The ER 7018 welding electrode, often celebrated in metalworking circles, is a product etched in the annals of industrial evolution. Born from the crucible of technological progress, the ER 7018 has become an indispensable tool for welders seeking precision, strength, and safety. Yet, beyond its technical specifications, lies a narrative rich with real-world experiences and insights that are invaluable for anyone navigating the welding domain.
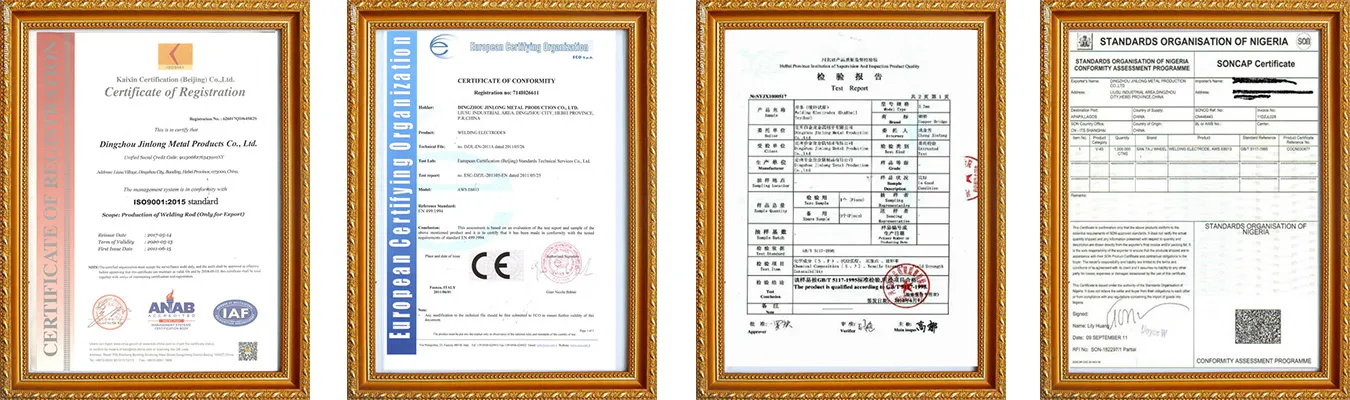
The journey of mastering the ER 7018 begins with understanding its distinct characteristics. Known as a low-hydrogen rod, it is particularly revered for its ability to produce strong, crack-resistant welds. This electrode's versatility is showcased in its application across various sectors like construction, shipbuilding, and pipelines, where it consistently demonstrates its reliability under stringent demands. Its coating, laden with iron powder, not only enhances weld metal deposition but also optimally shields the arc, ensuring stability and precision.
Experts in welding commend the ER 7018 for its unique usability across different positions with AC and DC currents. This flexibility makes it a go-to for many seasoned professionals who require adaptability in their welding practices. However, a nuanced understanding of its storage requirements is crucial. This electrode is hydrophilic; hence, proper storage in a dry, moisture-free environment is imperative to preserve its low-hydrogen properties and prevent weld defects.
