Understanding the optimal amperage for the 308 3/32 welding rod is crucial for achieving superior results in stainless steel welding. The 308 3/32 welding rod, known for its versatility, is commonly used for welding similar alloys in wrought or cast forms. The proper control of amperage not only influences the quality of the weld but also extends the lifespan of the components involved.
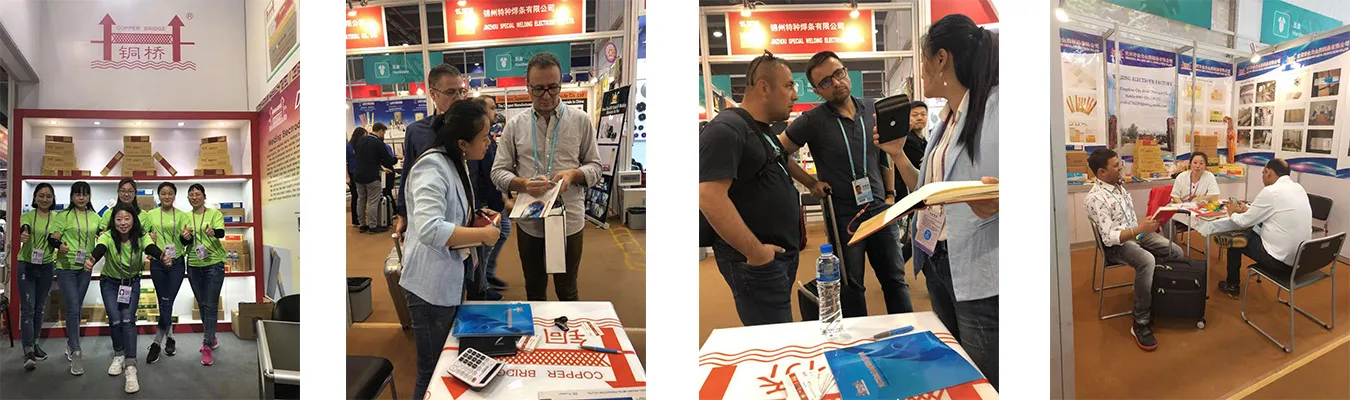
For welders dealing with stainless steel, the 308 3/32 rod is a staple due to its compatibility with a range of applications, including pipe and structural welding. The amperage setting is pivotal, as too low or too high can cause defects, such as porosity or excessive spatter, respectively. Thus, understanding the optimal amperage for this specific electrode is essential.
Amperage settings for the 308 3/32 welding rod generally range between 75 to 105 amps. This range, however, can vary depending on several factors including material thickness, the type of welding process, and the orientation of the workpiece. For instance, welding in vertical or overhead positions may require slightly different settings to maintain control and ensure proper penetration. In these scenarios, it is advisable to opt for the lower end of the amperage spectrum to avoid excessive heat that could lead to burn-through, especially in thinner materials.
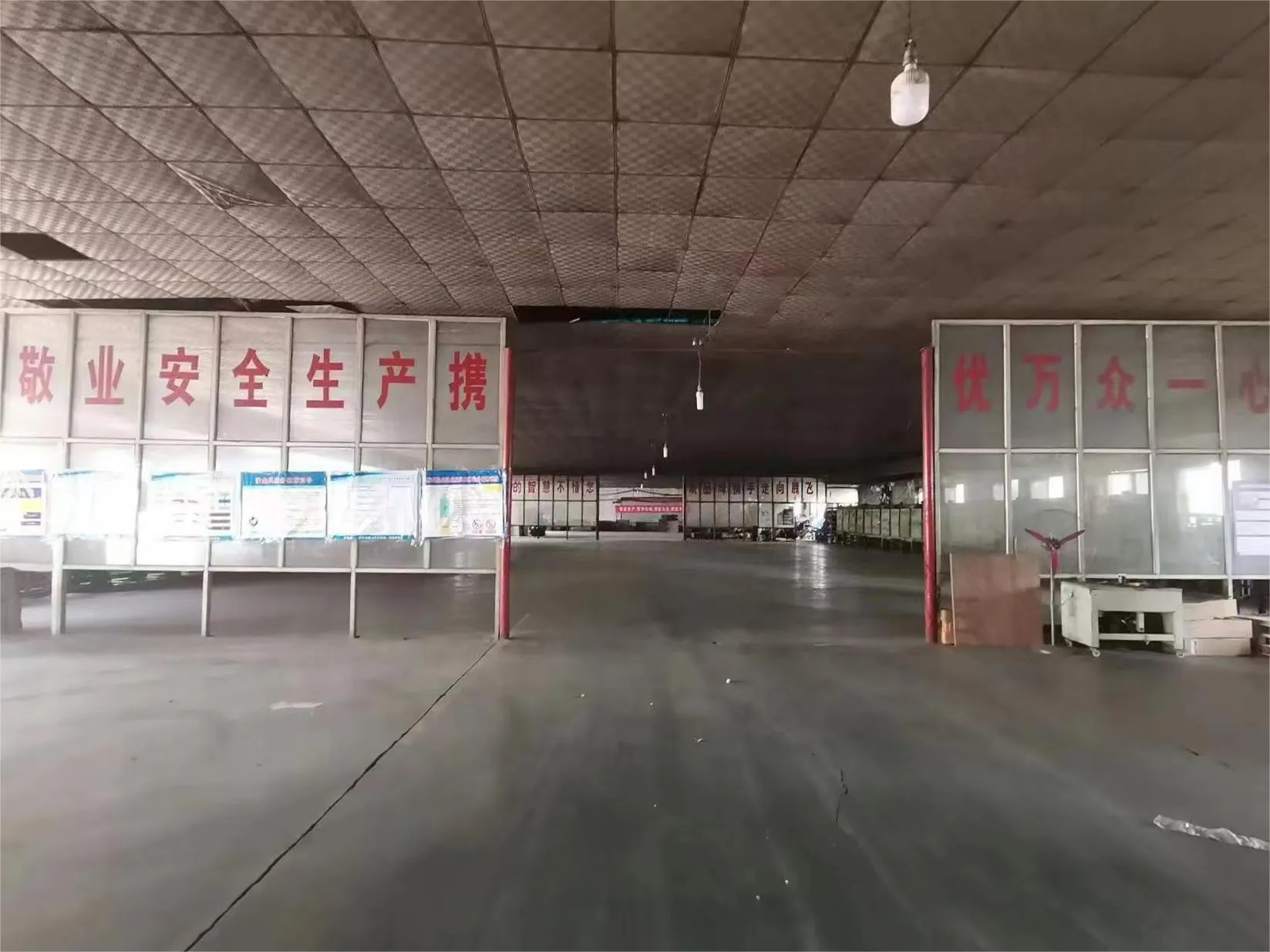
An experienced welder might start with an amperage slightly below the mid-point of the recommended range and adjust as necessary based on the behavior of the arc and the appearance of the weld bead. The sound of the arc, the fluidity of the weld pool, and the responsiveness of the rod as it interacts with the base metal serve as indicators for necessary adjustments. These insights, derived from professional experience, inform the welder when the settings are ideal or when further tweaking is needed.
308 3/32 welding rod amperage
