In the realm of welding and metalwork, selecting the right filler rod can be the difference between success and failure, particularly for projects requiring precision and reliability. The ER312 filler rod stands out as an exceptional option, renowned for its versatility and superior performance across various applications.
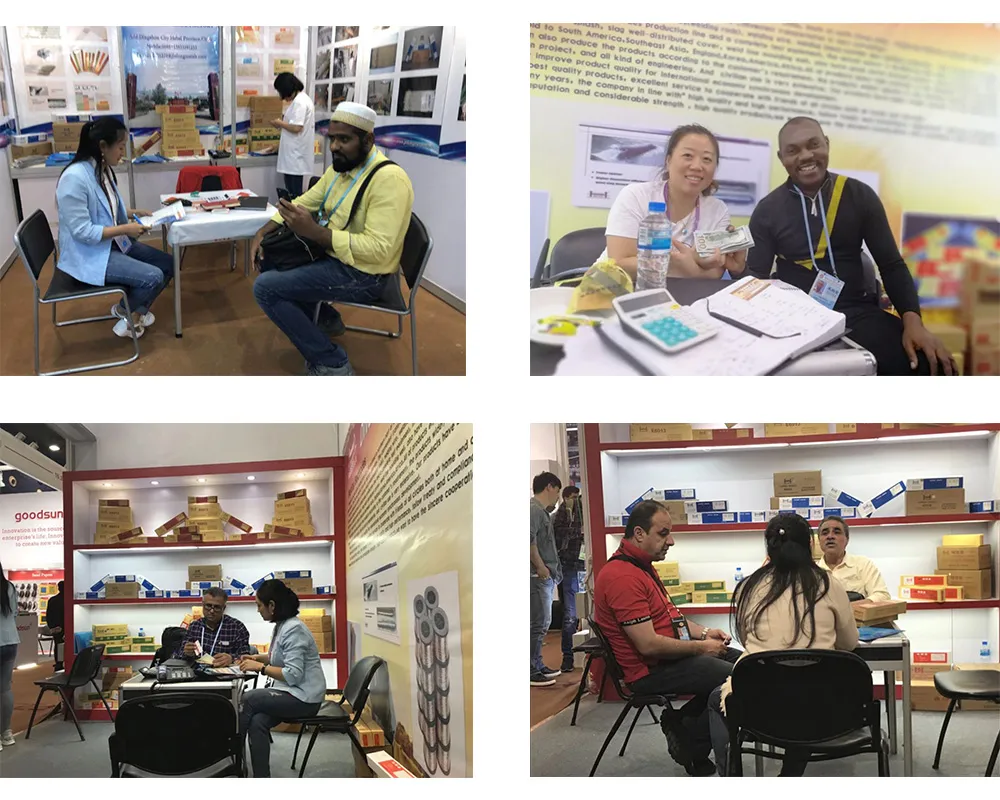
Experienced welders and engineers consistently emphasize the importance of utilizing ER312 filler rods due to their consistent results in challenging projects. This product is specifically designed to cater to the nuanced needs of high-stress environments, where variations in temperature and mechanical forces are prevalent. It is engineered from a high-grade stainless steel alloy, offering a unique composition that ensures not only strong, durable joints but also remarkable resistance to cracking and corrosion.
Professionals widely acknowledge ER312 for its outstanding ability to join dissimilar metals. This capability makes it an irreplaceable resource in industries such as aerospace, automotive, and petrochemical, where components are often subjected to severe operational stresses. The filler rod's robust performance in such conditions is a testament to its unparalleled metallurgical properties, including a high percentage of chromium and nickel. These elements not only enhance its strength and ductility but also contribute to its heat resistance, enabling it to withstand temperatures that would otherwise compromise lesser materials.
