Stick welding, also known as Shielded Metal Arc Welding (SMAW), remains a popular choice for metalworkers due to its versatility, portability, and cost-effectiveness. The 7018 electrode is one of the most commonly used sticks in the field, known for its strong welds and ease of use. Mastering stick welding techniques with the 7018 electrode can benefit both novice and experienced welders, providing superior welding craftsmanship.
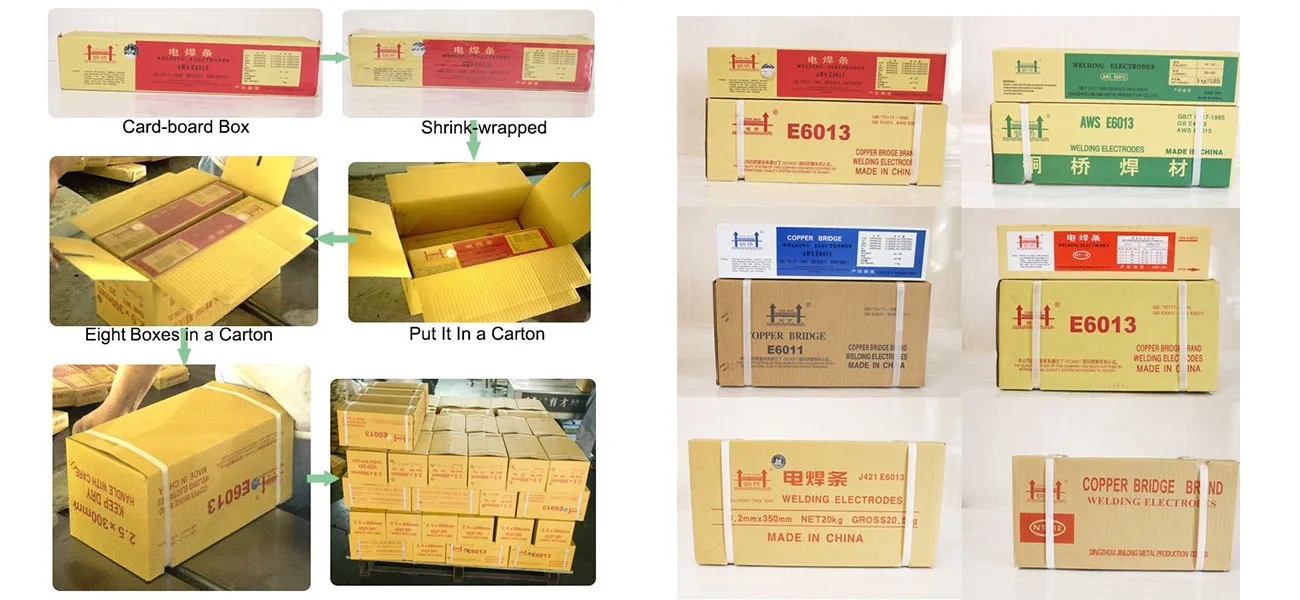
The 7018 electrode is a low hydrogen, iron powder coated electrode, which gives it excellent mechanical properties and crack-resistant welds. Its coating helps protect the weld from atmospheric contamination, making it ideal for a variety of structural applications, from bridges to skyscrapers. However, mastering the use of 7018 electrodes requires understanding its specific requirements and adjusting your technique accordingly.
One of the critical elements in stick welding with 7018 electrodes is maintaining the correct arc length. The arc length is typically about one electrode diameter. A short arc is crucial to prevent slag inclusions and to ensure a sound weld. By keeping the arc length consistent, the welder minimizes spatter and enhances penetration, resulting in a clean and robust weld.
