Choosing the correct stainless steel filler rod for TIG welding is a critical component in ensuring the success and longevity of a welded joint. The precision TIG welding demands can only be met with an appropriate filler rod that matches the specific needs of the task. As an expert in the field, I have accumulated in-depth knowledge on how to choose the ideal stainless steel filler rod for TIG welding, which impacts both productivity and the quality of the welds.
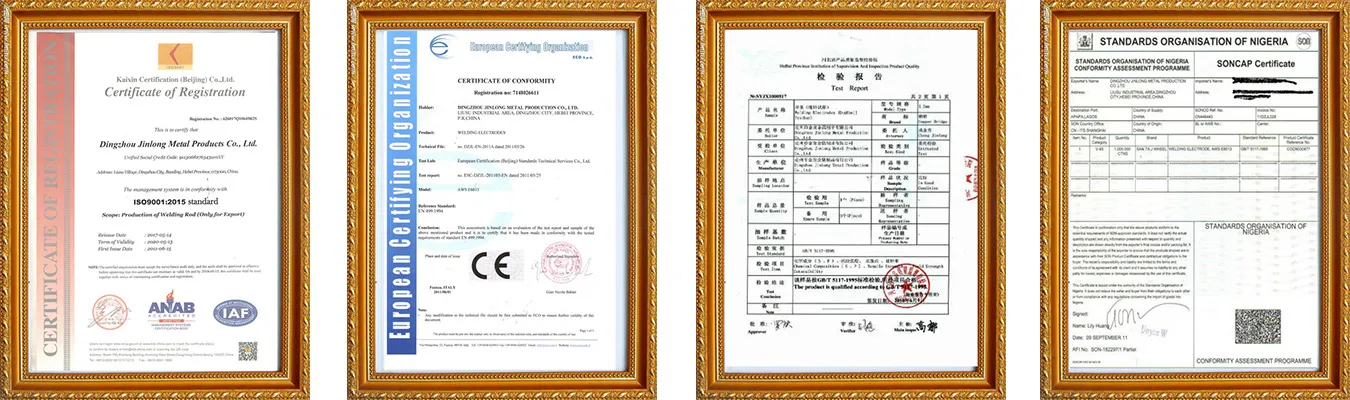
Stainless steel filler rods are available in a variety of compositions, each designed for specific purposes and types of stainless steel. For instance, the common grades such as ER308L, ER309L, and ER316L are widely used, each offering unique properties. ER308L is typically used for welding 304 stainless steel, providing a low carbon content that minimizes carbide precipitation, thus reducing the risk of intergranular corrosion. ER309L works excellently for dissimilar metal welding, especially when joining stainless steel to mild steel, offering increased resistance to cracking. ER316L is suited for molybdenum-bearing austenitic steels, providing enhanced corrosion resistance in chloride environments, making it ideal for applications in marine and chemical industries.
From my experience overseeing numerous welding projects, the choice of stainless steel filler rod must also consider factors like the operating environment of the weldment. For example, in corrosive environments, selecting a filler with higher alloying elements such as nickel and molybdenum is crucial. These elements contribute significantly to the stainless steel’s ability to withstand aggressive mediums, thereby ensuring the weld’s durability and performance.

Moreover, the welding process's thermal cycle influences filler rod selection. TIG welding, known for its precision and control, involves lower heat input compared to other processes, resulting in slower cooling rates. This aspect is crucial for preserving the filler rod's mechanical properties, and a filler with a compatible thermal expansion coefficient with the base metal significantly reduces the risk of thermal fatigue.
stainless steel filler rod for tig welding
The mechanical properties of the desired weld also dictate the filler choice. For structural applications demanding high tensile strength or ductility, fillers that offer a balanced combination of these properties are essential. Post-weld heat treatment needs should be factored into the selection process as specific stainless steel fillers are formulated to respond advantageously to these treatments.
A critical aspect of filler rod selection, often underestimated, is the match between the rod and the welding equipment. The rod's diameter should align with the TIG machine's capabilities, torch size, and the skill level of the welder. Skilled welders can leverage thin filler rods to achieve finer weld pools and accurate heat control, essential in delivering quality welds in thin-gauge materials.
Living in a digital age where information is at our fingertips, ensuring the authenticity and credibility of the resource providing this knowledge is pivotal. Hence, choosing filler rods from reputable manufacturers, who offer traceability and compliance with international standards, becomes imperative. The assurance of consistent quality and adherence to stringent specifications instills trust and reliability in welding outcomes.
In conclusion, the choice of the stainless steel filler rod for TIG welding is influenced by numerous factors such as the type of stainless steel, the operational environment, mechanical requirements, and compatibility with welding equipment. Attention to these details not only enhances the quality and durability of the weld but also optimizes the welding process, leading to cost efficiencies and superior performance. Accessing expert advice and using high-standard materials solidifies not just the integrity of the weld, but also the trust clients place in welding specialists.