Understanding the 7018 H4R Rod A Comprehensive Guide to Choosing the Right Welding Solution
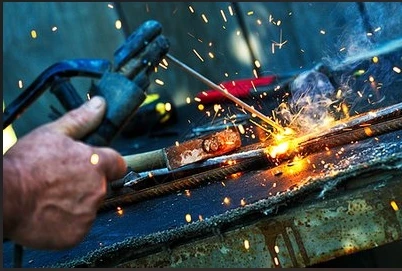
The world of welding is complex and requires a deep understanding of materials, techniques, and tools. One essential component that often comes up in discussions among welding professionals and enthusiasts is the 7018 H4R welding rod. Known for its unique properties and applications, the 7018 H4R rod is a key player in the field of welding. This article provides a comprehensive overview of its features, benefits, and uses, offering insights into why it might be the right choice for your welding projects.
The 7018 H4R rod is renowned for its low-hydrogen iron powder coating, making it a reliable option for crucial weld structures that require high-quality work and resilience. This rod is classified as a 'low-hydrogen' rod, meaning that it minimizes the introduction of hydrogen into the weld puddle. This is crucial in preventing hydrogen-induced cracking, a common issue that can lead to weld failure. Such features come primarily from its 'H4R' designation–signifying its low moisture pickup and exceptional moisture resistance.
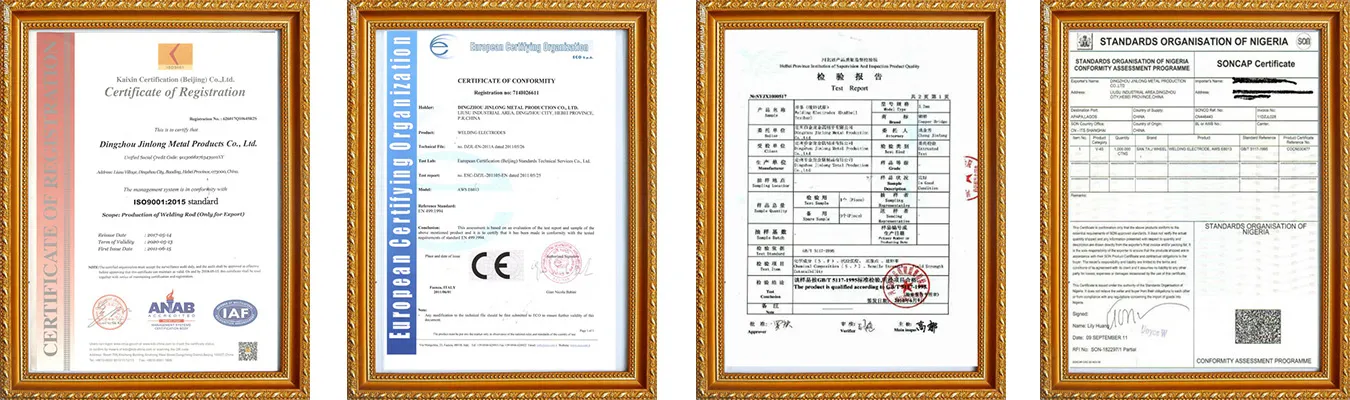
From an expertise standpoint, the 7018 H4R rod requires some skill to handle effectively because it must be kept dry and often requires a consistent heat source to maintain performance. It is typically stored in dry conditions or in a rod oven set between 250°F and 300°F to prevent moisture absorption—critical to maintaining its low-hydrogen properties. Experts in welding often recommend a high level of qualification to wield 7018 H4R rods due to these storage and handling requirements.
The attractiveness of the 7018 H4R rod lies not only in its mechanical properties but also in its wide range of applications across industries. Its usability in welding structural steel, notably for industries such as construction, shipbuilding, and infrastructure development, highlights its vital role. Its weld deposition provides excellent mechanical properties, especially when heated according to manufacturer guidelines. This makes it an authoritative choice for projects demanding superior weld seams, such as those in pressure vessel fabrication or heavy machinery manufacturing.
7018 h4r rod
Real-world experiences underscore the trustworthiness of the 7018 H4R rod. Professional welders often cite its smooth arc performance and easy slag removal as key benefits, making it an efficient tool for producing cosmetically appealing welds with minimal cleanup required. This contributes to increased productivity, positioning it as a cost-effective solution compared to some of its counterparts. Hands-on use in demanding environments confirms its superior toughness and ductility, reassuring welders of its reliability under stress.
It's crucial to note that the 7018 H4R rod also provides satisfactory usability in out-of-position welding—something that welders need when working on complex weld geometries. While flat and horizontal positions yield the best results, experienced welders can achieve successful vertical and overhead welds with the right technique and experience. This versatility makes it a popular choice for varied applications, from bridge construction to repair work in automotive or agricultural fields.
Furthermore, understanding the impact of storage conditions cannot be overstated when working with 7018 H4R rods. Maintaining its dryness is key to preserving its low-hydrogen characteristic—directly influencing the quality of the weld. Employers and welders should ensure proper training and adherence to handling guidelines to maximize the rod's effectiveness in their projects.
Choosing the 7018 H4R rod for your welding projects demands a balance between understanding its detailed requirements and leveraging its benefits. Through proper storage, handling, and application, the rod delivers welds of exceptional quality, proving itself as a trustworthy investment for delivering durable and strong connections in a range of industrial applications. As a staple in welding arsenals, mastering its use offers professionals a competitive edge in consistently achieving high standards in their welds, reinforcing its place as an authoritative choice in the industry.