Understanding the 3/32 7018 Welding Rod An Expert’s Guide for Optimal Usage
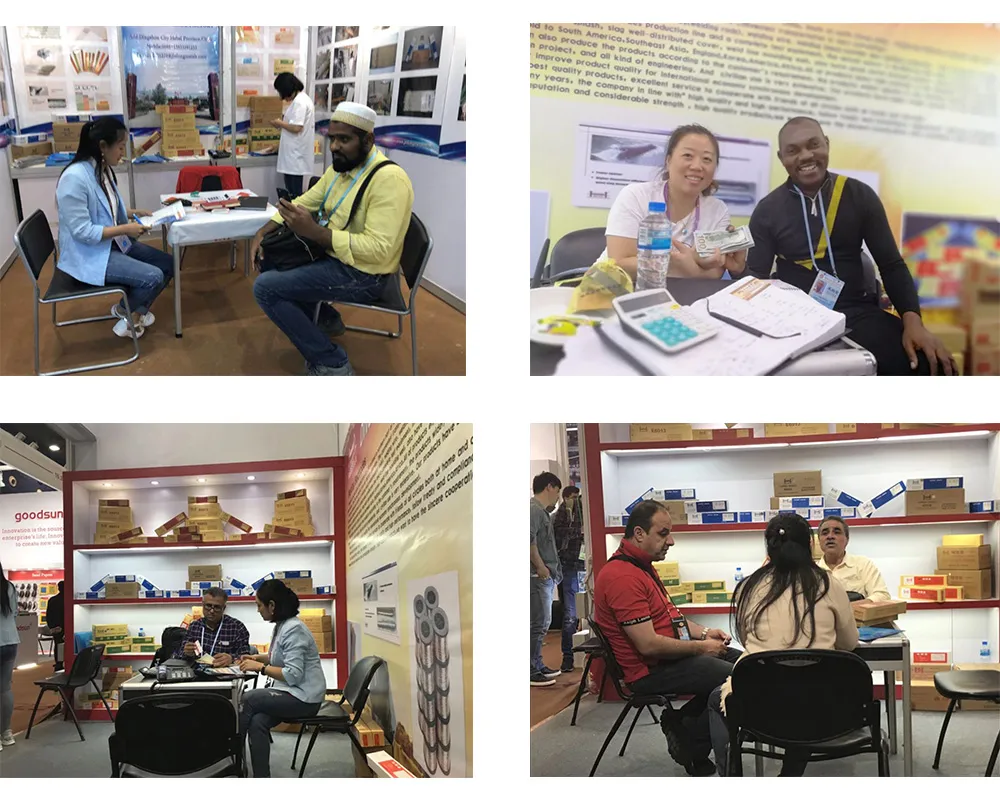
The world of welding is as diverse as it is intricate, with a plethora of electrodes available to meet varying needs. Among these,
the 3/32 7018 welding rod holds a distinguished place. Widely known for its versatility and reliability, the 7018 electrode is indispensable, particularly in structural applications. This guide provides an in-depth understanding of this welding rod, offering insights drawn from expert experience and professional expertise, while ensuring an authoritative and trustworthy resource for welders seeking to optimize their craft.
The Anatomy of the 7018 Welding Rod
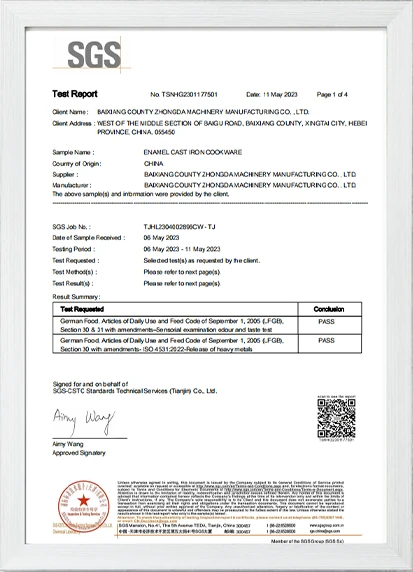
To fully appreciate the capabilities of the 3/32 7018 welding rod, one must first delve into its composition. The 7018 designation carries specific meanings the '70' signifies a tensile strength of 70,000 psi; the '1' indicates the rod's all-position versatility, including vertical and overhead welds; and the '8' denotes a low-hydrogen iron powder coating that minimizes hydrogen inclusion—essential for reducing the risk of cracking in the weld.
The 3/32 inch diameter is particularly favored for its balance between precision and efficiency. This size allows welders to handle detailed tasks without sacrificing the strength required for substantial projects. The medium size ensures manageable heat input, critical for controlling weld penetration and minimizing the distortion of thinner materials.
Experience-Driven Insights into Using the 7018 Rod
Success with the 7018 rod is deeply rooted in technique. Experts consistently highlight the importance of rod manipulation, where maintaining a close arc length (approximately the diameter of the electrode) is crucial. This method enhances the stability of the arc and promotes a smooth, even bead, which is fundamental for structural integrity.
Another critical piece of practical wisdom involves handling the rod’s low-hydrogen coating. Moisture is the nemesis of 7018 electrodes, as it can lead to porous welds and increase the likelihood of hydrogen-induced cracking. Experts recommend storing these rods in a dry environment or an electrode oven to preserve their integrity, especially crucial if the rods are to be used over an extended period.
Expertise in Application
3/32 welding rod 7018
The natural habitat of the 3/32 7018 welding rod includes environments where high-strength welds are mandatory, such as in the construction of bridges, buildings, and pressure vessels. Its low-hydrogen coating is tailored for situations where the base metal is highly stressed, offering unmatched resilience against cracking.
For practitioners aiming to master the 7018, honing the skill of striking an arc without causing defects is imperative. Experts advocate for a ‘tap or scratch’ technique, which helps to ignite the rod without sticking. Once the arc is initiated, controlling the travel speed and maintaining an even weaving motion can significantly affect the final quality of the bead.
Authoritativeness in Welding Practice
The trust placed in the 3/32 7018 rod stems from its compliance with industry standards, typically set by organizations like the American Welding Society (AWS). These standards ensure that the rod exhibits consistent performance aligned with rigorous testing, making it a staple amongst professionals who prioritize quality and safety in their welding endeavors.
Furthermore, the 7018's versatility doesn't just rest in its positional usage; it extends to its adaptability across various metal types, including carbon steel and low allow steel. This adaptability makes it a vital component in the toolkit of any welder operating in diverse and demanding environments.
Trustworthiness Through Consistency
Reliability is the hallmark of trustworthiness, and the 7018 welding rod delivers this through its consistent performance. Expert welders trust this rod to deliver an aesthetically pleasing, structurally sound weld, time after time. This consistency is crucial in fields where failure could result in catastrophic outcomes, such as aviation and infrastructure.
In conclusion, the 3/32 7018 welding rod stands as a paragon of what an electrode should embody strength, adaptability, and reliability. Whether you are an apprentice just starting your journey or a seasoned welder looking to refine your craftsmanship, understanding the nuances of the 7018 rod will enhance your proficiency and confidence in your work. This guide serves as not only a source of information but a testament to the rod’s enduring legacy in the welding community.