The world of welding is both intricate and fascinating, with each material and tool demanding its own set of skills and knowledge. Among these tools, cast iron stick welding rods hold a significant place due to their unique properties and applications. Understanding the intricacies of using these rods can drastically improve your welding outcomes, making them indispensable for certain projects.
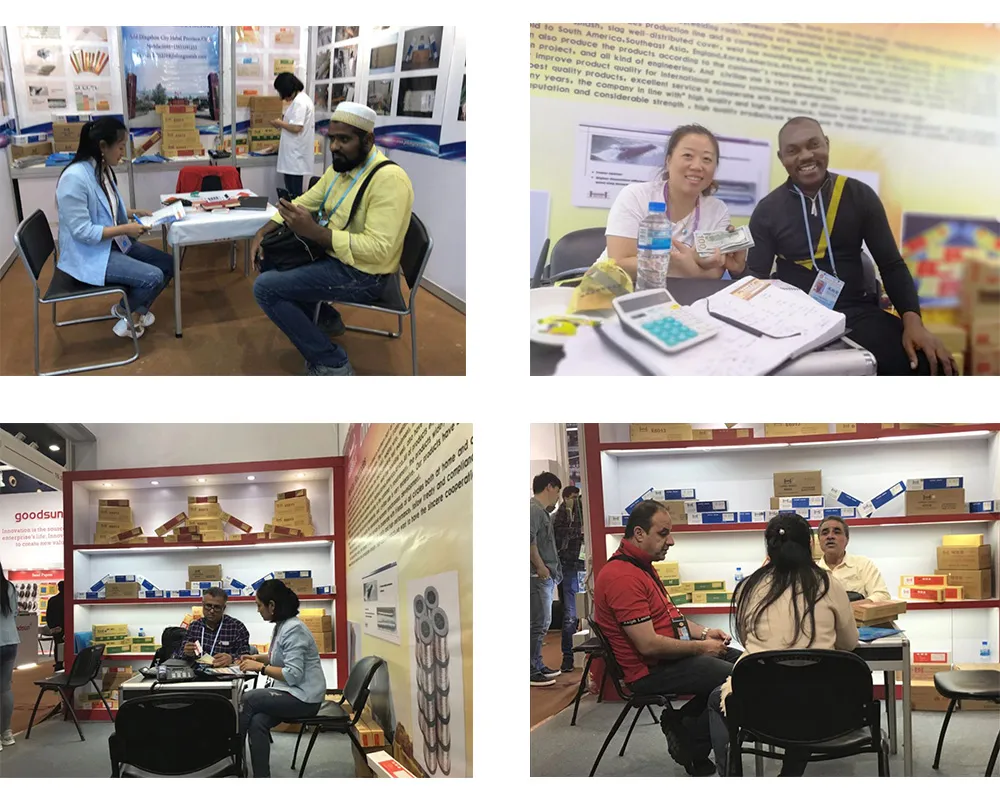
Cast iron, known for its durability and ability to retain heat, is a popular material in construction and manufacturing. However, welding cast iron can be challenging due to its brittle nature and high carbon content, often leading to cracking and other defects. This is where cast iron stick welding rods come into play, providing a viable solution to these challenges.
Experience in welding cast iron with stick welding rods reveals its importance in achieving a strong, reliable weld. Unlike other welding rods, those designed for cast iron often contain nickel, which helps accommodate the material's expansion and contraction during heating and cooling. Nickel inherently has properties that reduce the risk of cracking, offering more flexibility and a stronger bond with cast iron.
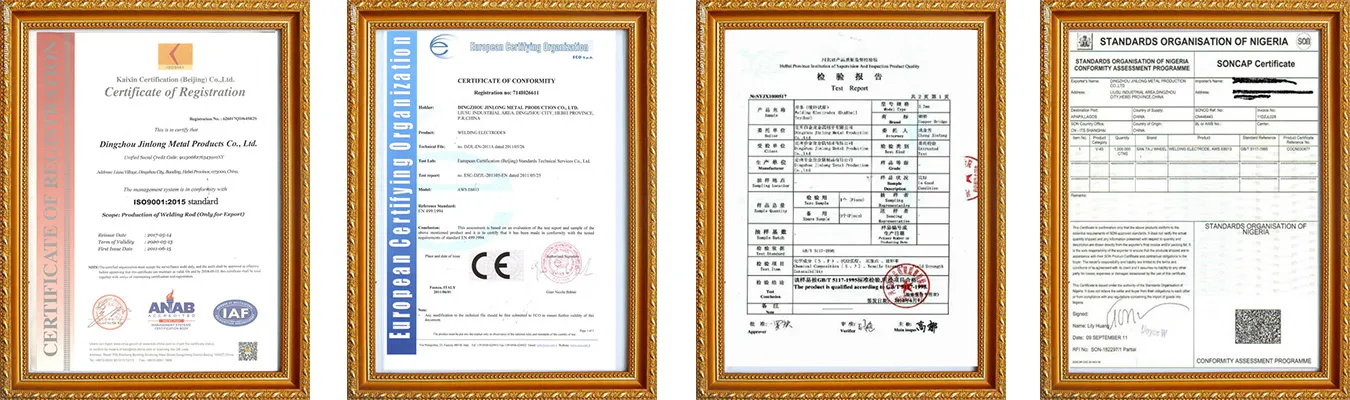
Expertise in selecting the right cast iron stick welding rod is crucial. There are generally two types of rods recommended for this material pure nickel rods and nickel-iron rods. The choice between the two depends largely on the specific requirements of your project. Pure nickel rods are typically preferred for welding cast iron to itself, as they provide the best machinability and color match. Nickel-iron rods, on the other hand, are more economical and can be used effectively when welding cast iron to steel.
Focusing on technique, preheating represents a critical step in the process. Preheating the cast iron helps reduce thermal shock, further minimizing the risk of cracking. The temperature required can vary based on the complexity and thickness of the piece, but a general guide is to heat the cast iron to between 500 and 1,200 degrees Fahrenheit prior to welding. Equally important is the cooling process; allowing the welded piece to cool slowly will ensure the integrity of the weld.
cast iron stick welding rod
Authoritativeness in cast iron welding with stick rods is also about understanding potential pitfalls and how to overcome them. One common issue is the porous nature of welds formed during the process. This can lead to weak points in the welded joint, which is undesirable in load-bearing or high-stress applications. Utilizing high-quality welding rods and maintaining a clean, consistent welding technique can mitigate these issues.
Trustworthiness in welding practices involves not only skill but a commitment to safety standards. Proper personal protective equipment (PPE), such as welding helmets, gloves, and aprons, should always be used to protect against heat, sparks, and harmful fumes. Furthermore, ensuring your work area is well-ventilated will reduce exposure to potentially hazardous gases generated during the welding process.
Incorporating these insights and practices fosters not only the quality and durability of the weld but also confidence in undertaking cast iron projects. The nuanced knowledge of how cast iron stick welding rods work, combined with technical expertise, is what sets skilled welders apart in the field.
Ultimately, the successful application of cast iron stick welding rods hinges on a balance of experience, knowledge, and attention to detail. Whether you are an experienced welder or a newcomer to the craft, understanding the specific demands of cast iron welding will enhance your capabilities and ensure superior outcomes in your projects. This commitment to excellence will inevitably lead to a stronger reputation and greater opportunities in the vast world of welding.