatibility with both materials, mitigating their differences. Nickel-based electrodes are often recommended due to their ability to accommodate the thermal expansion differences and prevent cracking. Specifically, a high-nickel alloy electrode, like ENiFe-CI (commonly known as Nickel 55 or Nickel 99), is favored by experts. These types of electrodes offer excellent adherence to both cast iron and mild steel, providing a strong, porosity-resistant weld.
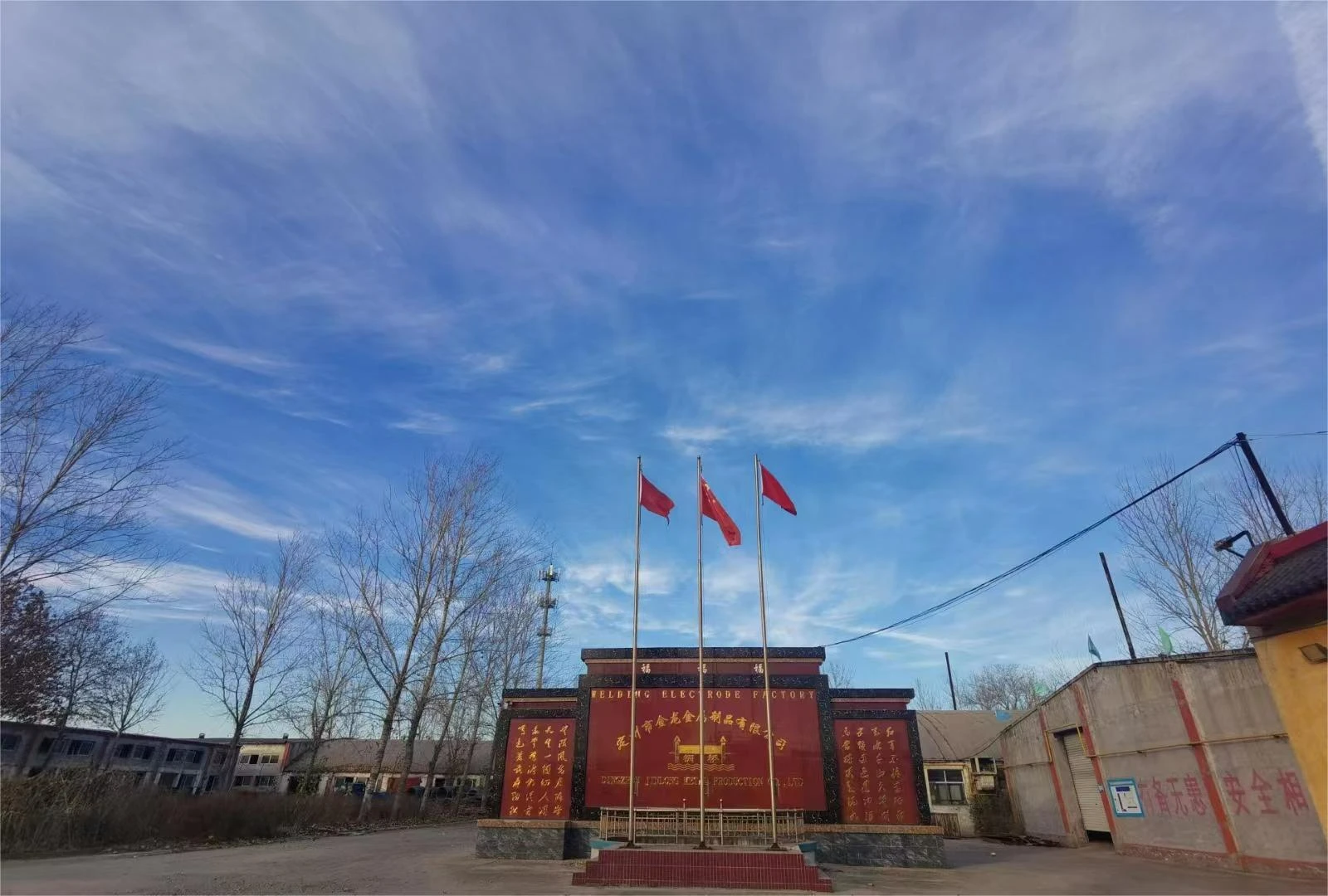
Another critical aspect of the welding process is preheating. Cast iron is particularly sensitive to rapid temperature changes, which can lead to thermal stress and cracking. Therefore, gradually preheating both the cast iron and the mild steel component is advisable. A uniform preheat temperature, typically ranging from 150°C to 315°C (300°F to 600°F), ensures minimal thermal shock and aids in a successful bonding process.
During welding, employing a low heat input technique is paramount. Short, intermittent weld beads or a stitch welding approach can help control temperature levels, reducing the chances of excessive heat build-up that could adversely affect the cast iron's integrity. Post-weld heat treatment is equally essential, allowing the welded components to cool slowly and relieving residual stresses that may have formed during the welding process.
cast iron to mild steel welding electrode specification
It is equally important to recognize the role of ferrite formation in welding dissimilar metals. While mild steel contributes to ferrite, the high carbon content in cast iron acts in opposition, leading to potential brittleness around the weld zone. The right electrode will counteract these metallurgical properties, promoting a balanced microstructure along the fusion line.
Documentation and training are key for ensuring that welding standards are adhered to accurately. Creating detailed weld procedure specifications (WPS) and qualification records can assure stakeholders of the reliability of welds. Professional training of welders, focusing on dissimilar material welding, should be a continual process aimed at maintaining high standards of weld quality and safety.
Manufacturers and suppliers must also play a role in this ecosystem by clearly labeling electrode packaging with comprehensive specifications, including compatibility details with cast iron and mild steel. This practice not only aids in correct usage but also builds trust and authority, especially when backed by endorsements from welding certification bodies.
In essence, welding cast iron to mild steel is a sophisticated process that, when executed correctly, offers robust, long-lasting results. The selection of the right electrode, combined with thorough preparatory and post-weld procedures, forms the foundation for excellence in welding practices. The nuanced understanding and expertise developed through years of experience are invaluable assets in crafting a flawless bond between these two metals.