Navigating the world of welding can be daunting, especially when you're tasked with understanding the intricacies of a specific weld like the 7018. This rod type is renowned for its robust performance in various engineering and construction projects, making it a staple in the welding community. However, to truly capitalize on its features, one must delve into its unique characteristics and applications, fostering a deep comprehension that transforms work quality and efficiency.
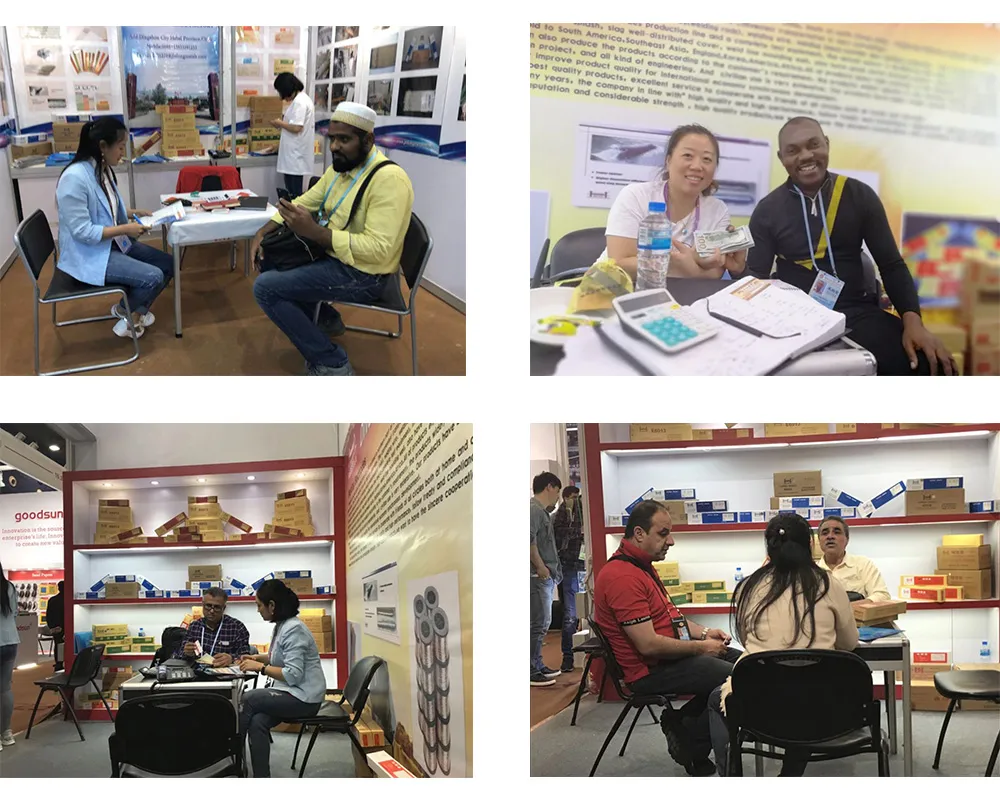
1. Understanding the 7018 Weld Rod
The 7018 weld rod is a low-hydrogen, iron powder electrode that has become synonymous with strength and reliability. Engineered for carbon and low-alloy steels, it boasts a tensile strength of 70,000 psi, making it ideal for heavy-duty projects. Its low-hydrogen content minimizes the risk of hydrogen-induced cracking, a common pitfall in other welding processes. The 7018 rod's dual function as both structural strengthener and stress reliever under high loads makes it indispensable.
