Welding cast iron with a stick welder is a skill that combines both art and science, and it’s a process that has intrigued metallurgists and welders alike. Anyone with experience in this niche knows that cast iron presents a unique set of challenges due to its high carbon content and brittle nature. Here's a comprehensive guide that draws on professional expertise and real-world experience.
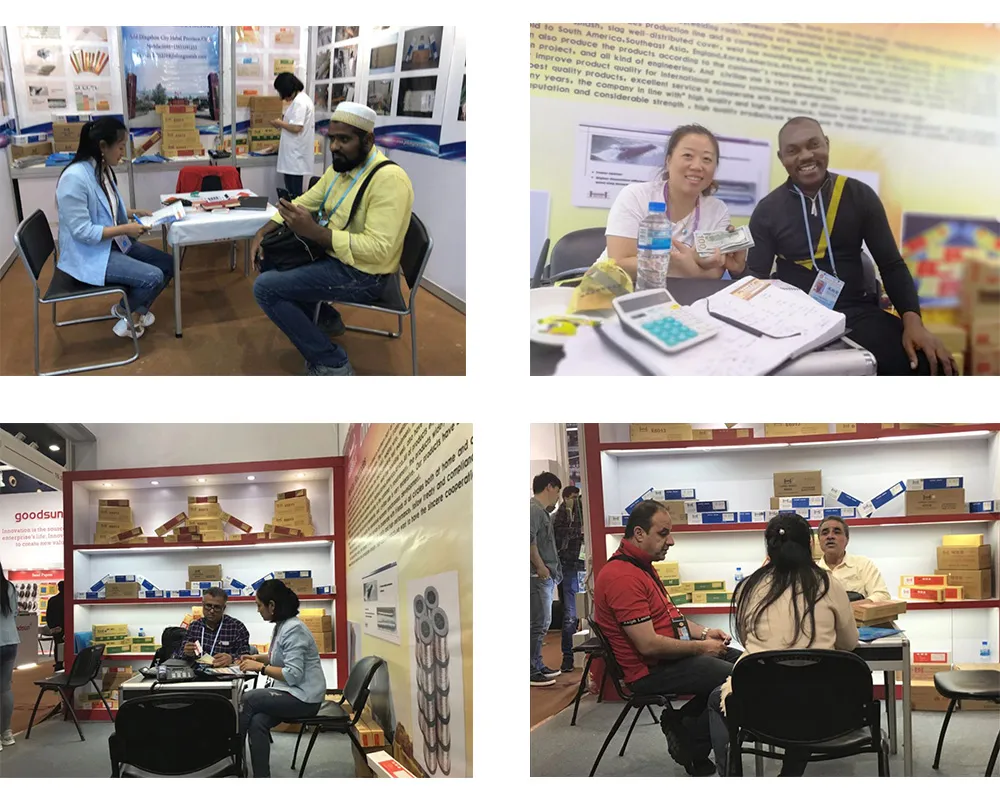
The critical first step in any cast iron welding project is understanding the material's properties. Cast iron typically contains 2% to 4% carbon, which necessitates careful control of heat input and cooling rates. Too rapid a cooling process can lead to cracking, a common frustration for those new to the material. Before you even strike an arc, consider preheating the cast iron to approximately 500°F. This step is crucial because it helps in reducing thermal shock and maintains structural integrity.
Selecting the appropriate stick electrode is crucial for a successful weld. Nickel-based electrodes, such as AWS ENiFe-CI or ENi-CI, are renowned for their compatibility with cast iron. These electrodes offer excellent weldability and reduce the risk of cracking, thanks to their ductile properties. For those working within budgetary constraints, certain steel electrodes can work, but they carry a higher risk and require even more precise heat control.
