Stainless steel is renowned for its corrosion resistance, strength, and aesthetic appeal, making it a staple in various industries, from construction to automotive. Among the numerous grades of stainless steel, SS 304 stands out due to its excellent characteristics. However, welding SS 304 requires specific electrodes to maintain its integrity and functionality.

When choosing a welding electrode for SS 304, one must consider factors such as compatibility, efficiency, and the specific application. An electrode, in essence, is a crucial component in the welding process, acting as the filler material that facilitates effective joint formation. The ideal electrode for welding SS 304 is austenitic, matching the base metal's crystalline structure, thereby ensuring seamless integration.
Shielded Metal Arc Welding (SMAW), commonly known as stick welding, is the preferred method for working with SS 304 in many industrial contexts. The E308L electrode is highly recommended for this purpose. This electrode is specially designed to maintain low carbon content, significantly reducing the risk of carbide precipitation. Carbide precipitation can lead to intergranular corrosion, undermining the longevity and strength of the weld. The E308L electrode's compatibility with SS 304 ensures a superior weld, providing both durability and corrosion resistance.
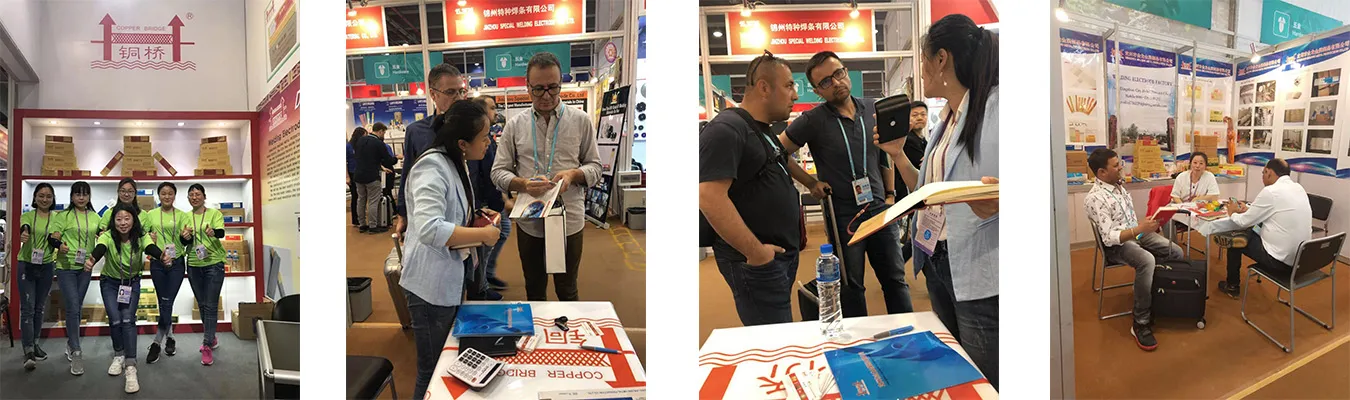
Expertise is crucial when selecting welding electrodes, as the wrong choice can compromise the overall quality. Professionals understand that an electrode's diameter is a critical factor. Larger diameters may support higher currents, allowing for faster welding speeds, but they can also increase the risk of warping or heat distortion, especially on thinner materials. Therefore, determining the appropriate electrode size is vital to ensure efficient heat management and minimize distortion.
Authoritativeness comes into play by adhering to industry standards and manufacturer recommendations. Standards such as the American Welding Society (AWS) guidelines or the relevant International Organization for Standardization (ISO) can provide invaluable references for selecting the suitable electrode. These standards are grounded in extensive research and testing, ensuring that the welding process yields optimal results.
ss 304 welding electrode
Experience from seasoned welders emphasizes the significance of maintaining a clean workspace and surface before welding. Contaminants, such as oil, dirt, or even fingerprints, can introduce foreign particles, compromising the weld's strength. Employing appropriate cleaning techniques, such as using solvents or wire brushes, is crucial to ensure that SS 304's natural corrosion-resistant properties are not negated in the welding process.
Trustworthiness in the context of SS 304 welding electrodes also extends to the source of the materials. Procuring electrodes from reputable manufacturers or distributors ensures high quality and consistency. These providers usually have traceable production processes and quality assurance measures, ensuring that each electrode meets stringent quality controls.
For those involved in fabricating structures requiring high aesthetic quality, weld appearance is often as critical as its functional properties. The E308L electrode not only supports strong, resilient welds but also facilitates a smooth, visually appealing finish. This aspect is particularly beneficial in industries where stainless steel's aesthetic attributes are as prized as its functional benefits.
In conclusion, the success of welding SS 304 stainless steel relies significantly on selecting the appropriate electrode, with the E308L standing out for its compatibility and performance. By adhering to expert recommendations, utilizing industry standards, and leveraging experienced insights, professionals can ensure high-quality welds that meet both structural and aesthetic demands. Trustworthy sourcing, meticulous preparation, and adherence to best practices form the backbone of reliable and successful stainless steel welding operations.