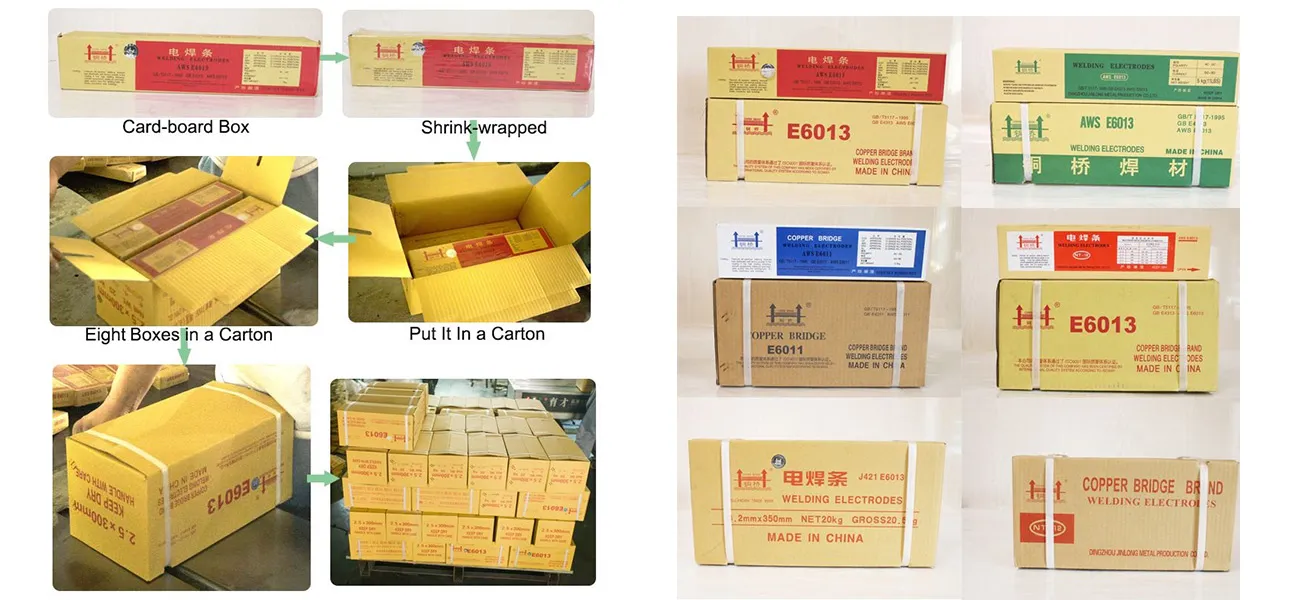
The expertise in deploying ER 7018 effectively is illustrated through real experiences shared by welders across the globe. Consider a scenario from a large infrastructure project where the welders were faced with the challenge of extreme cold. The ER 7018 was put to the test; its low hydrogen content was crucial in preventing cold cracking, a common risk in such environments. The welders preheated their base materials and maintained these temperatures during the welding process. This experience not only affirmed the electrode’s capabilities but also highlighted the importance of adhering to procedures that complement the electrode’s strengths.
Professional welders often narrate stories of its authority in seismic areas. Structures built in such zones require welds that can endure considerable stress and movement. The ER 7018's welds have been proven to deliver superior resilience, acting as silent sentinels even as tectonic forces roil below. This reinforces the electrode's repute not just among practitioners but also among engineers and planners who prioritize safety and durability.
er 7018
Trust in the ER 7018 extends beyond anecdotal endorsements. Data-driven analysis and years of empirical research lend this product a trustworthiness that few in its class can rival. Laboratory evaluations consistently highlight its tensile strength, reaching upwards of 70,000 pounds per square inch. Furthermore, regulatory bodies and industry standards endorse its use, adding a layer of reassurance for decision-makers tasked with choosing suitable welding materials for critical projects.
From a professional standpoint, wielding the ER 7018 is not merely a technical choice, but a commitment to quality and excellence. The electrode's identity is woven into the fabric of industries that literally build and shape the world. For budding welders, gaining mastery over this tool is akin to earning a rite of passage into the ranks of skilled metalworkers. It demands respect for its capabilities and an understanding of the nuanced dance between heat, pressure, and materials.
The path to optimizing the use of ER 7018 involves a blend of technical training and hands-on experience. Welding schools and workshops offer courses that focus specifically on the intricacies of this electrode, encouraging practitioners to refine their skills under the tutelage of seasoned experts. Moreover, sharing best practices and challenges within the professional community enhances collective expertise, ensuring that the knowledge surrounding ER 7018 continues to evolve and expand.
In summation, the ER 7018 is more than just a welding electrode; it is a testament to the progress in material sciences and industrial craftsmanship. Its enduring legacy is supported by extensive expertise, authoritative endorsements, and a foundation of trust built through consistent performance across innumerable applications. For those engaged in the art and science of welding, the ER 7018 stands as both a challenge and a partner in innovation, calling for skill, knowledge, and an unwavering commitment to excellence.