Casting welding electrodes, specialized for welding metal castings, are critical components in manufacturing and repair industries. These electrodes are engineered to meet the unique challenges of joining cast materials, which are often characterized by their distinctive metallurgical compositions and mechanical properties.
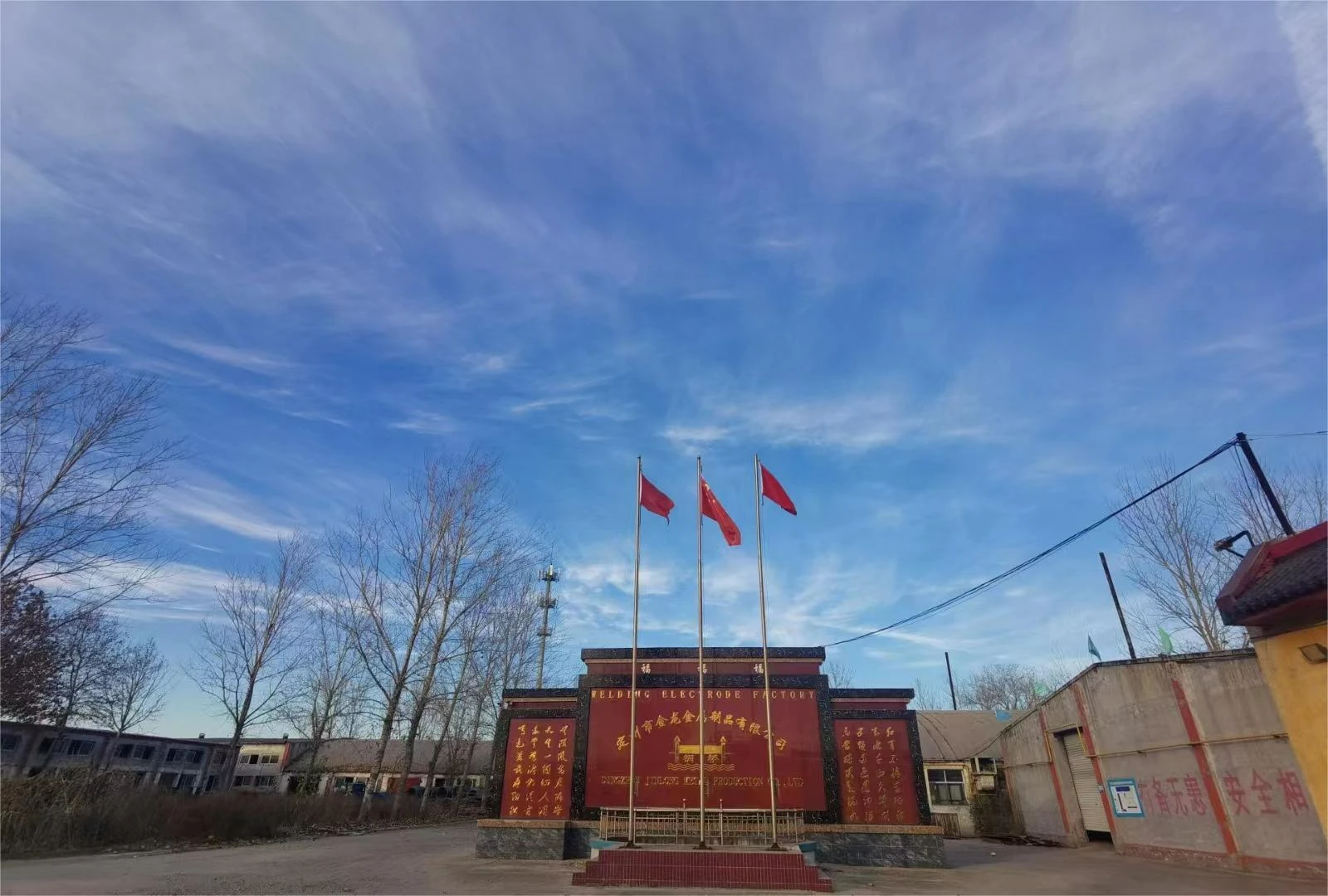
Understanding the intricacies of casting welding electrodes requires diving into their functionality and applications. First, consider the types of metals typically associated with casting welding. Iron, steel, and aluminum are common in foundries, each demanding specific electrode formulations to ensure strong, reliable welds. The ability of an electrode to facilitate proper fusion between these materials and other metals makes it an indispensable tool in industries ranging from automotive to heavy machinery repair.