Expert welders often emphasize the importance of pre-weld preparation, stating that clean joints aid in achieving optimal welding conditions. Removing contaminants such as oil, paint, and rust ensures that the welding arc performs consistently and minimizes the risk of defects that are difficult to rectify post-weld. For the 308 3/32 rod, which is typically used in stainless steel applications, it is paramount to maintain a clean and stable arc to create a strong, corrosion-resistant weld.
Additionally, an authoritative voice in the welding industry suggests considering the environmental factors that affect welding, such as wind speed and air movement, as these can influence amperage settings. For instance, when welding outdoors or in high ventilation areas, one might need to slightly increase amperage to combat the cooling effects that the environment might have on the weld pool. Conversely, in controlled environments, sticking closer to the lower end of the range might suffice for optimal results.
Maintaining trustworthiness in welding practices involves adhering closely to the manufacturer’s recommendations for applications and amperage settings specific to the 308 3/32 rod. Documentation provided by reputable manufacturers typically includes guidelines that help ensure the integrity and strength of the welds. Utilizing these resources not only fosters reliable results but also extends the life of both welding equipment and the materials being joined.
In summary, determining the ideal amperage for the 308 3/32 welding rod is a balanced act of technical knowledge and practical experience. Observation and adjustments tailored to the specific conditions and requirements of the welding task ensure high-quality welds. Recognizing the importance of each contributing factor—from equipment and materials to environmental conditions—empowers welders to consistently produce work that meets professional standards of expertise and trustworthiness. The integration of these insights cultivates a well-rounded approach to welding that not only aligns with SEO objectives but also solidifies a brand’s authority in the competitive market of welding products and services.