Selecting the correct amperage for a 3/32 inch 7018 welding rod is crucial for achieving optimal results in any welding project. This electrode, known for its versatility and smooth arc performance, is often the choice of professionals who seek consistent quality in their welds. Yet, operating this electrode incorrectly can compromise the integrity and quality of the workpiece.
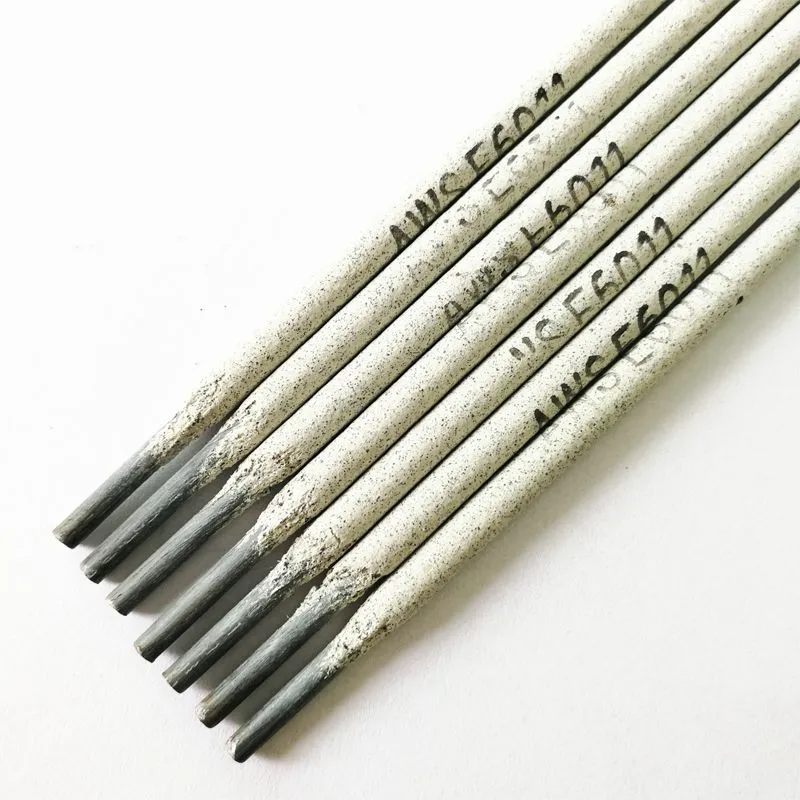
The 7018 welding rod operates optimally within a specific amperage range. Typically, for a 3/32 inch rod, the recommended amperage falls between 70 and 110 amps. Finding the sweet spot within this range, however, can depend on several important factors, including material thickness, welding position, and personal welding technique.
Material thickness plays a vital role in amperage selection. Thicker materials require higher amperage to ensure adequate penetration. For thin materials, using the lower end of the spectrum prevents burn-through and distortion. For example, when working with quarter-inch mild steel, setting the amperage at approximately 90 amps can provide sufficient heat to create strong, secure welds without compromising the parent material.
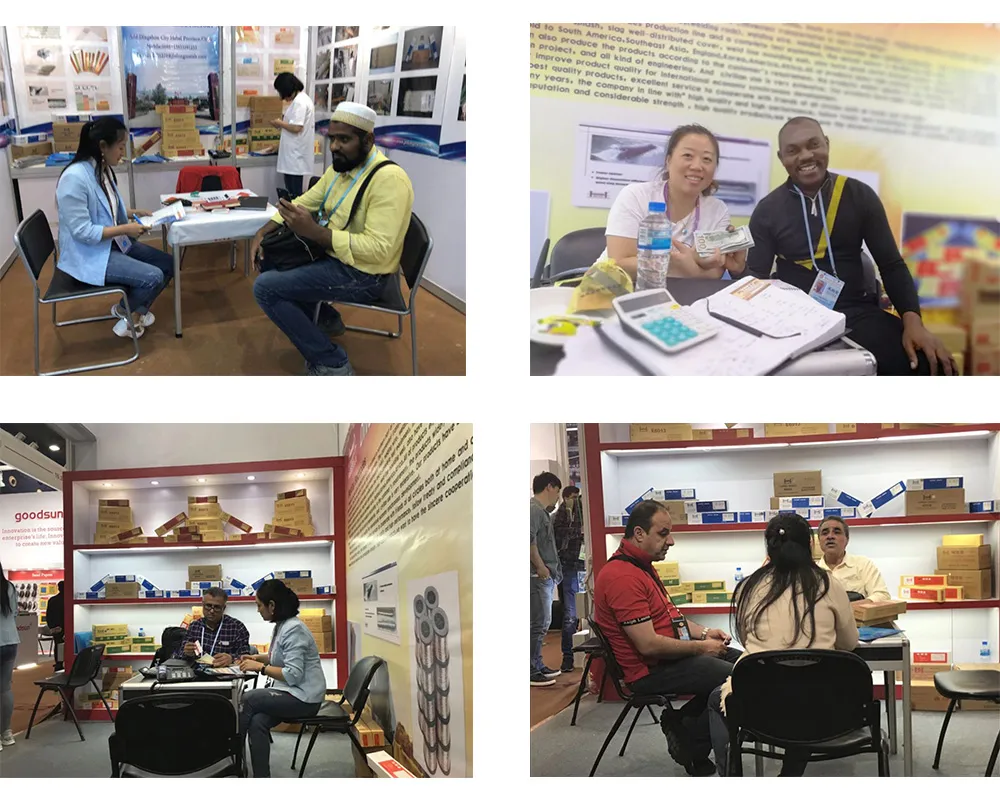
Different welding positions also call for adjustments. Flat position welding generally allows for slightly higher amperage, whereas vertical or overhead positions may necessitate reducing the amperage to maintain better control over the molten pool. For instance, when welding vertically, setting the amperage around 80 amps might help maintain bead stability and prevent excessive dripping.
Personal technique and machine calibration are factors that experienced welders often fine-tune. A seasoned welder may adjust the amperage based on their speed and style to achieve the desired bead appearance and penetration. Familiarity with the welding machine's specific behavior is also important, as machines often vary slightly in performance output.
3/32 welding rod 7018 amperage
An essential consideration is the type of current used alternating current (AC) versus direct current electrode positive (DCEP), also known as reverse polarity. While 7018 rods are designed to operate on DCEP to provide cleaner welds with deeper penetration, adjusting amperage according to the current can further enhance performance. When using different machines or external power sources, ensuring they are set to the correct polarity and amperage can significantly impact the final weld quality.
Many experts recommend performing test welds on scrap materials before commencing with the main project. This allows for practical adjustments to both settings and technique. The feedback obtained during these tests informs the welder on whether the arc characteristics—such as sound, stability, and bead appearance—are in line with the expectations for a structurally sound weld.
Safety cannot be overlooked. Operating at inappropriate amperages not only affects weld quality but can also pose safety hazards like overheating equipment or causing arc blow. Following manufacturer recommendations and adhering to safety protocols ensures both operator safety and welding excellence.
The choice of a 3/32 inch 7018 welding rod is often driven by its ability to produce robust welds with aesthetic appeal. Therefore, understanding and correctly applying the appropriate amperage settings enhances not only the weld's integrity but also reflects a welder's proficiency and commitment to quality craftsmanship. Operating within the sweet spot of the amperage range tailored to specific project needs is a hallmark of professional expertise and authoritative welding practice.
With this understanding and approach, welders enhance their capability to deliver authoritative and trustworthy results, reinforcing both individual expertise and industry standards. Acquiring this knowledge elevates one's skill and ensures the delivery of superior outcomes across diverse welding requirements.