Cast iron welding electrodes are specialized tools in the world of metallurgy and welding, offering unique benefits for repairing and joining cast iron materials. These electrodes have been meticulously developed to address the specific challenges associated with welding cast iron and are essential for professionals seeking to maintain structural integrity and aesthetic quality in their projects.
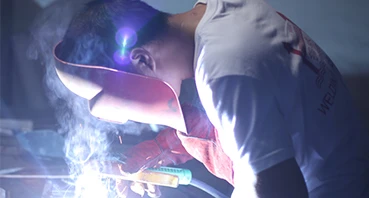
One of the key experiences in using cast iron welding electrodes is understanding the intricacies of working with cast iron itself. Unlike other metals, cast iron possesses a unique microstructure that includes carbon content in the form of graphite flakes within its composition.
This peculiarity can make traditional welding approaches problematic, often resulting in cracks or weak joints. However, cast iron welding electrodes are specifically designed to accommodate these graphite flakes, ensuring a robust and durable weld.
Professional welders often attest to the remarkable expertise required when handling cast iron welding electrodes. Selecting the correct type of electrode for a specific application involves knowledge about the different variants available, such as nickel-based or steel alloy electrodes. Nickel-based electrodes, for instance, are highly recommended for their robustness and ability to minimize cracking. Their exceptional thermal expansion properties align closely with that of cast iron, leading to a more harmonious bond. Conversely, steel alloy electrodes may be preferable in situations where the color match and machinability of the weld are critical.
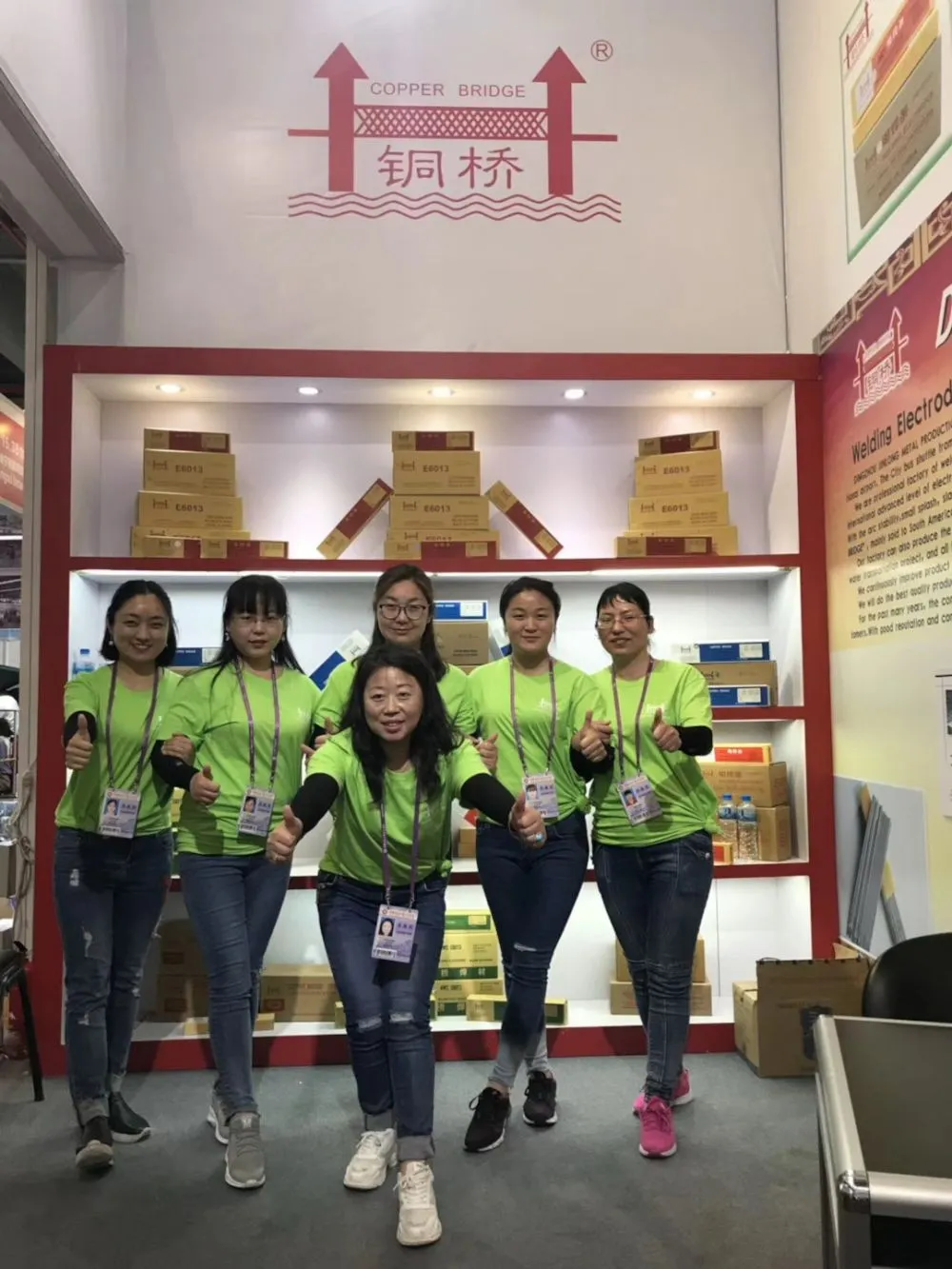
Authoritativeness in the field of welding with cast iron electrodes is supported by extensive research and documentation. Trusted sources, including manufacturers and educational institutions, have published detailed studies and guidelines on the optimal use of these electrodes. Such resources often highlight the importance of pre-weld and post-weld heating processes, crucial steps in avoiding thermal shock and reducing the likelihood of stress fractures. Pre-heating the cast iron part to a moderate temperature helps in alleviating temperature gradients that typically cause warping or cracking.
cast iron welding electrodes
Building trustworthiness around the use of cast iron welding electrodes also involves adhering to industry standards and practices. Certified welding professionals emphasize the necessity of adhering to best practices, such as maintaining clean work surfaces, employing proper welding techniques, and ensuring appropriate cooling periods. By following these guidelines, welders can produce consistent, reliable, and aesthetically pleasing welds, thus enhancing the trust of clients and stakeholders in their services.
Furthermore, field experiences underscore the advantage of using cast iron welding electrodes in a variety of applications, ranging from the repair of cast iron engine blocks to the restoration of vintage cast iron cookware. Each application benefits from the specific properties that these electrodes offer, such as improved corrosion resistance and superior tensile strength. This versatility is a testament to the electrode's ability to adapt to the varied demands of different industrial sectors.
In conclusion, cast iron welding electrodes represent a specialized but essential niche within the welding industry. Their development has been driven by the need to resolve specific challenges associated with cast iron, a material revered for its mechanical properties and historical significance. By leveraging their unique chemical compositions and adhering to established welding protocols, professionals can achieve high-quality, durable welds. Whether it is through practical experience, abiding by the expertise of industry leaders, or building on authoritative techniques, the effective use of cast iron welding electrodes remains a critical skill for achieving excellence in metalwork and repair projects.