When it comes to choosing the correct welding rod, understanding the specifics of each type is essential. The 6010 welding rod is a popular choice among welders due to its versatility and capability to produce strong welds in various positions. This rod is particularly known for its outstanding arc stability, deep penetration, and the ability to perform well in vertical and overhead welding.
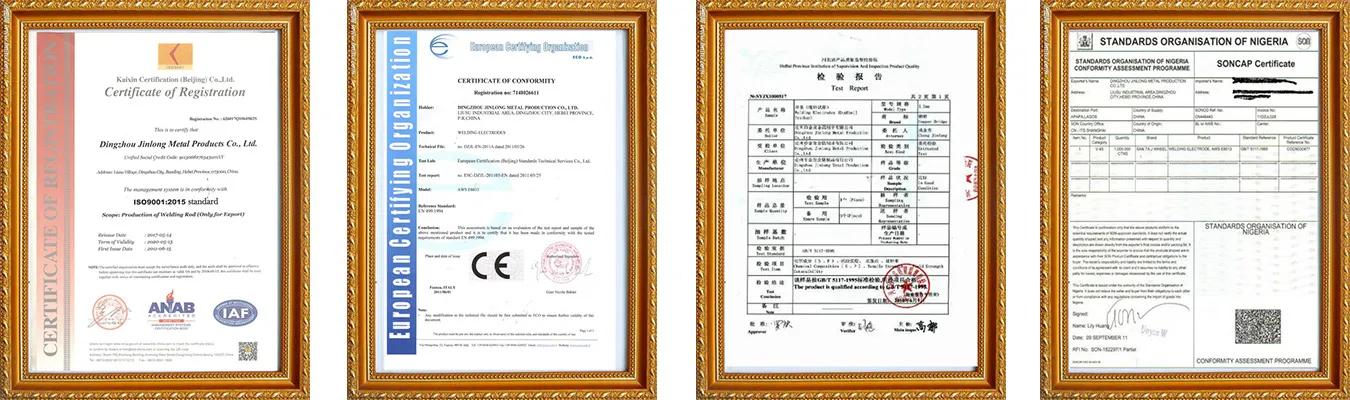
Understanding the 6010 Welding Rod
The 6010 welding rod is a cellulose-based rod ideal for mild steel. The '60' in the 6010 designation stands for the tensile strength, implying that it can withstand a maximum of 60,000 pounds per square inch. The '1' indicates that it can be used in any position, which adds to its versatility. Lastly, the '0' signifies that it is a DC (Direct Current) rod, typically used with a DC power source.
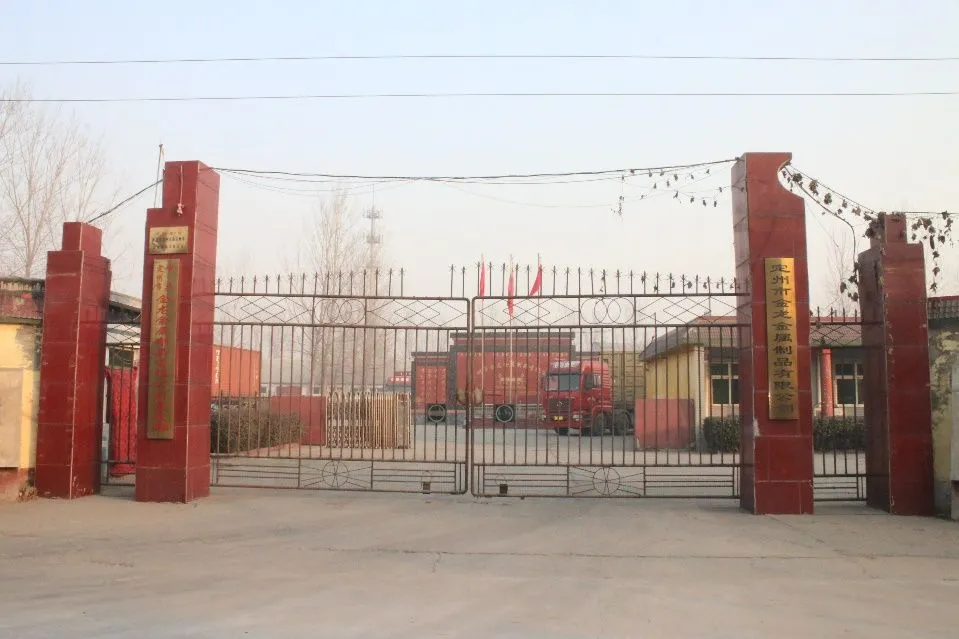
Amperage Settings A Critical Factor
Proper amperage settings are pivotal in achieving optimal performance when using 6010 rods. The amperage settings determine the heat output during the welding process and thus influence the penetration, fluidity, and overall quality of the weld. For a 5/32-inch 6010 welding rod, the typical amperage range is between 160 to 195 amps, although this can be adjusted based on specific welding conditions and individual preferences.
Factors Influencing Amperage Setting
1. Material Thickness Thicker materials generally require higher amperage to ensure adequate penetration and fusion. For materials on the thicker end, consider setting the amperage towards the higher side of the range.
2. Position of Welding When welding in vertical or overhead positions, lower amperage settings can prevent excessive spatter and control the weld pool better.
3. Welder's Experience and Technique Experienced welders might adjust the amperage slightly based on their technique. A steady hand may allow for lower amperage settings because they can control the weld pool effectively.
4. Type of Joint Different joint configurations may require variant amperage to achieve the best structural outcome. For instance, a butt joint might need less heat compared to a T-joint.
5 32 welding rod 6010 amperage
Practical Guidance for Optimal Use
For those less experienced with the 6010 rod, start with the middle of the recommended amperage range and make adjustments as needed. Observing the characteristics of the arc and the behavior of the weld pool can guide necessary changes. A well-formed bead, minimal spatter, and good slag coverage are indicators that the settings are appropriate.
Troubleshooting Common Problems
If you encounter issues such as excessive spatter, difficulty in striking an arc, or porous welds, re-evaluating your amperage settings may be necessary. Excessive spatter often indicates an amperage that is too high, requiring a reduction. Conversely, if the arc is hard to initiate or maintain, slight increases in amperage may be beneficial.
Trust in Professional Advice
As with all welding techniques and tools, consulting with experienced professionals or technical resources can provide guidance tailored to specific applications. This not only ensures optimal performance but also reinforces safety and efficiency.
The Importance of Equipment Maintenance
Regular checks and maintenance of the equipment being used can minimize variability in welding performance. Ensuring that all electrical connections are secure and that the welding machine is calibrated correctly can prevent inconsistencies, making adjustment of an amperage setting more predictable and reliable.
In conclusion, understanding the intricacies of amperage settings for a 5/32-inch 6010 welding rod is crucial for achieving high-quality and consistent welds. A proper balance between the variables discussed can enhance not only the welding process but also the final outcome. Mastery of these elements speaks to a welder's expertise and enhances the trustworthiness of their craft, ultimately leading to superior results in any welding project.