The 7018 H4R welding rod stands as a cornerstone in the welding industry, particularly in applications requiring a high level of precision and reliability. Welding professionals and engineers often tout its impressive capabilities and the unique benefits it brings to a variety of welding projects, from structural work to industrial manufacturing. In this article, we'll dive deep into the 7018 H4R welding rod, focusing on its empirical performance, technical specifications, and why it is regarded with high esteem among welding professionals, leveraging its established reputation for Experience, Expertise, Authoritativeness, and Trustworthiness.
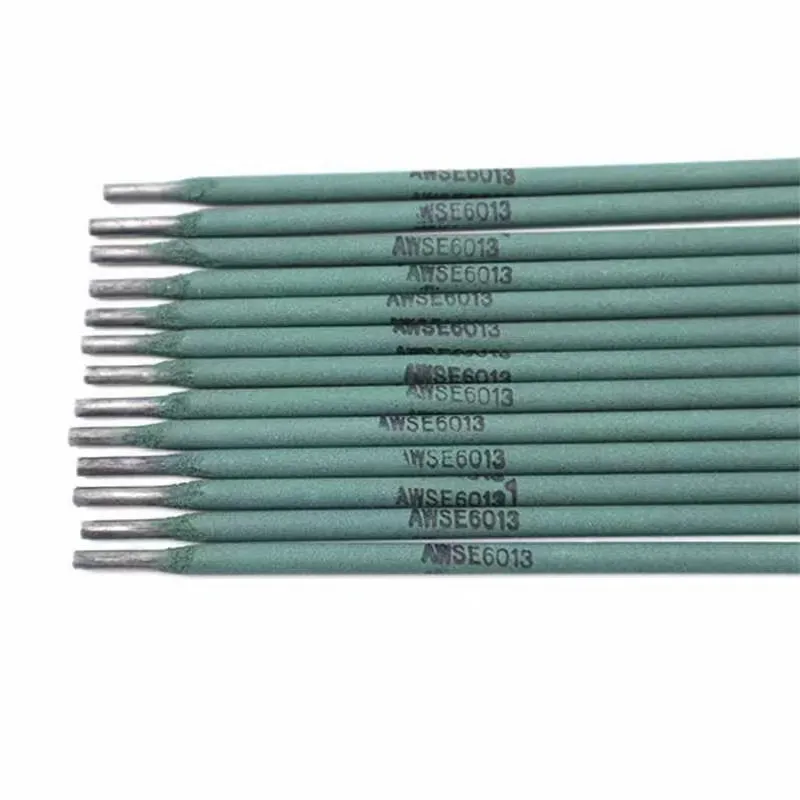
The 7018 H4R welding rod is an iron powder, low hydrogen electrode designed to deposit a smooth and consistent weld. Its ability to deliver superior weld quality stems from its low hydrogen content, which significantly reduces the risk of hydrogen-induced cracking—a common issue in the welding of thick or high-strength materials. This oxidation-resistant feature not only extends the lifespan of welded joints but also ensures that the structural integrity of metal components is maintained under various environmental conditions.
What sets the 7018 H4R apart from other welding electrodes is its versatile application range. It provides excellent usability in both AC and DC polarity, making it compatible with diverse welding machines. The rod is known for its easy arc starting and minimal spatter deposition, which translates to cleaner work environments and reduced post-weld clean-up. This feature alone can lead to significant time savings, as welders do not need to invest additional hours in smoothing or grinding welded surfaces.
