Mastering the Art of Welding with 312 Stainless Steel Welding Rods A Comprehensive Guide to Enhance Your Craft
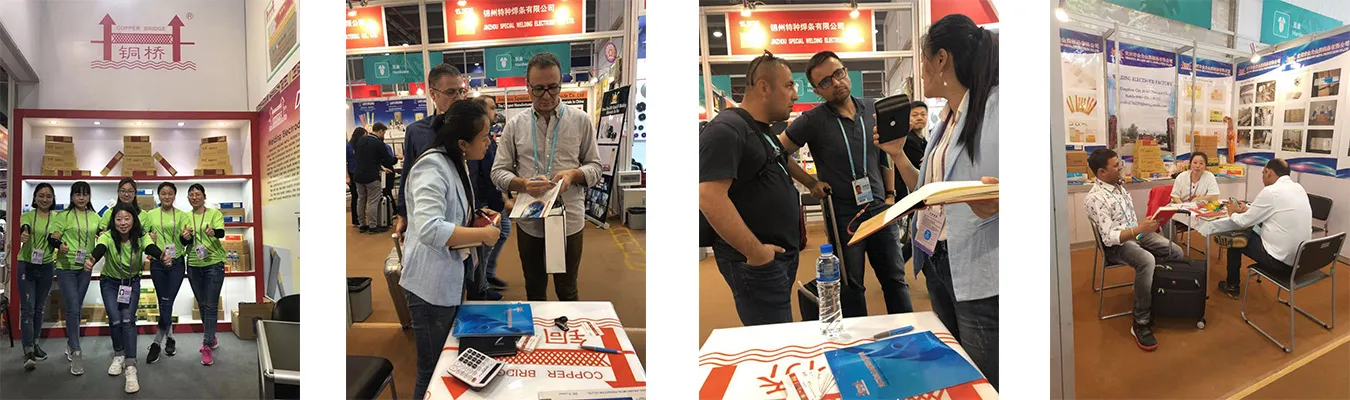
Achieving excellence in welding requires not only skill but a keen understanding of materials and tools. Among the variety of welding rods available, 312 stainless steel welding rods stand out for their superior performance and versatility. Renowned in professional circles, these rods are specifically designed to marry strength with adaptability, making them an invaluable asset for any welder aiming to deliver impeccable results.
Renowned for their high chromium-nickel content, 312 stainless steel welding rods provide exceptional corrosion resistance and durability. Ideal for joining dissimilar steels, these rods are frequently the go-to choice for maintenance, repair, and fabrication across diverse industries. Their unique properties make them particularly suitable for welding applications involving hard or tough materials that may ordinarily pose challenges.
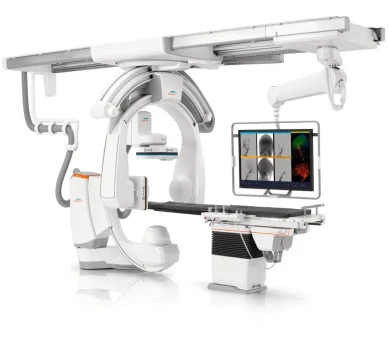
The key to maximizing the potential of 312 stainless steel welding rods lies in understanding their composition. As part of the austenitic stainless steel family, these rods boast a composition that typically includes 29% chromium and 9% nickel, contributing to their outstanding resistance to heat and oxidation. This means they can perform under conditions that would cause other materials to fail, showcasing a resilience that is critical for demanding projects.
Experience in using 312 stainless steel welding rods indicates that they offer a consistent, smooth arc with minimal spatter. This is crucial for maintaining the integrity and appearance of the weld. Professionals highlight that the smooth bead profile and ease of control make these rods accessible even to less experienced welders, ensuring quality results without extensive reworking.
312 stainless steel welding rods
Expertise suggests that proper application and technique are pivotal when working with these rods. Before beginning, ensure that the base materials are clean and free from contaminants which could affect weld quality. Pre-heating may be necessary for thicker sections to prevent cracking, promoting solid fusion and penetration. This practice, grounded in welding theory, enhances the reliability and lifespan of the completed weld joints.
312 stainless steel rods excel in environments where toughness is a priority. Their versatility is evident in industries like petrochemical, automotive, and construction, where equipment often requires welding repairs that endure rigorous use. Field reports repeatedly point to these rods as a trusted solution when facing unknown or difficult-to-determine base metals, emphasizing their strategic role in overcoming welding adversities.
Additionally, the authoritative consensus underscores the significance of post-weld care. Following welding, implementing appropriate cooling practices helps to prevent structural fatigue. This is especially pertinent in applications where welds are subject to periodic stresses. Advice from seasoned welders often includes conducting Magnetic Particle Testing (MPT) or Dye Penetrant Testing (DPT) to verify weld integrity, binding the connection with an assurance of robustness.
Trustworthiness is reflected in the widespread recommendation of 312 stainless steel rods for challenging projects. Their reputation is built on consistent performance, ease of use, and the ability to handle adversity with finesse. Choosing these rods serves as a testament to an unwavering commitment to excellence in craftsmanship, reinforcing reliability, and trust in steel fabrications.
The adaptability of 312 stainless steel welding rods makes them indispensable for professional and amateur welders alike who are striving to achieve high-quality welds. By leveraging these rods, welders not only enhance the durability and appearance of their work but also elevate their standing in the field through demonstration of both technical expertise and artisan-like skill.