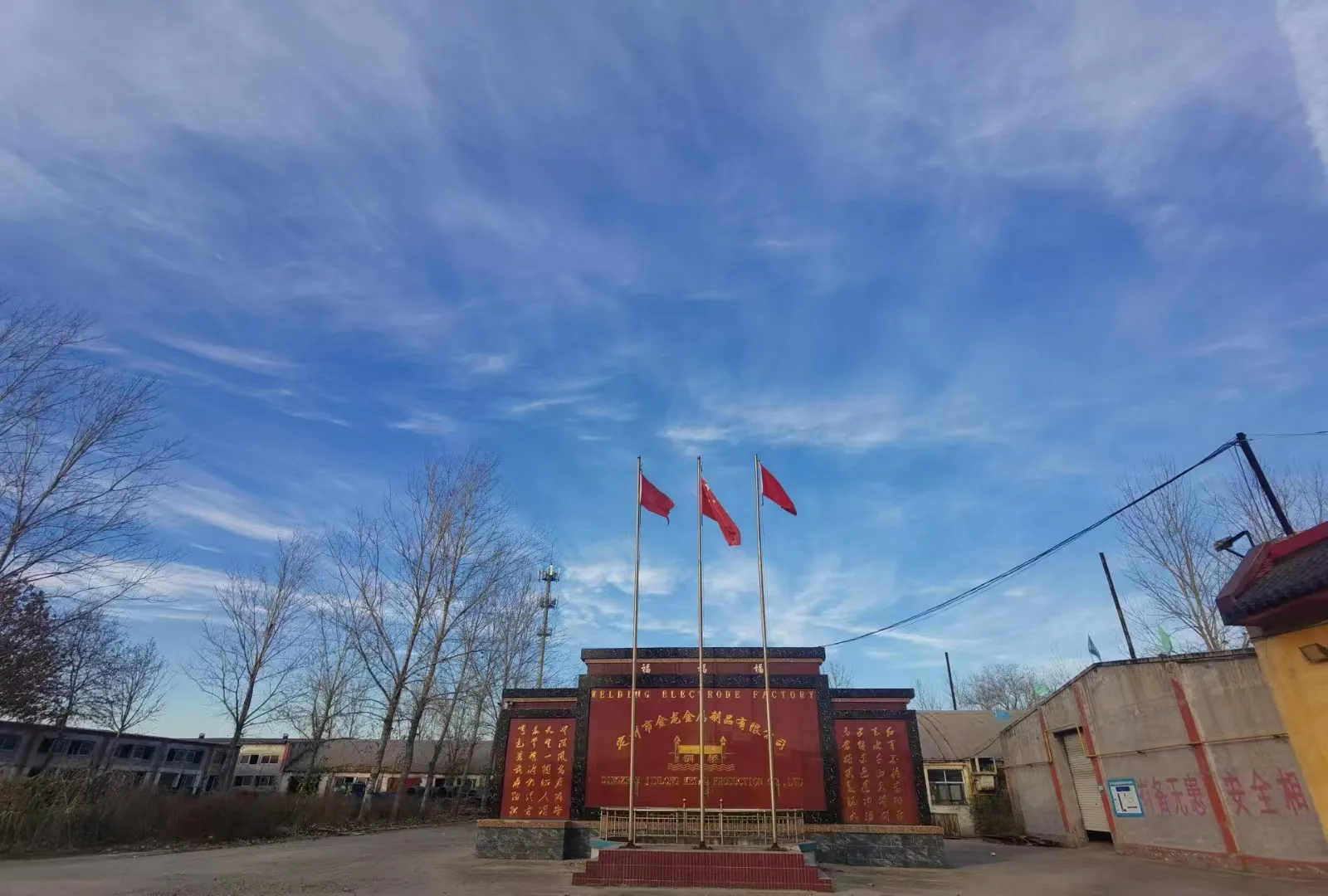
The correct angle of the electrode is another factor that affects the quality of the weld. It is generally recommended to maintain a travel angle between 5 to 15 degrees, leading the weld pool. This angle allows for optimal deposition rate and ensures the slag peels away cleanly as the weld cools. Mastering this angle will significantly reduce the need for post-weld cleaning.
Welding speed is directly linked to the quality and strength of the weld. Moving too quickly can lead to inadequate penetration or a weak weld bead, while moving too slowly may result in excessive build-up or burn-through. The key is to achieve a steady, consistent pace that allows the electrode to penetrate effectively while maintaining a smooth, even bead.
stick welding techniques 7018
Pre-weld preparation is another component that cannot be overlooked. For best results, surfaces must be clean and free from contaminants, such as moisture, rust, or oil. Impurities on the base metal can lead to porosity and weaken the weld. Furthermore, because 7018 is a low hydrogen electrode, it is often stored in a rod oven to prevent moisture absorption. Using electrodes directly from the oven can significantly enhance weld quality and prevent hydrogen-induced cracking.
The striking or starting technique is also pivotal when working with 7018 electrodes. Striking an arc with a 7018 stick requires a swift but controlled motion to prevent the electrode from sticking to the metal, which can disrupt the welding flow and compromise quality. Once the arc is established, maintaining a steady pace and angle is crucial for consistency and uniformity in the weld bead.
Experienced welders often rely on their auditory senses as much as their visual cues. The sound of the arc can provide immediate feedback on the quality of the weld. A consistent, crisp crackling sound indicates a good weld. In contrast, a hissing or popping noise could signal an issue with the arc length or electrode angle and require adjustment.
Safety is of paramount importance when engaging in any welding process. Ensuring the correct protective gear—such as a welding helmet with an appropriate shade, gloves, and protective clothing—safeguards the welder from UV exposure, hot metal, and noxious fumes. Proper ventilation is essential, as the fumes from stick welding can be hazardous if inhaled over prolonged periods.
Regular practice and keen attention to these elements can significantly refine one's stick welding skills with the 7018 electrode, fostering not only efficiency but also safety and quality in metal fabrication projects. By cultivating this expertise, welders can ensure strong, durable joints and deliver high standards of workmanship in any setting, reinforcing their professional reputation and reliability.