The 7018 welding rod stands as a staple in the welding industry, recognized for its versatility and reliability in a wide range of applications. Its characteristics render it particularly suitable for structural welding projects, which require high tensile strength and moderate ductility. Understanding the applications and correct usage of the 7018 rod enhances workflow efficiency, guarantees robust structural integrity, and aligns with the best practices advocated by welding professionals.
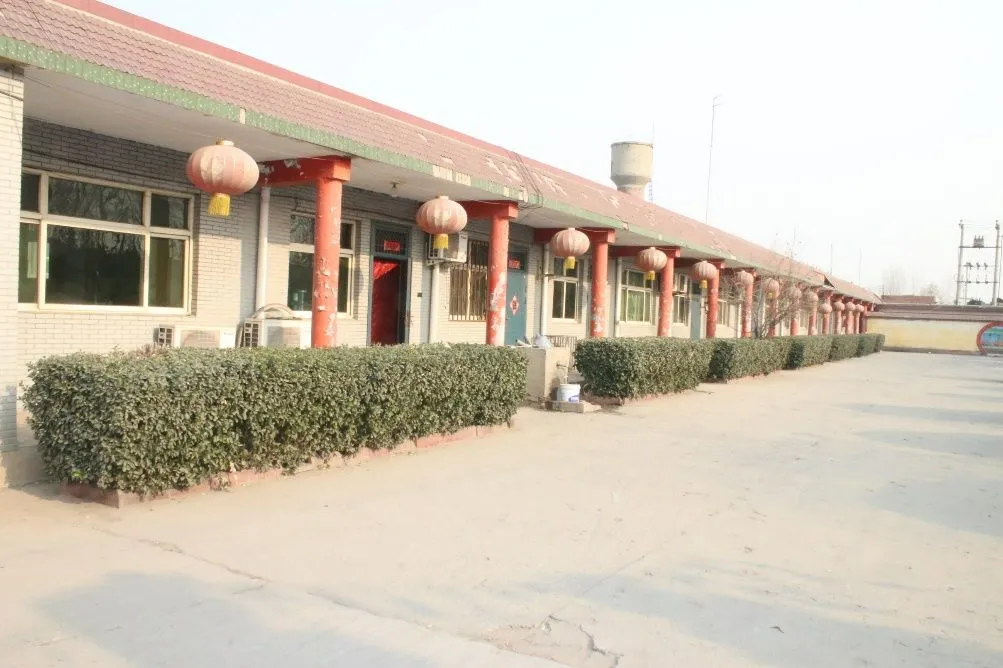
The intrinsic value of the 7018 welding rod lies in its chemical composition and mechanical properties. Comprising a low-hydrogen iron powder coating, the rod's formulation minimizes hydrogen inclusion during the weld, mitigating the risk of crack formation. This characteristic is of paramount importance in environments susceptible to freeze and thaw cycles or subject to dynamic loading. By reducing the hydrogen content, the 7018 rod ensures welds are less prone to embrittlement, thereby increasing the durability and safety of the structure.
Expert welders often select the 7018 welding rod for its exceptional usability across various steels, particularly in piping, pressure vessels, bridges, and structural components. This electrode is compatible with AC and DC currents, which adds to its flexibility. Its deposition rate is high, allowing for increased efficiency on large-scale projects. The rod’s ease of use also extends to its slag removal — the slag typically peels away effortlessly, thereby reducing post-welding clean-up time and maintaining aesthetic weld beads.
