Understanding the nuances of using a casting to mild steel (MS) welding rod requires an exploration into the characteristics, applications, and best practices involved in this realm of metalworking. Cast iron and mild steel are both widely utilized materials in the industry, yet they differ significantly in composition and properties, making their welding an intriguing subject for professionals and hobbyists alike. This article delves into using welding rods specifically designed for casting to MS transitions, emphasizing experiential insights, technical expertise, authoritative guidelines, and trustworthy recommendations.
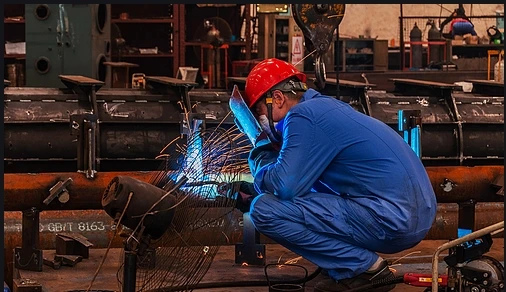
To begin with, welding is essentially a metallurgical process where two materials are joined through the application of heat and pressure. The challenge with welding cast iron to mild steel lies in their distinct carbon contents. Cast iron has much higher carbon levels compared to mild steel, resulting in differences in melting points and thermal expansion rates. A specialized welding rod is crucial in bridging this gap, typically made with a composition that includes nickel or a nickel-iron blend, which accommodates the dissimilarities between these materials.
In practice, a chairperson in welding workshops will often recommend nickel-based electrodes for casting to MS applications, such as the AWS A5.15 ENiFe-Cl, due to their versatility and ability to mitigate common issues. Nickel has a lower melting point and offers excellent ductility, which helps in soaking up stresses that occur due to differential thermal expansion.
Using such rods results in a weld that is more resilient to cracking and other defects. Noteworthily, operators must be keen on controlling the heat input by employing short arcs and low amperage to avoid overheating the cast iron.
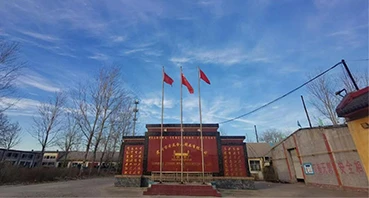
From an expert's perspective, preparation is pivotal. The surfaces of the materials should be cleaned thoroughly to remove any oils, paints, or rust, ensuring optimal fusion. Preheating is another crucial step, particularly for the cast iron component, as it minimizes the thermal shock during welding. A slow cooling process is equally critical post-welding, often achieved by wrapping the welded piece in insulating materials like sand or lime. These processes require precision and patience but dramatically improve the integrity of the weld.
casting to ms welding rod
Authority in welding practice extends beyond mere technique; it involves comprehensive understanding and adaptation to specific use-cases. For example, when repairing machinery with cast components, welding reliability is non-negotiable. In such scenarios, selecting a nickel-rich rod ensures that mechanical stresses do not undermine the joint's strength. Similarly, structural applications involving cast reinforcements often demand rigorous assessment of the weld quality, achieved through non-destructive testing methods such as ultrasonic testing or radiography.
Reliability and trustworthiness in welding with casting to MS rods come from adherence to industry standards and continuous education. Staying abreast with manufacturers' guidelines for welding rods and incorporating technological advancements, such as new protective gas mixtures or updated procedural standards, fortifies the process against failures.
Finally, experiential insights reveal that successful casting to MS rod applications boast a symphonic blend of foundational principles and tailored adjustments. On-the-ground reports suggest that maintaining a flexible approach—one that considers project-specific variables and real-time challenges—is indispensable. This experiential learning process not only refines individual skill sets but also contributes to the collective expertise within the welding community.
In summary, using a casting to MS welding rod is an intricate task that requires technical proficiency, authoritative insight, and an unwavering commitment to safety and quality. Whether for repair, structural, or fabrication purposes, the effectiveness of these welding rods hinges on careful preparation, appropriate technique, and constant learning. By amalgamating experienced insights, expert evaluations, authoritative standards, and trustworthy practices, one can ensure superior outcomes in this complex yet rewarding facet of welding.