Choosing between solid welding wire and flux core can significantly impact your welding project's success. Both have their unique qualities and are suited to different types of jobs and environments. Understanding the distinctions can guide you to making an informed choice tailored to your specific needs.
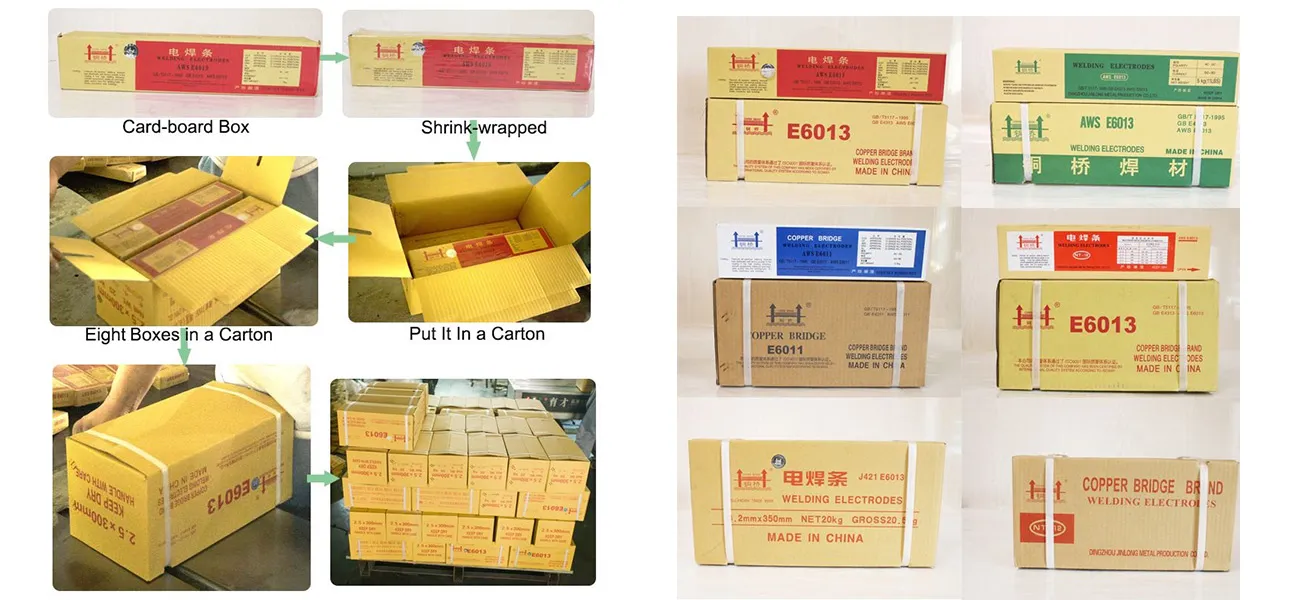
Solid welding wire is favored for its versatility and clean welding experience. It’s typically used for MIG (Metal Inert Gas) welding, which requires a shielding gas, commonly argon or a mixture of argon and CO2. The use of this shielding gas ensures a clean, spatter-free weld, making it ideal for indoor welding projects where environmental control is more manageable. This makes solid wire a preferred option for applications in the automotive industry, metal fabrication, and production environments where high precision and high-quality welds are demanded.
The absence of flux means less residue is left on the welds, resulting in a cleaner finish. It's best suited for welding thin materials, typically less than half an inch thick. However, using solid wire necessitates a more stable environment, as external factors like wind can disrupt the shielding gas, leading to compromised weld integrity.
