When it comes to selecting materials for construction and fabrication, understanding the distinct properties and applications of both ER6011 and ER7018 welding rods is crucial. Each of these electrodes offers unique advantages and limitations, making them suitable for different tasks within the realm of structural and heavy-duty welding. A profound knowledge of these can benefit welders, contractors, and engineers, ensuring both performance and safety.
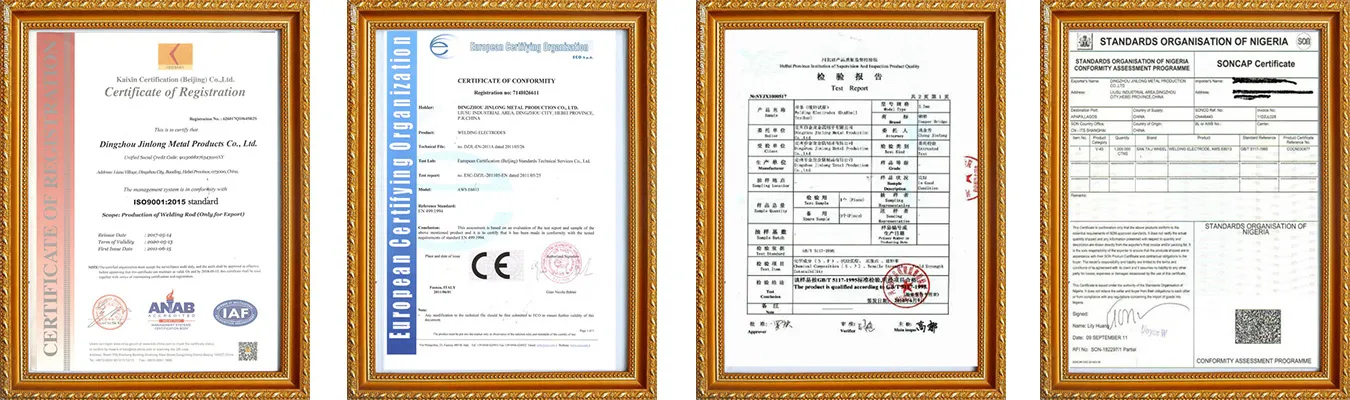
ER6011 electrodes are a popular choice among welders due to their versatile nature and deep penetration abilities. These features make them particularly effective for welding through rust, oil, paint, and dirt. They produce a forceful arc capable of cutting through challenging surfaces, which is why they are predominantly used in maintenance and repair welds. The fast-freezing characteristic of the slag is advantageous for vertical and overhead positions as it minimizes drips and enhances control. However, it’s worth noting that the bead appearance from ER6011 can be quite rough compared to others, which may necessitate additional grinding for aesthetic purposes.
On the other hand, ER7018 electrodes are celebrated for their smooth, clean welds. They are often the go-to for structural welding tasks, particularly when working with carbon steel. Known colloquially as low hydrogen rods, ER7018 electrodes minimize the risk of hydrogen-induced cracking, a critical feature when ensuring the longevity and integrity of metal structures. The welds produced are not only visually appealing but also incredibly strong and ductile. That said, ER7018 electrodes do demand dry storage conditions to avoid moisture absorption, which can otherwise lead to weld defects.
