The 70s6 welding wire is a crucial component in the toolkit of any welder looking to achieve high-quality results, especially in the field of gas metal arc welding (GMAW). Its unique composition and properties make it an ideal choice for a variety of applications, from industrial projects to artistic metalwork. Understanding the expertise required to use this material effectively can significantly impact the quality of welds and the satisfaction of clients.

Crafted for precision and durability, 70s6 welding wire is primarily composed of manganese and silicon, which work synergistically to improve the mechanical properties of the weld. This specific composition enhances the wire’s ability to produce smooth, clean welds with excellent penetration, reducing the need for post-weld cleaning and making it a cost-effective choice for large-scale operations. Such characteristics are crucial in industries that demand high standards, such as automotive manufacturing and structural steelwork.
The expertise in using 70s6 welding wire lies in fine-tuning the welding parameters to suit the material. Experienced welders will note its ability to maintain arc stability, which minimizes spatter and reduces defects. Proper technique involves adjusting the voltage and amperage to accommodate the thickness of the materials being joined, as well as controlling the wire feed speed to ensure consistency. Mastery of these variables can lead to significantly improved weld quality, enhancing structural integrity and longevity.
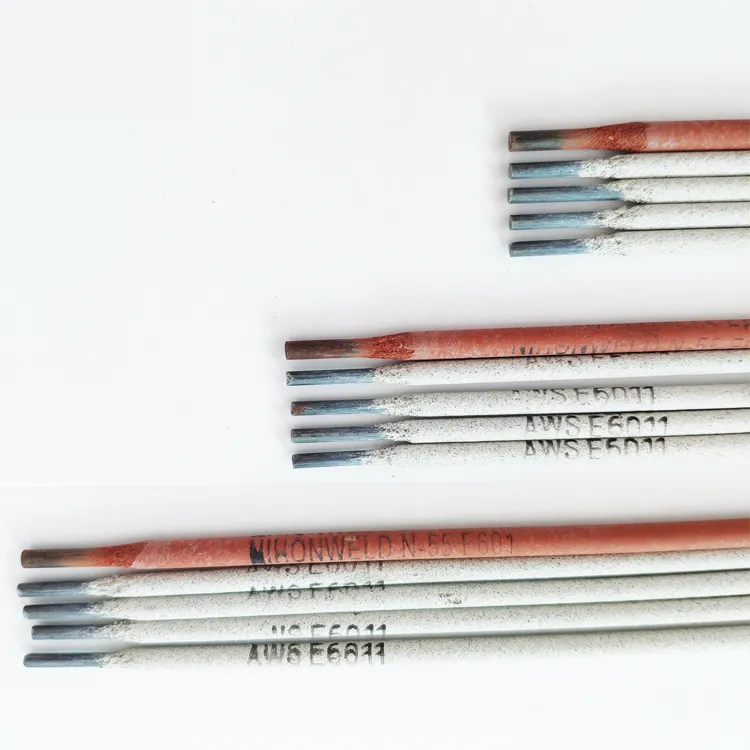
An authoritative voice in the industry, the American Welding Society recognizes the value of 70s6 wire due to its ability to adhere to stringent standards while still offering versatility. It meets the AWS ER70S-6 specification, which speaks to its excellent tensile strength and yield properties, making it suitable for both thin-gauge and heavy workpieces. This recognition by a reputable organization highlights its reliability and builds trust among professionals seeking materials that comply with industry regulations.
70s6 welding wire
Trustworthiness in welding products is paramount, and choosing a manufacturer known for quality control is essential. Optimal performance of 70s6 wire can only be assured when purchased from trusted brands that adhere to consistent production standards. These manufacturers provide certifications that ensure each batch matches the chemical and mechanical attributes required for demanding welding tasks.
Equipped with knowledge from seasoned professionals, welders can maximize the potential of 70s6 welding wire by incorporating best practices gathered from practical experience. This includes pre-weld preparation such as cleaning the base metal to avoid contamination and using the right shield gas mix to prevent oxidation during the welding process. Maintaining the equipment, such as keeping the welding torch in good condition, also plays a vital role in achieving optimal results.
For professionals in the welding industry, mastering the use of 70s6 welding wire can yield not only high-quality welds but also enhanced career opportunities. By continuously improving their technique and staying informed about advancements in welding technology, welders ensure they remain competitive in a field that values precision and efficiency. In conclusion, 70s6 welding wire represents a blend of professional expertise, trusted quality, and authoritative standards, making it an indispensable element in the world of modern welding.