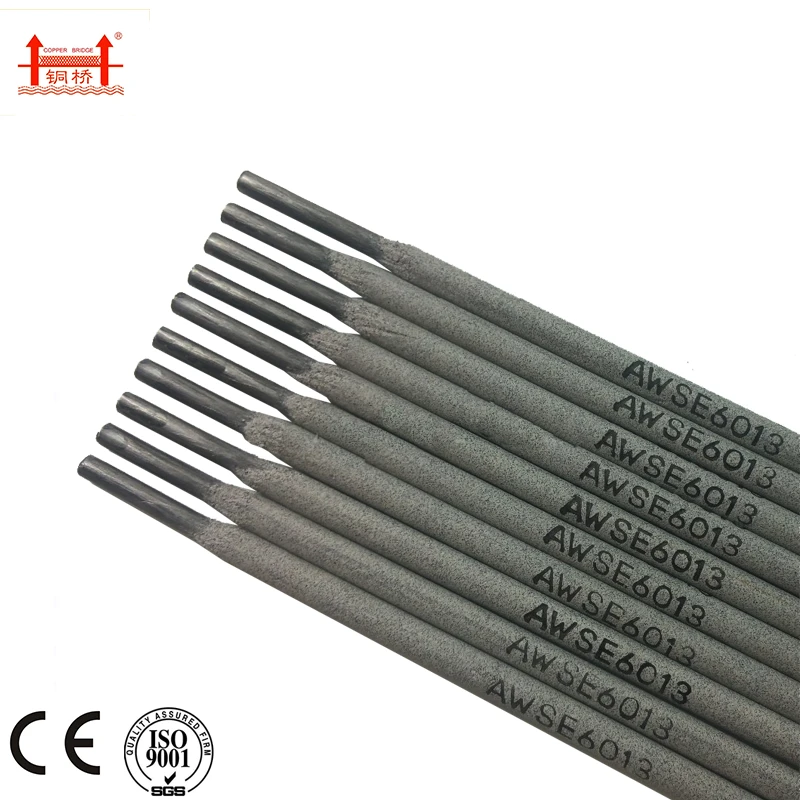
Exploring the practical aspects of using ER312 filler rods in a workshop setting reveals its ease of use and adaptability. Its unique formulation allows for greater control and precision during the welding process, facilitating smooth application even in the hands of less experienced welders. As echoed by lead welding instructors in vocational schools, the filler rod's forgiving nature during application makes it a recommended choice for learners honing their skills in advanced welding techniques.
er312 filler rod
Another noteworthy aspect of ER312 filler rods is their contribution to reducing post-weld cleanup and maintenance efforts. Projects utilizing these rods consistently show cleaner, more aesthetically pleasing joints, minimizing additional finishing work and thereby enhancing overall project efficiency. This reduction in labor and material costs translates into significant savings, a benefit frequently highlighted in professional welding journals and industry publications.
Authoritative sources in metallurgical research point to the unique combination of elements in ER312 rods as a primary factor for their successful performance across various scenarios. Studies from recognized institutions underscore their indispensability in welding operations involving carbon steel and stainless steel, where other rods might falter. The research also highlights the cost efficiency achieved by manufacturers and contractors, who increasingly opt for ER312 as their go-to choice, owing to its reliability and reduced risk of joint failure.
Moreover, ER312's track record in producing repeatable, high-quality results fosters a deep level of trust among those who rely on weld integrity for safety-critical applications. Testimonials from field technicians consistently report fewer incidences of joint failure or need for rework when ER312 rods are employed, further reinforcing their reputation for durability and excellence.
In summary, the ER312 filler rod is distinguished by its superior metallurgical properties, which grant it the flexibility and strength necessary to excel in demanding environments. Its ability to forge reliable bonds between dissimilar materials, combined with ease of use and economic practicality, makes it a preferred choice for experienced professionals and newcomers alike. By offering consistent, high-quality outcomes, the ER312 filler rod not only satisfies rigorous industrial demands but also sets a benchmark for reliability and performance in the welding industry.