When it comes to achieving optimal results in metal fabrication, the choice of welding materials plays a critical role. One such material, cast iron, often presents a unique challenge due to its brittle nature and complex chemical composition. Utilizing cast iron electrodes for welding, however, has emerged as an effective solution, offering both strength and versatility for a variety of applications.
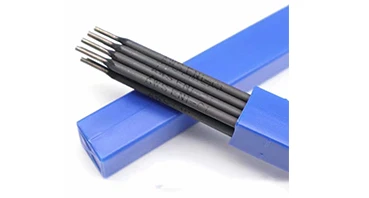
Cast iron, a group of iron-carbon alloys with a carbon content greater than 2%, is known for its excellent fluidity, castability, and machinability. However, its high carbon content also makes it prone to cracking during welding.
This is where cast iron electrodes come in. Specifically designed to manage the idiosyncrasies of cast iron, these electrodes provide a reliable means of welding that minimizes the risk of cracking and other structural issues.
One of the main advantages of using cast iron electrodes is their ability to effectively bond cast iron parts without compromising their integrity. These electrodes are generally coated with a special flux that not only stabilizes the arc but also protects the weld from contaminants. Furthermore, the coatings on these electrodes often contain nickel, copper, or other alloying elements that promote ductility and thermal expansion compatibility, essential factors in reducing residual stress and preventing fractures in the weld zone.
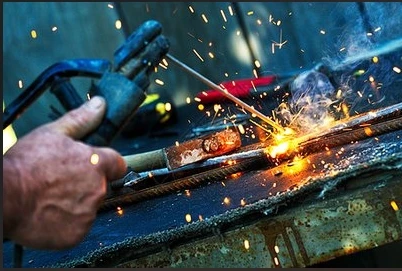
Experience with cast iron welding shows that electrode selection must align closely with the specific requirements of the workpiece. For instance, nickel-based electrodes are widely regarded as the best solution for joining cast iron to steel or for repairing worn parts. Their exceptional mechanical properties offer excellent strength, corrosion resistance, and a low coefficient of expansion—characteristics that help accommodate the inherent brittleness of cast iron.
cast iron electrode welding
Professional welders emphasize preheating and slow cooling as crucial steps in the cast iron welding process, facilitated by the use of suitable electrodes. Preheating the cast iron workpiece helps to reduce the temperature gradient between the weld and the surrounding metal, mitigating the risk of thermal stress. Slow cooling, on the other hand, is achieved by covering the welded piece with an insulating material, allowing the temperature to decrease gradually, which further aids in stress relief and crack prevention.
The authority of cast iron electrode welding lies in its proven track record across a multitude of industries, from automotive repair to industrial machinery maintenance. In scenarios where structural integrity is paramount, welders trust cast iron electrodes for their reliable performance and ability to produce high-quality joints.
Experts in the field continually stress the importance of adhering to best practices when welding cast iron. Beyond choosing the right electrode, consideration should also extend to factors such as electrode diameter, welding position, and technique. Techniques such as short, intermittent welds can minimize heat input and further decrease the risk of cracking, ensuring the longevity and durability of the welded structure.
In conclusion, cast iron electrode welding represents a specialized yet robust approach to working with one of the more challenging materials in the metalworking domain. Through a combination of expertise, precise material selection, and adherence to proven welding protocols, welders can successfully leverage the unique benefits of cast iron electrodes, achieving not only structurally sound welds but also enhancing the overall trustworthiness of their fabrication projects.