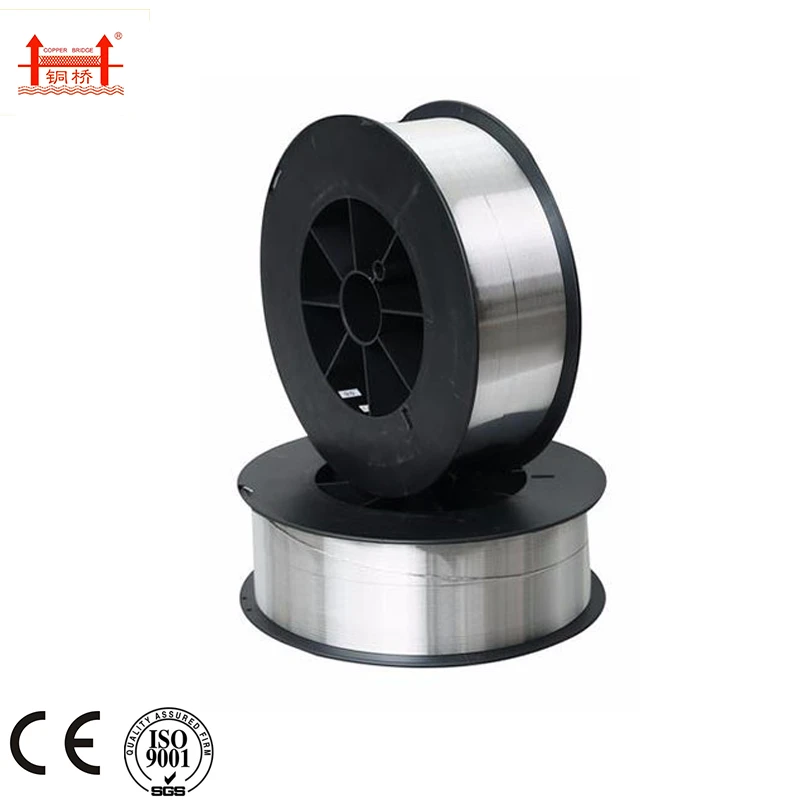
To optimize performance,
proper storage of the 7018 welding rod is critical. One common challenge with this electrode is its susceptibility to moisture absorption. Moisture can lead to hydrogen-induced cracking, undermining the integrity of the weld. Therefore, it is recommended to store these rods in temperature-controlled environments, preferably using a rod oven heated between 250°F to 300°F. This practice is not just an industry standard, but a necessity in projects demanding high safety standards.
In practice, utilizing a 7018 welding rod requires an understanding of the settings best suited to the project at hand. Welders should adhere to the correct amperage — generally spanning from 90 to 150 amps for electrodes of 1/8-inch diameter — to avoid issues such as excessive spatter or insufficient penetration. Mastery in adjusting these parameters ensures optimal weld quality and aligns with procedural norms outlined in welding codes and specifications, such as those from the American Welding Society (AWS).
7018 welding rod used for
The role of the welder cannot be overstated. Skilled professionals are aware that achieving the best results with a 7018 requires not only the correct equipment settings but also proficient technique. Such expertise involves maintaining a steady travel speed and correct rod angle — typically between 5 and 15 degrees from vertical — to ensure the weld pool is adequately controlled, thus avoiding defects like undercutting or overlapping.
Another dimension to the 7018 rod's utility is its contribution to sustainable welding practices. Minimal defects mean reduced waste, conserves materials, and lowers production costs, aligning with environmentally conscious operational standards. Additionally, high-quality welds contribute to longer-lasting structures, reducing the need for repairs or replacements and supporting ecological sustainability.
Understanding the utility of a 7018 welding rod extends beyond its application; it involves comprehending the broader implications of its use in enhancing project outcomes. Engineers and project managers recognize that the reliability of such a welding rod translates to time and cost savings, but more importantly, it can significantly influence safety and structural soundness. This understanding builds authority and trust, as decisions grounded in robust data and experience lead to successful project execution and longevity.
The 7018 welding rod remains a benchmark of reliability in the industry, embodying a blend of technology and craftsmanship. By adhering to the recommended guidelines for its application and storage, professionals can maximize the advantages this electrode offers. Its importance transcends mere function, reflecting values of quality assurance, sustainability, and operational excellence. For those invested in quality welding outcomes, the strategic use of 7018 rods plays a pivotal role in achieving structural masterpieces destined to stand the test of time.