In the world of industrial applications and advanced electronics, the cast electrode serves as a cornerstone component, significantly influencing the performance and efficiency of various systems. Understanding its unique properties, manufacturing process, and applications can lead businesses and technicians to make informed decisions regarding their machinery and equipment investments.
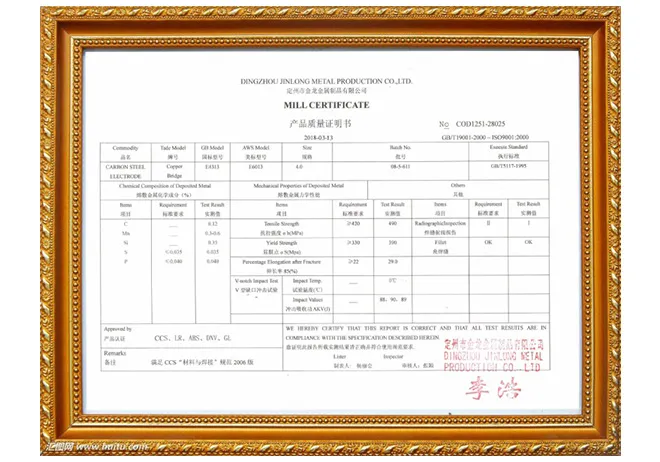
Cast electrodes are renowned for their stability and robustness, particularly in high-frequency welding, metallurgy, and advanced electrochemical processes. Made through a specific casting process, these electrodes are designed to withstand intense thermal and chemical environments, offering unparalleled longevity and consistency compared to other electrode types.
The production of cast electrodes involves a meticulous process where high-quality raw materials, such as pure metals or their alloys, are melted and poured into predefined molds. This technique allows for the precise control of the electrode's shape and size, tailor-fitted for specific industrial needs. The casting process not only ensures uniformity in composition but also enhances the grain structure of the metal, thus providing superior mechanical properties. This makes cast electrodes particularly advantageous in applications requiring high thermal conductivity and electrical efficiency.
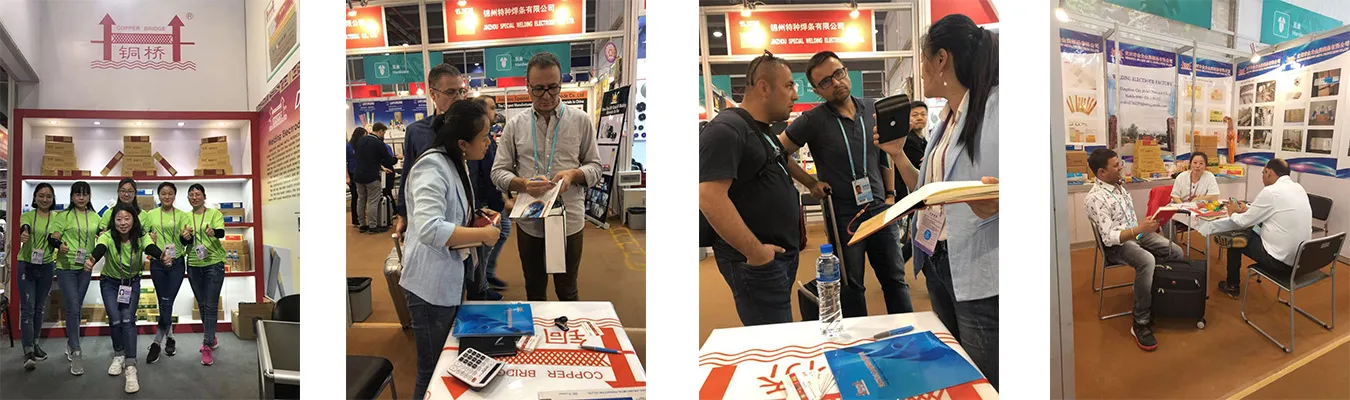
Expertise in the manufacturing process of cast electrodes is critical.
It requires a deep understanding of metallurgy and materials science. Professionals often employ advanced modeling techniques to predict the behavior of materials during the casting process, ensuring that the final product meets exact specifications and performs reliably under stress.
The applications of cast electrodes are vast and varied. In the welding industry, they are prized for their ability to deliver a stable arc, which is essential for producing clean and robust welds. Their capacity to maintain performance even in extreme temperatures makes them suitable for welding heavy-duty materials such as steel and aluminum.
In environmental and energy sectors, cast electrodes are employed in electrochemical systems, including batteries and electrolysis cells. Their durability ensures prolonged usage without frequent replacements, reducing maintenance costs and downtime. This is particularly critical in large-scale operations like power plants, where efficiency and reliability are paramount.
cast electrode
The authority of cast electrodes in these industrial applications is further underscored by their adoption in research and development settings. Laboratories experimenting with high-energy physics or developing advanced materials often rely on the precision and reliability of cast electrodes. Their performance directly influences the success of experiments and the development of new technologies.
Trust in cast electrodes comes from decades of proven performance and continual improvements in manufacturing technology. Manufacturers of these components often undergo stringent quality assurance tests to ensure that each piece meets industry standards. This commitment to quality is reflected in their widespread use across critical industries where failure is not an option.
Choosing the right cast electrode supplier is just as important as understanding its applications and benefits. It requires evaluating potential manufacturers' capabilities in producing high-quality electrodes, their track record of reliability, and their ability to adapt to custom specifications. Partnering with a reputable supplier ensures access to expert advice and ongoing support, which can be invaluable in optimizing production processes and improving overall system efficiency.
Investing in high-quality cast electrodes brings measurable benefits in the form of reduced electrical waste, enhanced system longevity, and improved product outcomes. Businesses aiming to maintain a competitive edge should consider the comprehensive advantages cast electrodes offer, from operational efficiency to reduced environmental impact.
Overall, the cast electrode is not just a component; it's a critical enabler of innovation and efficiency in modern industry. Its robust nature and versatile applications make it indispensable, and staying informed about advances in this field ensures that businesses can continue to thrive in an increasingly competitive and technologically advanced landscape.