Normal welding rods, often overlooked yet essential tools in the arsenal of any welding professional, are indispensable in ensuring the strength and durability of metal joints. When selecting a welding rod, understanding its composition, application, and usage can make all the difference in achieving superior weld quality. With decades of collective industry experience, experts emphasize the significance of using the right rod for specific projects to uphold standards of safety and efficiency.

Fundamentally, a normal welding rod is a consumable electrode that plays a dual role in the welding process. It conducts the welding current to the arc and supplies filler material to the joint, becoming an integral component of the final weld pool. The varied compositions of these rods, from mild steel to specialty alloys, dictate their suitability for particular metals and environments. Professionals in the field understand that matching the rod specification to the base metal properties is crucial in minimizing defects and maximizing the weld strength.
Experienced welders often stress the importance of electrode coating, which affects the stability of the arc and the resultant quality of the weld. Normal welding rods are typically coated with a flux material that serves multiple purposes it safeguards the weld area from atmospheric contamination, enhances the arc stability, and assists in the removal of impurities from the metal surface. The flux coating also plays a decisive role in producing slag, which covers the weld bead and protects it during cooling.
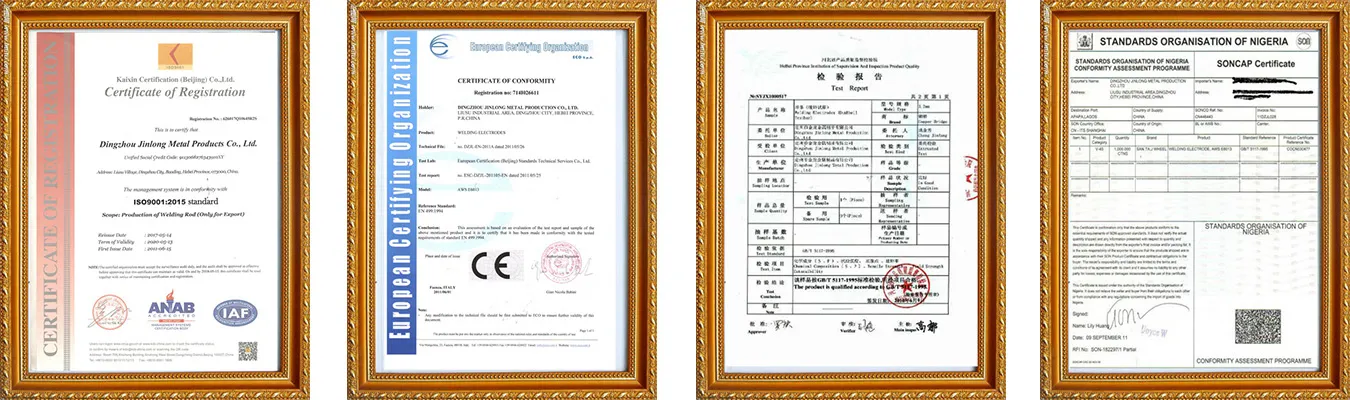
Over the years, there has been a notable evolution in the technology and materials used in welding rods, aligning with advancements in welding techniques. Leaders in the industry highlight that investing in state-of-the-art rods can significantly reduce downtime and improve overall productivity. The right choice of rod can also contribute to cost-efficiency by reducing the need for post-weld treatments such as grinding or finishing.
normal welding rod
For those striving for expertise in the welding domain, understanding the technical specifications often found in rod packaging—such as tensile strength, electrode polarity, and recommended operating conditions—is vital. These parameters are indicative of a welding rod’s performance and its adaptability to various applications. Moreover, consulting with seasoned professionals or manufacturers can provide additional insights into achieving optimal results.
Trust in normal welding rods also emanates from their proven track record in diverse applications. From construction projects and shipbuilding to automotive repair and pipeline infrastructure, these rods have consistently delivered reliable performance. Testimonials from industry experts and seasoned welders reinforce their reputation for versatility and dependability.
Beyond technical knowledge,
the credibility of a welding rod brand speaks volumes. Trustworthy manufacturers adhere to stringent quality controls and industry standards, ensuring each rod meets the rigorous demands of welding tasks. Establishing a relationship with credible suppliers not only guarantees the quality of welding rods but also provides access to specialized support and up-to-date product innovations.
In conclusion, normal welding rods largely determine the outcome of welding endeavors. From their chemical composition and coating with flux to the operational expertise required, understanding these factors is essential for anyone who desires excellence in their welds. Industry veterans and experts alike attest to the impact these seemingly simple tools have on the integrity and success of metalwork projects. By ensuring adherence to standards of quality and precision, normal welding rods have cemented their place as a cornerstone in the field of welding.