In the complex world of welding, mastering the vertical weld, specifically the [7018 vertical weld], is a hallmark of seasoned professionals. With its distinct challenges and intricate demands, this technique is crucial in various industrial applications, offering both reliability and strength.
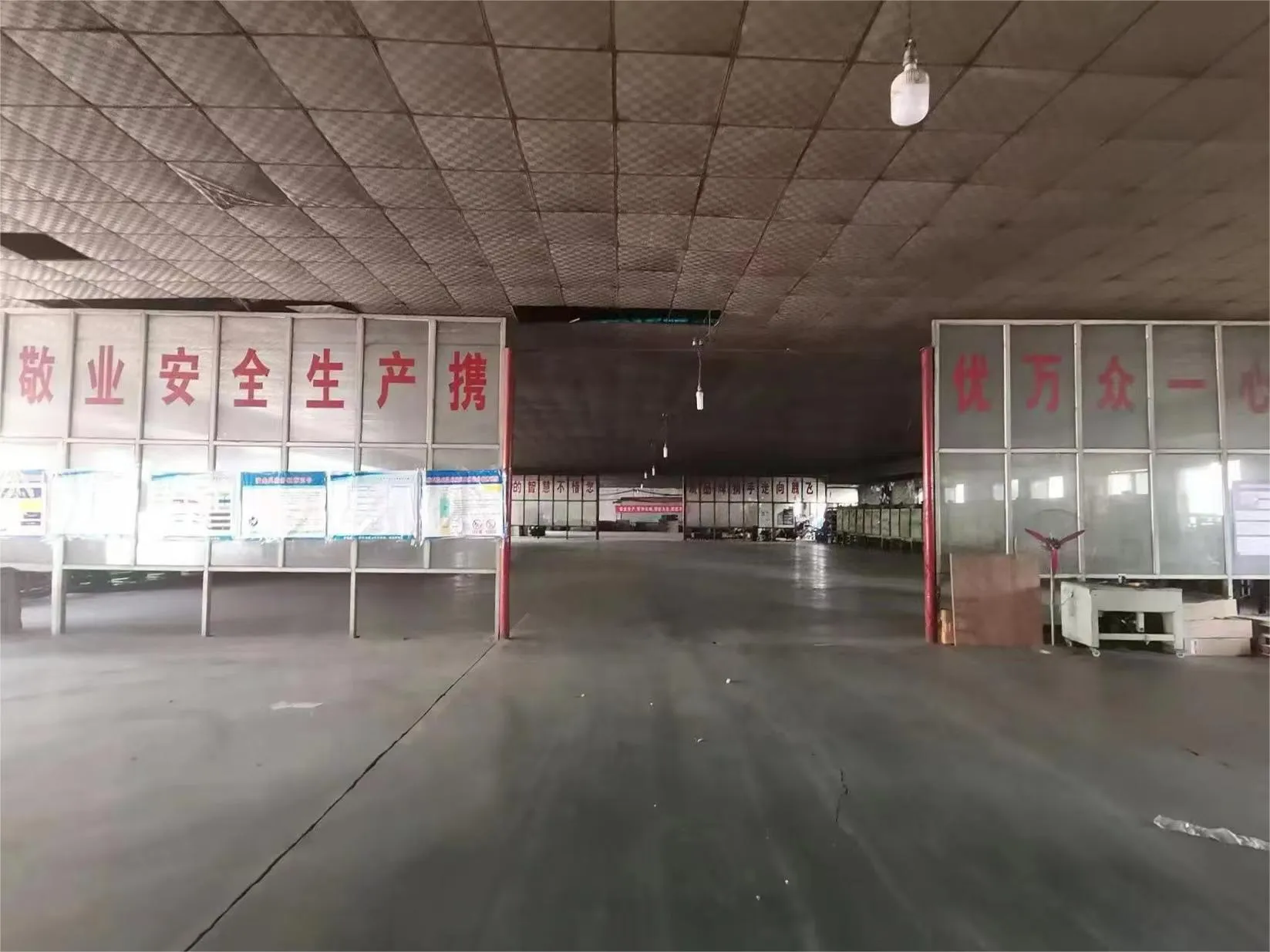
Mastering the 7018 vertical weld requires a comprehensive understanding of both the electrode's properties and the physics involved in the welding process. The 7018 electrode is a low-hydrogen rod that provides excellent deposition qualities, known for producing smooth and consistent weld beads with minimal spatter. This low-hydrogen content also reduces the risk of hydrogen-induced cracking, making it ideal for critical structural applications.
However,
vertical welding poses unique challenges. The gravitational force acts against the molten weld pool, creating a tendency for sagging or dripping if not managed correctly. This requires a skilled hand and a deep understanding of the technique. The welder must maintain a steady hand, adjust the travel angle, and control the heat input, ensuring that the weld pool remains stable and adequately penetrates the base metal.
