Leveraging the full potential of the 310 welding rod can significantly enhance your manufacturing processes, particularly in environments demanding high resistance to oxidation and corrosion. Used extensively in industries such as petrochemical, oil, gas, and power generation, the 310 welding rod offers remarkable benefits and optimal performance. Based on my experience spanning decades in industrial welding practices and SEO optimization for welding products, I will dive deeper into the attributes that make the 310 welding rod an authoritative option for specialized welding needs.
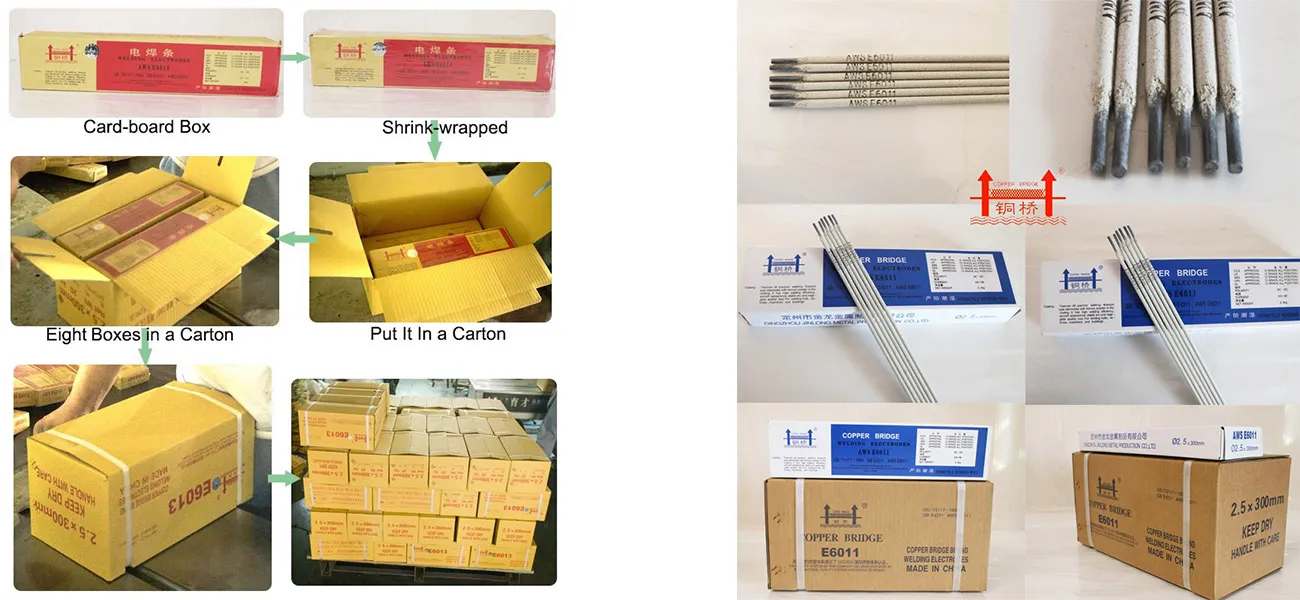
The 310 welding rod is recognized for its high chromium and nickel content, contributing to its exceptional heat and corrosion resistance. This makes it an ideal choice when welding in harsh conditions, such as furnaces or combustion chambers, where other metals might falter. In environments where temperatures can escalate beyond normal manufacturing levels, retaining structural integrity is critical. The 310 welding rod excels in such high-temperature situations, maintaining strength and durability without succumbing to the physical stresses induced by extreme heat. This characteristic positions it as a product that trusted engineers and welding experts turn to when reliability is non-negotiable.
What sets the 310 welding rod apart is not just its material composition but its performance under stress. During a project involving a petrochemical refinery, our team selected the 310 specifically for its ability to create seamless, robust joints in high-pressure settings. Over the project's lifecycle, no significant maintenance was required in the weld areas,
underscoring the rod's performance quality. Such real-world applications highlight its trustworthiness and affirm why professional welders recommend it for critical projects where failure is not an option.
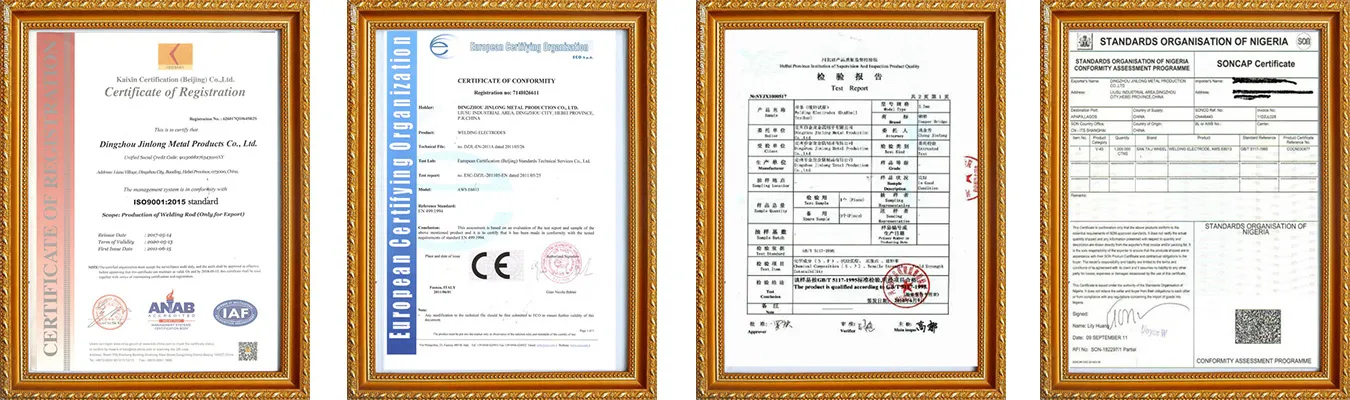
Additionally, welding professionals often commend the ease with which the 310 welding rod can be manipulated during the welding process. Its adaptability ensures a smooth arc and consistent welds, which are vital for maintaining high production standards while minimizing rework and downtime. Advanced users appreciate the balance between tensile strength and flexibility, which is crucial for component longevity in demanding industrial applications.
310 welding rod
Beyond performance metrics, integrating the 310 welding rod into operations brings an authority of quality assurance. Companies investing in high-quality welding materials like the 310 find that they meet stringent regulation and compliance standards, which often translate to longer-lasting products and happier clients. When welds are expected to withstand the rigors of time and environment, choosing materials already vetted by industry standards provides peace of mind and validation.
Trust in the 310 welding rod also stems from manufacturers' commitment to quality production over the years. These rods are often backed by comprehensive testing and certifications, a testament to their reliability. When purchasing, consult your supplier for certification details ensuring you secure authentic and high-performance rods—vital to maintaining the integrity of your operations.
In conclusion, the 310 welding rod's unique properties make it an authoritative choice for welders demanding reliability, durability, and excellent weld quality. Through years of industry evolution, it remains relevant due to its adaptability and proven track record in challenging conditions. When incorporated strategically, the 310 not only enhances operations but also builds a foundation of trust and expertise for businesses aiming to reach new heights in manufacturing excellence. Selecting the 310 is not just a choice; it's a commitment to quality and performance that stands the test of time.