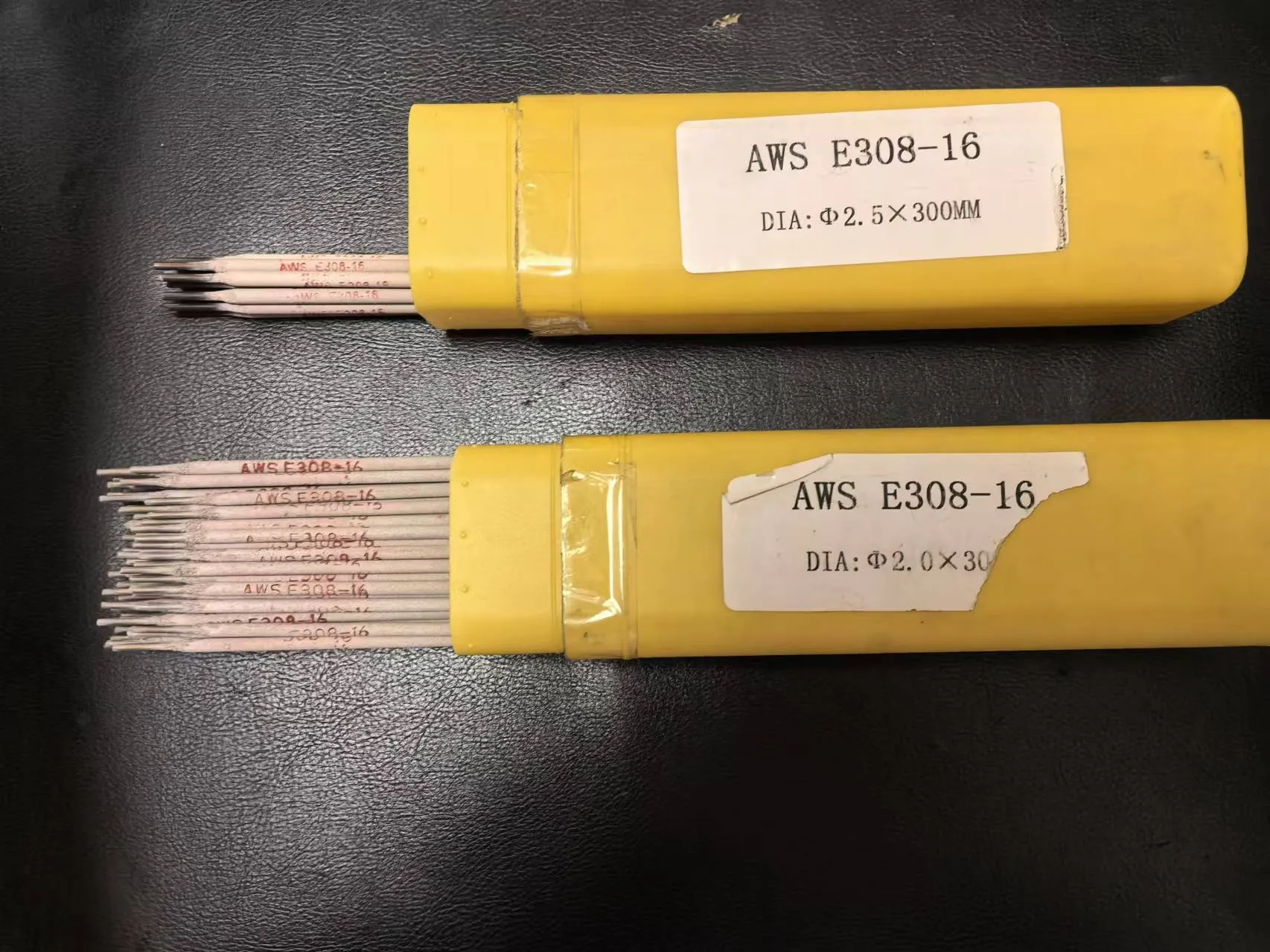
The actual welding method for cast iron with a stick welder should follow a strict regime. Employ a short arc length to prevent porosity and use a low amperage setting to control input heat. It's advisable to make short, staggered welds — no longer than one inch at a time. This helps in minimizing the heat concentration and distributes it more evenly across the weld and parent metal. Each weld must be peened immediately using a ball-peen hammer to relieve stress and counteract cracking.
Cooling the cast iron correctly is as crucial as the welding itself. After the weld is complete, allow the piece to cool slowly. You can achieve this by wrapping it in an insulating blanket or by burying it in dry sand. This gradual cooling process is essential to avoid thermal stress, which is a primary catalyst for cracks.
welding cast iron with stick
Drawing from extensive professional experience, safety cannot be overstated. Given the high temperatures involved and the potential for sudden material fractures, personal protective equipment (PPE) should include welding gloves, a face shield, and appropriate long-sleeved clothing. Additionally, ensure the workspace is well-ventilated to prevent the accumulation of toxic fumes.
Trustworthiness in this craft comes from continuous learning and adaptation. Industry experts regularly emphasize the importance of practicing on scrap pieces before tackling a primary project. This practice brings familiarity with the nuances of cast iron’s behavior under heat and improves skill over time.
Authoritative sources agree that a successful weld on cast iron is a combination of artful technique and strict adherence to safety and procedural standards. Educational seminars, welding forums, and industry workshops can offer further insights and updates on evolving welding technologies and techniques.
In summary, welding cast iron with a stick welder is a specialized skill demanding a balanced application of technical knowledge and hands-on experience. By understanding the metal's properties, selecting the right consumables, executing proper welding techniques, and adhering to safety protocols, one can achieve durable, high-quality welds. This mastery not only adds to one's craftsmanship but also elevates the trust potential clients place in a professional's ability to deliver resilient and reliable metalwork.