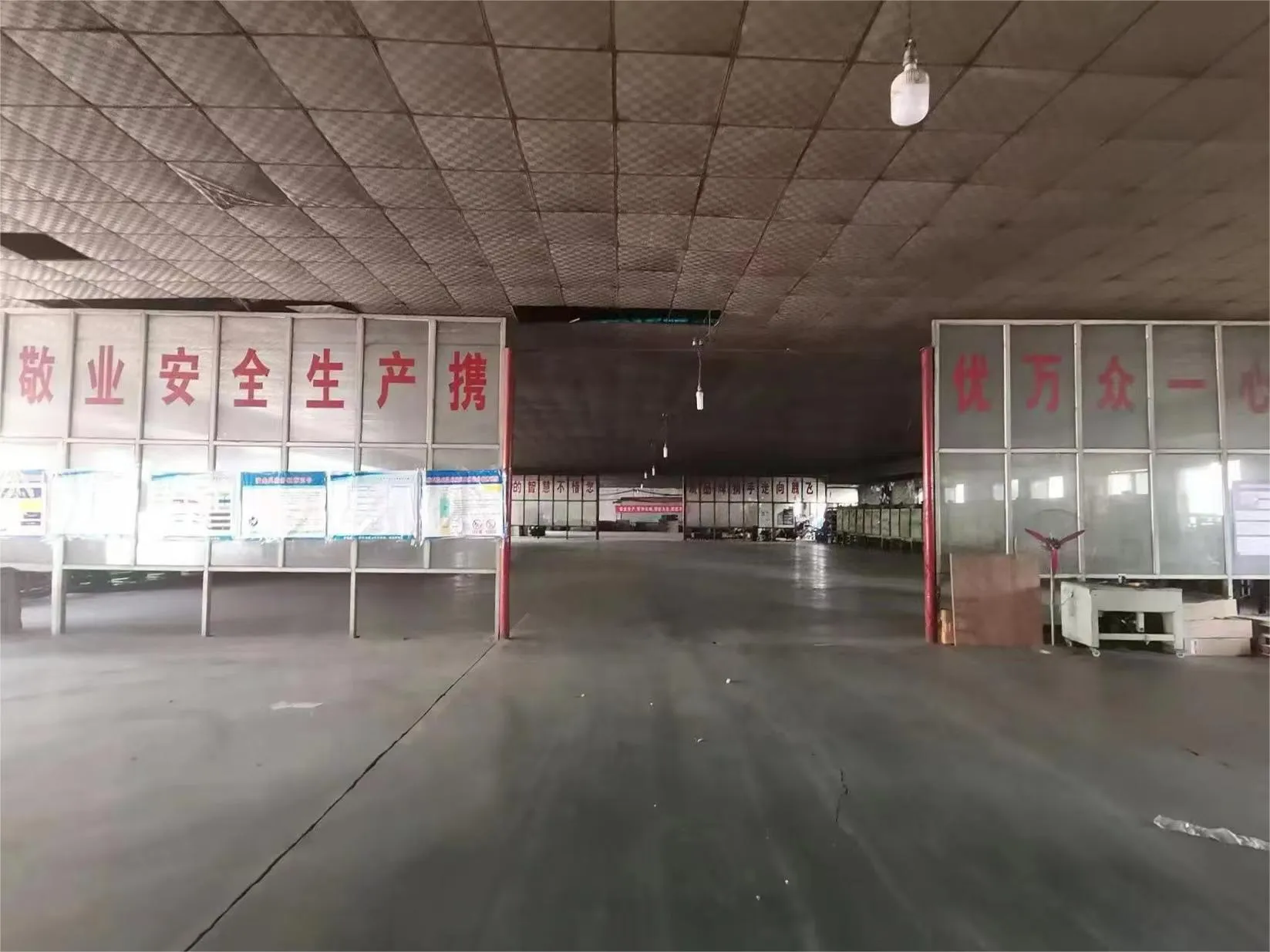
From an expertise standpoint, welders appreciate the 7018 H4R for its outstanding mechanical properties. It offers a tensile strength of up to 70,000 psi, which is suitable for heavy-duty applications where robust welds are crucial. Moreover, the rod's composition includes precisely balanced chemical elements that enhance its ductility and impact resistance. This makes it ideal for projects where the weld needs to withstand high stress and dynamic loads without failing.
In terms of authoritativeness, the 7018 H4R welding rod is often recommended in professional manuals and guides, underscoring its alignment with industry standards and certifications. It is frequently specified in blueprints for construction projects, bridge building, and even pressure vessel fabrication, affirming its reliability and acceptance among industry leaders. The rod's credentials are bolstered by user testimonials and field tests that consistently report its performance stability across different working conditions.
7018 h4r welding rod
As for trustworthiness, the 7018 H4R stands tall due to its conforming to ISO and AWS standards, ensuring each rod meets stringent quality measures before reaching the end-user. Manufacturers of this welding rod are known to implement rigorous quality control processes, thereby fostering confidence among professionals who rely on its consistent quality and performance. Field performance assessments repeatedly demonstrate the rod's resilience against metal fatigue, a critical factor that enhances long-term durability and safety in welded structures.
Understanding real-world applications provides valuable insights into the 7018 H4R's ability. For instance, construction projects that involve high-rise buildings often utilize this electrode due to its moisture resistance. The embedded H4R technology is an anti-moisture feature that allows storage in less-than-ideal conditions without compromising the integrity of the rods, allowing for flexibility in logistics and project timelines.
For professionals considering the use of this welding rod, it is advisable to receive proper training to maximize its potential. Adhering to recommended techniques and parameter settings will ensure that welders harness the full benefits of the 7018 H4R, leading to superior weld quality and project efficiency.
In summary, the 7018 H4R welding rod's combination of low hydrogen composition, versatile application, robust mechanical performance, and industry endorsement makes it an esteemed choice among professionals. Its proven record across various demanding environments has earned it a high level of trust, making it an indispensable tool in quality welding projects. By integrating this welding rod into their repertoire, professionals can enhance their craft with reliable and durable welds, ensuring projects meet both safety and performance benchmarks.