Selecting the correct amperage for a 7018 welding rod is essential for achieving optimal weld quality and performance. This particular welding rod is known for its versatility and strength, making it a popular choice among welders for a variety of structural applications. Understanding the nuances of amperage settings can significantly impact the outcome of your welding projects. Here’s a closer look into the intricacies of using the 7018 welding rod and how to effectively utilize it to maximize your results.
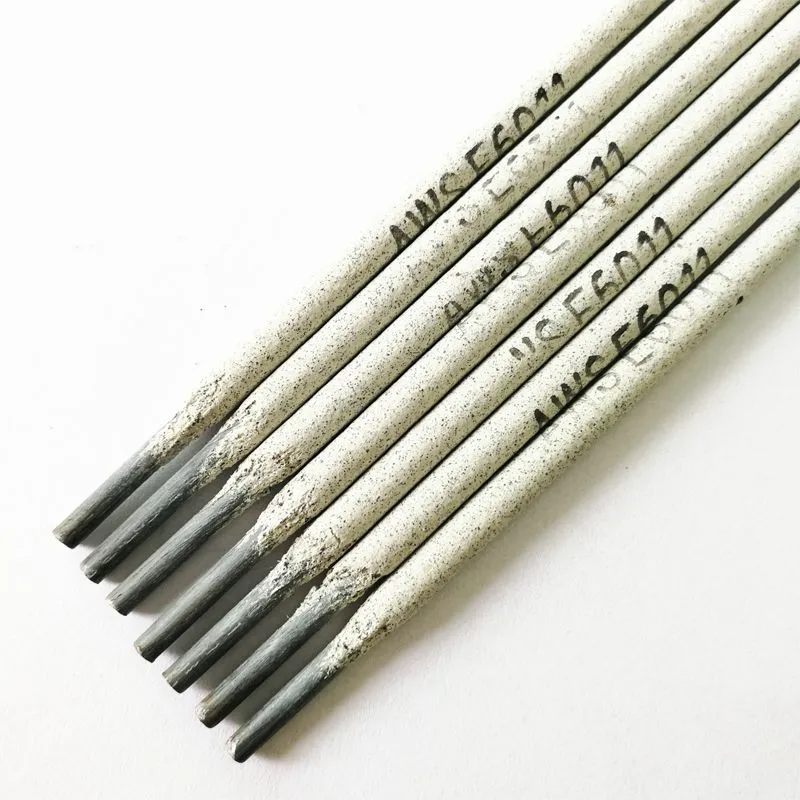
The 7018 welding rod is classified as a low-hydrogen electrode, which means it minimizes the risk of hydrogen-induced cracking—a common issue in high-strength steel welding. Its popularity stems from its capability to produce high-quality welds characterized by excellent mechanical properties and an aesthetically pleasing finish.
When determining the correct amperage for a 7018 rod, several factors come into play, including the diameter of the rod, the type of material being welded, the joint configuration, and the welding position.
For a 5/32 inch 7018 welding rod, the recommended amperage typically ranges between 90 to 170 amps. Finding the sweet spot within this range is critical and can greatly vary based on the specific conditions of your project.
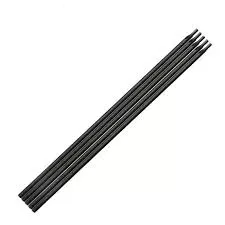
Experience plays a pivotal role in selecting the right amperage. Seasoned welders often rely on their understanding of the subtleties of the welding environment. For instance, welding in a flat or horizontal position might allow for higher amperage, around 140 to 170 amps, which helps maintain a steady arc and effective penetration. Conversely, for vertical or overhead welding, reducing the amperage—closer to the 90 to 130 amps range—can prevent excessive heat buildup, which could lead to molten metal dripping or sagging.
Professional expertise is equally crucial when working with 7018 rods. Professionals appreciate that these rods are designed for AC or DCEP (Direct Current Electrode Positive) currents and are most effective under consistent power supply to maintain their low-hydrogen integrity. A rapid change in amperage can increase hydrogen diffusion, undermining the rod's intended performance.
5 32 welding rod 7018 amperage
The authority of a welder often hinges on their understanding of how different metals react under varied conditions. When welding on thicker materials, for example, bumping up the amperage allows for deeper penetration and a more secure weld. Experts also consider electrode manipulation techniques; for tighter joints, a lower amperage with a weaving motion can be advantageous, whereas higher amperage with stringer beads can be more suitable for wide joints.
Trustworthiness in welding practices is demonstrated through adherence to recommended guidelines and standards. Reliable welders never compromise on the operational manual specifications provided by welding rod manufacturers. Trust is also built through rigorous testing methods. Conducting test welds with increased and decreased amperage settings aids in pinpointing an ideal range, ensuring strong, clean welds without compromising the material's integrity.
Understanding the relationship between amperage and arc stability is vital for those seeking better control over the welding process. A stable arc—achieved by setting the correct amperage—not only facilitates a smoother operation but also enhances the welder’s ability to predict and manipulate the molten pool. Such control is paramount, especially when dealing with complex weldments.
Utilizing a 7018 welding rod with precision can vastly improve both the structural integrity and visual appeal of a weld. By leveraging experience and expertise in determining the appropriate amperage, welding professionals showcase their authoritative knowledge within the field, while trustworthiness is upheld through consistent, high-quality welds. Balanced amperage settings contribute to prolonged electrode life and reduced rework, leading to more efficient project completion and cost-effectiveness. Understanding this fundamental aspect of welding preparation helps ensure that each application of the 7018 means consistently exceptional results.