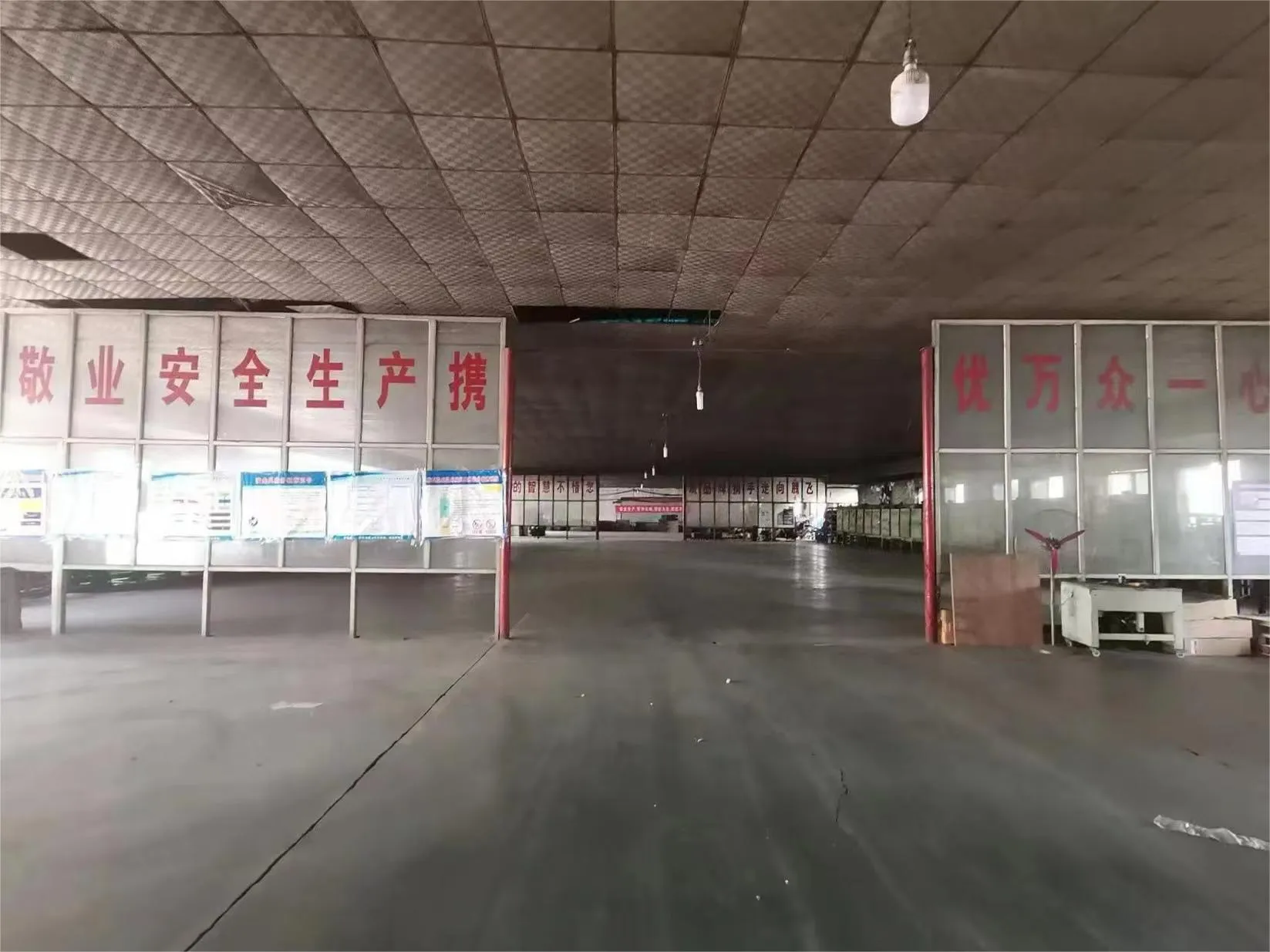
Both ER6011 and ER7018 serve as authoritative examples of specific-use electrodes within the welding community. The expertise required to utilize these electrodes effectively involves not only understanding their chemical and mechanical properties but also executing proper safety standards and environmental considerations.
When choosing between ER6011 and ER7018, welders must assess the project requirements meticulously. ER6011's robust penetration and adaptability make it ideal for outdoor, unclean, or variable conditions. Alternatively, ER7018’s reliability and strength make it the preferred choice for high-strength structural welds where appearance and crack resistance are paramount.
6011 or 7018
Furthermore, the difference in current versatility adds another layer to the decision-making process. ER6011 can be used with both AC and DC currents, offering flexibility in terms of equipment and power sources, whereas ER7018 is generally better suited for DC applications to maintain its composition integrity.
Experienced welders understand the importance of maintaining a high level of authoritativeness in their practice, which comes from continuous learning and adaptation to technological advancements in electrode compositions and welding techniques. They leverage their expertise to decide whether the depth of penetration from an ER6011 outweighs the clean bead of an ER7018 for a specific project.
Trust is another critical aspect when discussing electrode choices. Professional welders and industries alike must have confidence in the materials and their applications. This trust is built over years through rigorous testing, adherence to standards, and a track record of successful applications. Both ER6011 and ER7018 have stood the test of time, providing reliable and trustworthy performance across numerous industrial applications.
Ultimately, the choice between ER6011 and ER7018 electrodes should be guided by a combination of experience, expertise, and project-specific demands. Welders confident in their abilities can draw from their authoritative knowledge to select the right tool for the job, ensuring safety, efficiency, and high-quality results in their welding endeavours.