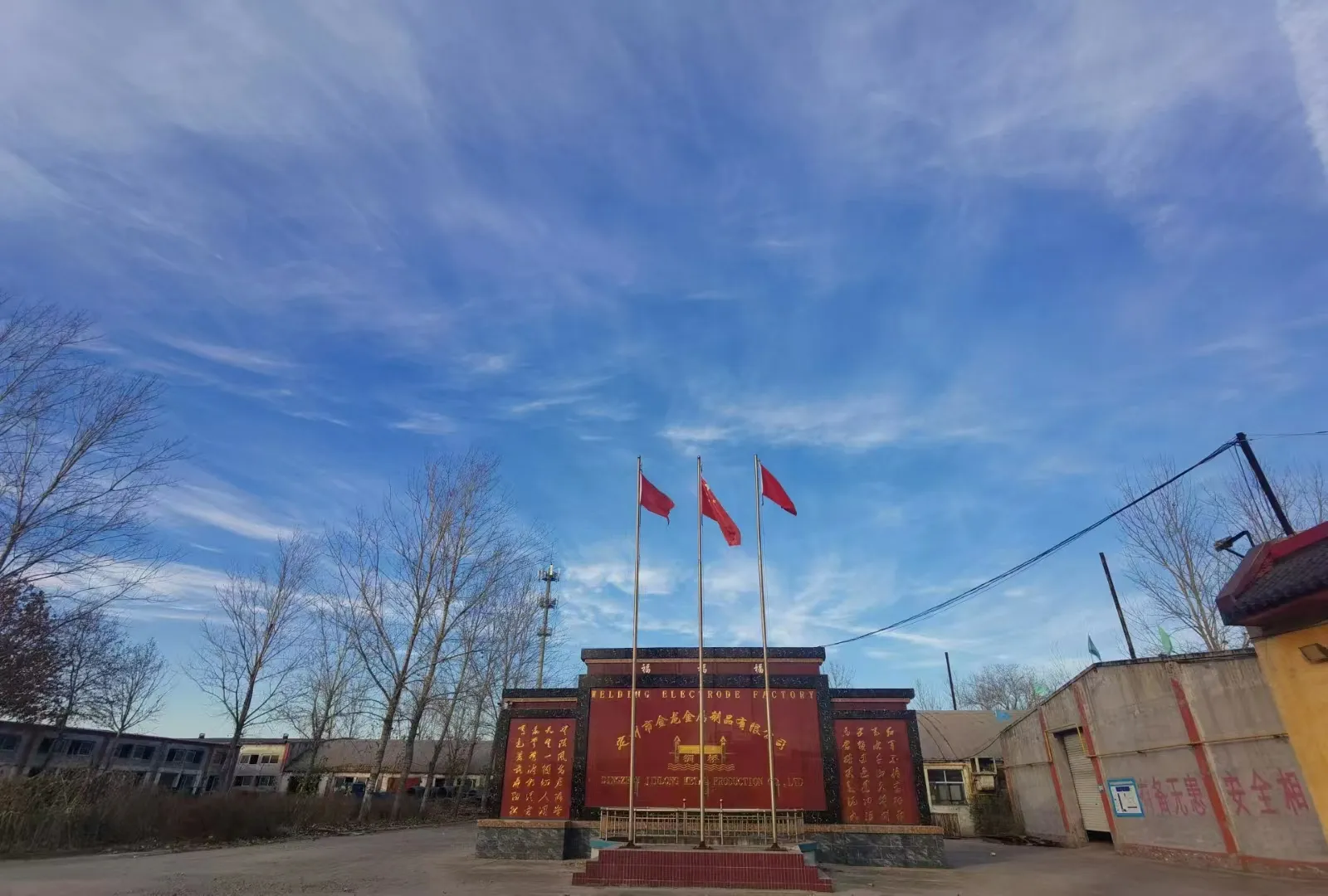
An effective approach to a 7018 vertical weld involves using the T or inverted V technique. This method involves making small, consistent weaving motions with the electrode, allowing the welder to control the shape and penetration of the weld bead. The key is to maintain short arc lengths and ensure that the electrode remains perpendicular to the workpiece. Practicing this technique extensively will ensure precision and reduce welding defects such as undercuts or excessive convexity.
Another critical factor is adjusting the amperage controls on the welding machine. Because the vertical position can cause heat to concentrate differently than in flat or horizontal welding, fine-tuning the current settings is essential to avoid excessive penetration or burn-through in thinner materials. A starting recommendation is to set the amperage slightly lower than you would for a flat weld, and then adjust carefully based on the specific needs of your project and thickness of the metals involved.
7018 vertical weld
Although technical competence is paramount, safety cannot be compromised. Welding in an upright position can expose necessary areas to heat and sparks, so wearing proper safety gear, including flame-resistant clothing, gloves, and a welding helmet, is non-negotiable. Moreover, maintaining good ventilation is critical, especially when using electrodes like 7018, which can produce fumes detrimental to health.
For industries and applications where structural integrity is non-negotiable — such as in construction, shipbuilding, and pipeline welding — the 7018 vertical weld is the preferred choice. Its ability to consistently deliver high-strength welds underlines its importance in creating stable structures that can withstand various stresses and environmental conditions.
Gaining expertise in the 7018 vertical weld not only enhances a welder's repertoire but also cements their authority in the field. Employers and clients alike recognize the value of quality welding, ensuring that projects are delivered with the utmost strength and durability. Furthermore, with continuing advancements in materials and welding technology, staying informed and continually honing one's skills in vertical welding signifies trustworthiness and commitment to superior project delivery.
In conclusion, the 7018 vertical weld is much more than a technical skill; it is a testament to a welder's expertise and dedication to quality. As industries push the boundaries of what's possible, the demand for proficient vertical welders continues to grow. Mastery of this technique will undoubtedly set welders apart, aligning with industry standards and client expectations, thereby ensuring that both present and future projects rest upon a foundation of solid integrity.