The key to effective electrode performance lies in its coating composition. A well-formulated coating stabilizes the arc, minimizes spatter, and ensures a smooth weld bead. It might include elements like fluxes that help in deoxidizing and cleaning the weld area, shielding gases that protect the molten weld from atmospheric contamination, and binders that facilitate easy handling and even melting. This coating not only aids in achieving a clean weld but also provides corrosion resistance and mechanical strength—qualities that are crucial when working with cast metals.
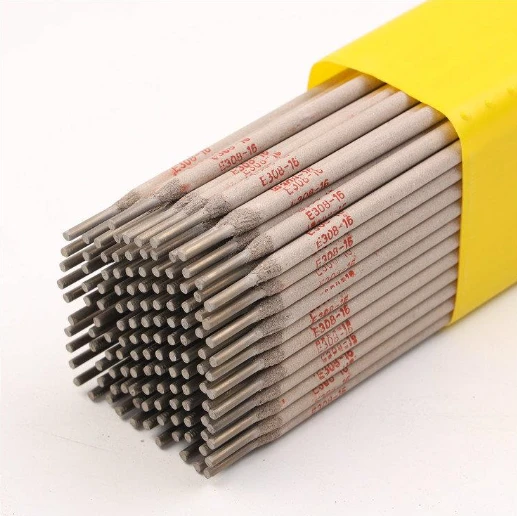
Professional welders recognize that selecting the right electrode goes beyond mere compatibility. It's about adapting to specific casting imperfections—such as gas porosity, shrinkage cracks, and inclusions—that can complicate the welding process. Crafting a weld over these inconsistencies requires electrodes that support versatile welding positions and allow for control over penetration and bead shape. Experts often prefer electrodes with a higher tensile strength to match or exceed that of the casting material, creating a joint that withstands operational stresses over time.
Moreover, electrodes must cater to the specific welding technique being employed, whether it's MIG, TIG, or stick welding. For instance, in TIG welding, the electrode must withstand high temperatures while maintaining its integrity, thus necessitating the use of tungsten—a material renowned for its high melting point and electron stability. In contrast, stick welding might benefit from a cellulose coating for deep penetration or a mineral-based coating for a smooth finish.
casting welding electrodes
Experience tells us that trustworthiness in welding equipment is non-negotiable. Professionals rely on brands with a proven track record of quality assurance and adherence to industry standards. Certifications from organizations like the American Welding Society (AWS) signify that electrodes have undergone rigorous testing, further affirming their reliability.
Not only is product quality paramount, but so is the support and expertise of the supplier. A reputable supplier offers guidance on electrode selection and provides insights grounded in a thorough understanding of casting materials and welding techniques. This knowledge base enables end-users to maximize their welding outcomes, minimizing downtimes and material wastage.
Modern advancements in manufacturing technology have pushed the boundaries of welding electrode capabilities. Today's electrodes are designed to accommodate cutting-edge industrial applications that demand precision and adaptability. Smart coatings and innovative materials have become more prevalent, marking a shift towards electrodes that deliver enhanced performance while supporting environmentally sustainable practices.
As industries evolve, so does the demand for specialized electrodes that meet increasingly complex technical requirements. Welding professionals must remain abreast of these evolving technologies to ensure they're employing electrodes that align with the latest advancements in metallurgical engineering and casting technologies.
In conclusion, casting welding electrodes embody the intersection of material science and practical application. Their role is not merely functional but strategic, bolstering the structural integrity of welded components. Their selection represents a critical decision with far-reaching implications for the quality and longevity of metal castings. A profound understanding of casting welding electrodes—rooted in a blend of technical knowledge, practical experience, and industry trust—lies at the heart of successful welding operations.