AWS E7018 welding rod is an essential tool in the realm of professional welding, utilized extensively across various industries due to its unique characteristics and superior performance. This electrode is renowned for its ease of use, strong welds, and adaptability in different environments, making it a favorite among professionals seeking reliable and consistent results.

The AWS E7018 welding rod is a low-hydrogen, iron powder electrode known for its versatility and strength. It is particularly suited for welding carbon steel and low-alloy steel, offering excellent mechanical properties and strong resistance to cold cracking, which is crucial for projects demanding high structural integrity and reliability. The low hydrogen content in this rod is critically important as it reduces the risk of hydrogen-induced cracking, a common problem faced in steel welding.
In practice,
the usability of the E7018 is well-appreciated in situations where multiple pass welding is required. This rod is known for its smooth arc, minimal spatter, and easy slag removal, which collectively contribute to higher productivity and cleaner welds. These features significantly reduce post-weld cleaning time, thereby increasing overall efficiency for welders and fabricators.
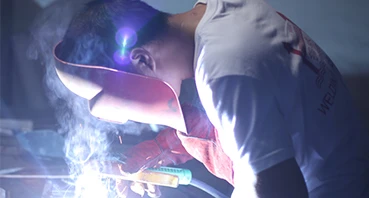
The versatility of the E7018 welding rod is underscored by its suitability for both AC and DC welding, catering to a wide range of welding machines and techniques. This flexibility makes it an indispensable component in sectors such as construction, shipbuilding, and pipeline welding, where diverse welding tasks are the norm.
In environments where site conditions vary widely, the E7018 maintains performance integrity, allowing welders to work with confidence even in challenging conditions. It performs exceptionally well in both indoor and outdoor settings, standing up to environmental factors that might otherwise compromise welding quality. This performance consistency ensures that projects are completed within tight timeframes without sacrificing the quality or durability of the welds.
aws e7018 welding rod
The mechanical properties of welds created with E7018 rods are among the best available. This electrode produces welds with tensile strengths typically exceeding 70,000 psi, which are crucial for high-strength applications. Additionally, its excellent ductility and impact toughness at low temperatures make it suitable for dynamic and high-stress applications, including heavy machinery and structural steel.
One of the distinctive aspects of the E7018 rods is their coating, which contains iron powder and low hydrogen compounds. This coating contributes to the electrode's exceptional deposition rate, improving efficiency on large projects. It also aids in producing a stable arc with less need for operator intervention, further enhancing productivity and reducing operational fatigue.
Expertise in using AWS E7018 welding rods comes with understanding and adapting to its storage requirements. The rods must be kept dry and at recommended temperatures to maintain their low-hydrogen properties. Manufacturers often suggest storing these electrodes in heated cabinets to prevent moisture absorption, which can diminish their effectiveness and lead to potential failures in the welds.
Many professionals gain their authority and trust in using these rods through certification and training, usually provided by welding institutions or manufacturers. These programs emphasize the importance of technique, rod handling, and environmental considerations to ensure optimal outcomes. Acquiring proficiency with E7018 rods not only enhances a welder's skills but also assures clients of the quality and reliability of the welds produced.
In summary, the AWS E7018 welding rod stands as a testament to technological advancements in welding materials, offering both versatility and performance that meet rigorous industrial demands. Its widespread use across various industries highlights its authority in the market. The rod’s ability to produce strong, reliable, and aesthetically pleasing welds guarantees its continued relevance and trustworthiness among welding professionals worldwide.