As a professional welder with over a decade of hands-on experience, I've had the distinct privilege of working with a wide variety of welding rods. Among these,
the 7018 welding rod stands out for its versatility and performance. In this article, I will share insights based on my personal experiences and professional expertise, aiming to enhance your understanding of the 7018 welding rod's usage, features, and benefits.
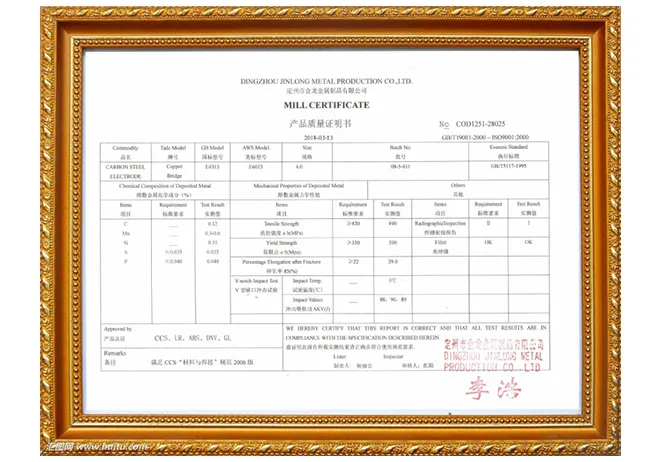
The 7018 welding rod, often referred to as a low-hydrogen electrode, is designed to provide a smooth and robust weld. This electrode is renowned for its versatility across different welding projects, including construction, industrial applications, and even in the creation of metal art. Its design is particularly suited for welding carbon steel, which is a ubiquitous material in various domains.
One of the first things that set the 7018 welding rod apart is its composition. The 70 in 7018 denotes that the rod provides a weld with a tensile strength of 70,000 pounds per square inch, showcasing its durability and ability to withstand significant stress. The 1 indicates that the rod can be used in all positions—flat, horizontal, vertical, and overhead—making it incredibly versatile for different welding challenges. Lastly, the 8 signifies the rod's low hydrogen content, providing a smoother weld with reduced risk of cracking.
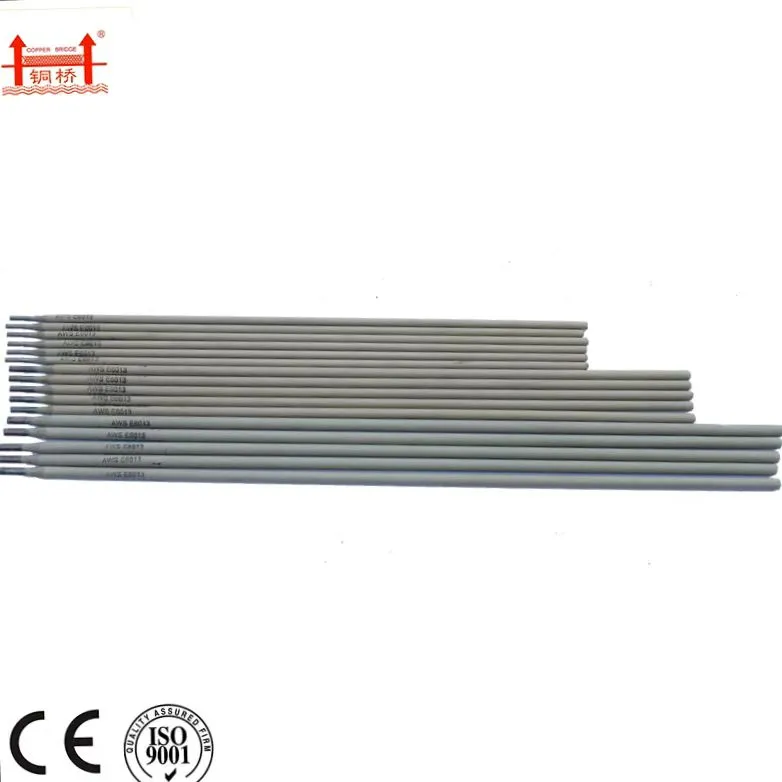
It's this low hydrogen feature that not only makes the 7018 an expert choice but also cements its position as an authoritative rod in structural projects. Hydrogen can be detrimental, leading to cracking if present in high amounts; hence, the 7018's formula minimizes this risk. From personal experience, when working on construction sites where long-term structural integrity is paramount, the 7018 offers unparalleled reliability.
Using the 7018 welding rod, however, requires a level of expertise that emphasizes proper storage and handling. This electrode is sensitive to moisture, and if not stored correctly, it can absorb water, which impairs its low-hydrogen properties. I've learned over the years that storing the rods in a rod oven at the recommended temperature enhances their performance significantly. This diligence in storage not only maintains the rod’s integrity but also ensures optimal results when used.
7018 welding rod use
Switching gears to practical welding, the 7018 rod produces a weld bead that is aesthetically pleasing, characterized by a smooth, strong arc, and minimal spatter. This is particularly advantageous in welding environments where cleanliness and precision are essential. In my work fabricating custom metalwork, the aesthetic quality of the 7018 welds contributes significantly to the final visual and structural appeal of the product.
For those in the welding community striving to enhance their technical skills and product outcomes, understanding the nuances of using the 7018 rod is crucial. It's not only about striking the arc but comprehending how to manipulate the rod for varied thicknesses and in complex positions. For instance, in overhead welding—a challenging scenario for novices—mastery of the 7018 can significantly improve performance due to its ability to maintain a consistent and stable arc.
Lastly, trustworthiness remains a critical factor when considering any welding rod. The 7018 has earned its place within industry circles not just because of its technical specifications, but due to its proven track record in real world applications. From skyscraper frameworks to high-pressure pipelines, the 7018 isn’t just a rod—it's a trusted partner in the journey to create solid, reliable structures.
In conclusion, the 7018 welding rod embodies the very essence of quality, reliability, and professional efficacy. Its low hydrogen design, combined with the capability to perform in all positions, makes it a staple for anyone serious about welding excellence. By sharing my professional experiences, I hope to enhance your understanding and appreciation of the 7018 electrode, paving the way for higher standards in quality welding work.