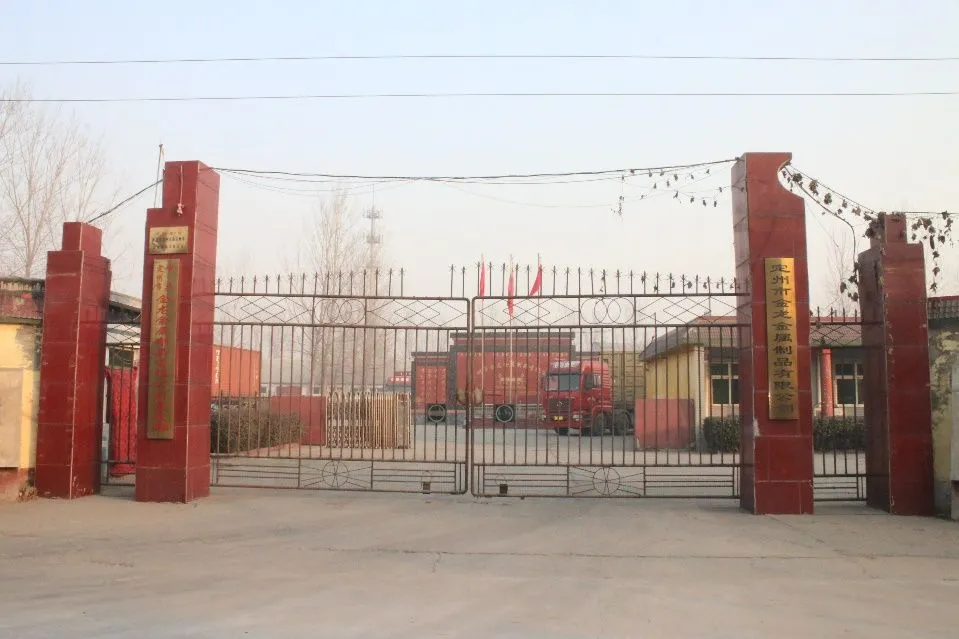
2. Application Domains
7018 weld rods thrive in industries requiring high structural integrity, such as shipbuilding, pipelines, and infrastructure projects. Their ability to perform steady welds under challenging conditions, such as vertical and overhead positions, enhances their desirability. Additionally, 7018 rods are frequently employed in the repair and maintenance of worn or damaged iron and steel parts, ensuring long-lasting joins without compromising on safety.
3. Expert Techniques for Effective Utilization
For optimal use, pre-weld preparation is crucial. It begins with baking the electrodes at a temperature ranging from 250°F to 300°F (120°C to 150°C) to eliminate any residual moisture, preventing unwanted hydrogen inclusion. This step is vital in achieving premium weld quality.
When welding, employing a slight drag technique allows for a molten pool to form and consistently penetrate the metal. Experts emphasize maintaining a stable, steady arc and ensuring the rod is kept at the correct angle to the work surface, typically around 15-30 degrees from the vertical. Such meticulous attention to technique helps capitalize on the rod’s characteristics, ensuring superior results.
7018 weld
4. Challenges and Overcoming Them
Despite its numerous advantages, the 7018 weld rod can be challenging, primarily due to its stringent storage and handling conditions. Maintaining a viable condition requires keeping rods in a moisture-free environment. Invest in a rod oven capable of sustaining consistent temperatures to ensure rods remain ready for use.
Another challenge is the requirement for continued skill development. Welders must train extensively to master the nuances of using 7018 rods effectively, from managing weld pools to adapting techniques across different metals and thicknesses. Continuous education and practice refine one's ability to deploy these rods under various circumstances.
5. Trustworthy Execution and Quality Assurance
Quality assurance in welding with 7018 rods mandates rigorous inspection and non-destructive testing protocols. Methods such as ultrasonic testing or radiography can detect subsurface imperfections, ensuring weld integrity. Adhering to recognized standards, such as those established by the American Welding Society (AWS), enhances credibility and assures stakeholders of the project's safety and durability.
6. Conclusion
Comprehending and mastering the 7018 weld rod can significantly elevate a welder's craft. Beyond technical prowess, the responsibility of ensuring safety, reliability, and integrity of each weld is paramount. Emphasizing expertise through proper application, continuous learning, and dedication to quality not only affirms the welder's authority but also solidifies trustworthiness, positioning them as leaders in their field.