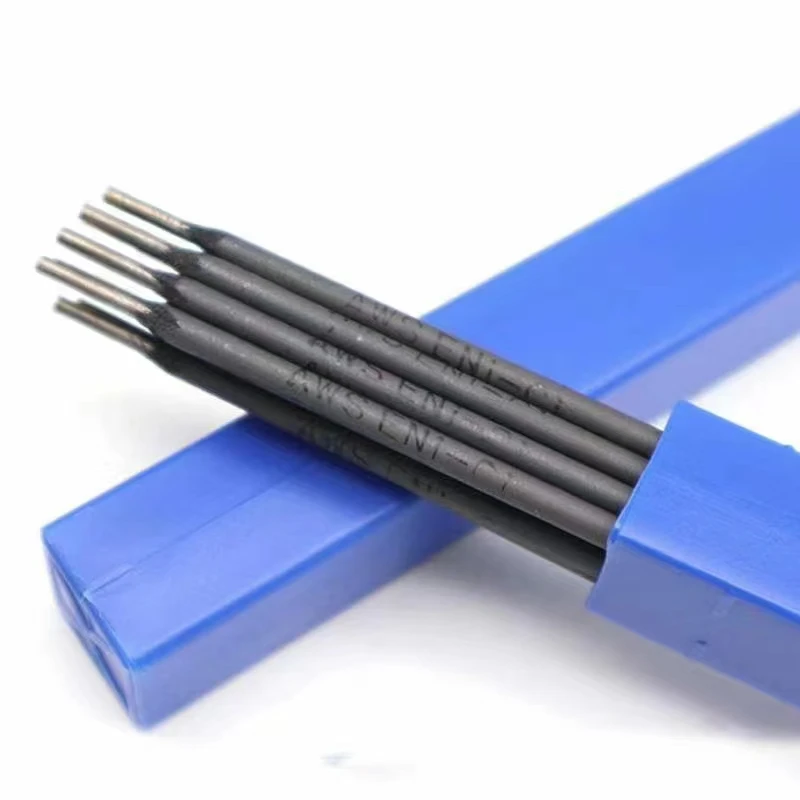
Flux core wire, on the other hand, is designed for ease of use and adaptability in less controlled environments. Unlike solid wire, it doesn’t require external shielding gas as it is self-shielded; the wire contains a flux that produces the necessary gas when heated. This characteristic makes flux core welding particularly useful for outdoor applications where wind could affect shielding gas, such as in construction, shipbuilding, and heavy equipment repair.
Moreover, flux core wires excel in welding thick materials – typically above half an inch – due to their capability to produce deeper penetration and sturdier welds. This makes it a go-to solution for manufacturing industries and construction projects requiring robust structural integrity. The flux within the core does result in slag, which requires additional work to clean off post-welding, but it also allows the wire to adapt to imperfect surface conditions and contaminants.
solid welding wire vs flux core
From an expertise perspective, choosing between solid wire and flux core often falls on the project's specific requirements. Solid wire offers precision and a cleaner finish with less post-weld cleanup, ideal for controlled environments and thinner material projects. Flux core's rugged versatility shines in outdoor and structural contexts, dealing better with thicker materials and less pristine surfaces.
Considering authoritativeness and trustworthiness, manufacturers and seasoned welders emphasize the importance of understanding these wires' characteristics related to their strengths and limitations. For instance, professional welders will often suggest practicing on scrap pieces to get accustomed to each wire type before embarking on crucial projects to avoid mishaps and material waste. Equipment readiness, such as ensuring you have the correct feeding mechanism and roller types for your specific wire, cannot be understated in maintaining efficiency and product quality.
Real-world experiences consistently show that there’s no one-size-fits-all answer. Veteran users of welding technologies frequently relay stories of learning curves when switching wire types. Continuous education through workshops, tutorials, and hands-on practice sessions are highly recommended, especially when deploying new technologies or methods in different operational conditions.
In conclusion, the debate of solid welding wire versus flux core rests significantly on the demands and conditions of the welding task at hand. By aligning the choice of wire to the environmental conditions, material thickness, and specific requirements of the job, one can harness the strengths of each to achieve the most efficient and quality outcome. Hence, understanding the application and ensuring the right conditions are met, leveraging expertise and continued learning, stands as the cornerstone of successful welding projects.