Different welding electrodes play a critical role in the quality and properties of a weld. The choice of the right electrode is fundamental to achieving strong, durable, and defect-free welding. With a multitude of options available, each type of welding electrode brings unique characteristics suitable for specific materials and applications, making it essential for welders to choose wisely.
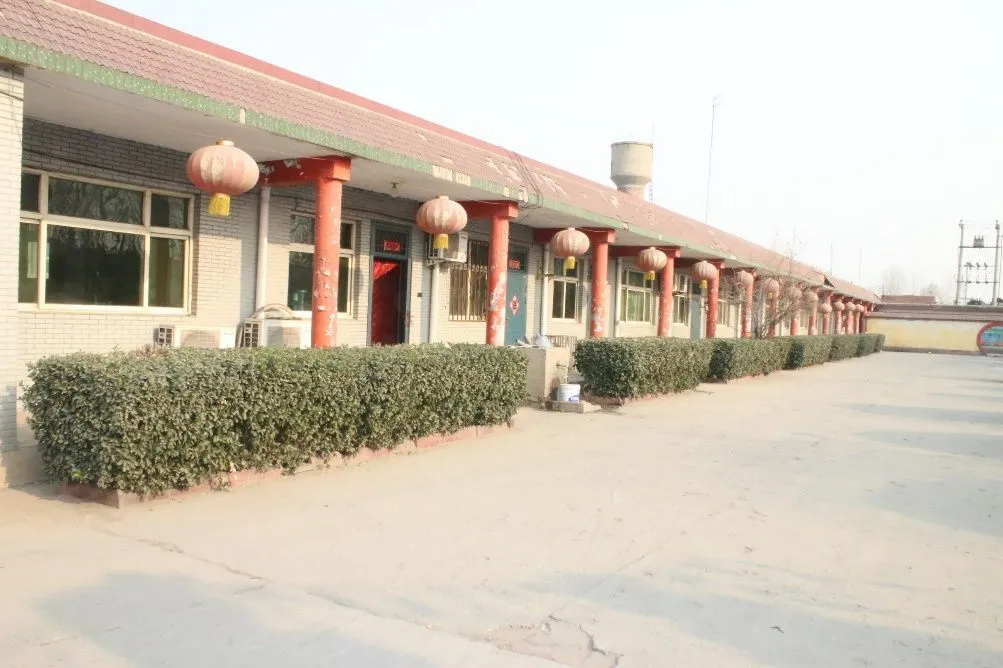
Electrodes are broadly classified into two categories consumable and non-consumable. Among consumable electrodes, the most common types are shielded metal arc welding (SMAW) electrodes, flux-cored arc welding (FCAW) electrodes, and gas metal arc welding (GMAW) electrodes. Each serves different purposes and materials. SMAW electrodes, for example, are perfect for rugged conditions and work wonders in outdoor settings, providing protection against moisture due to their flux coating. This makes them indispensable for construction and shipbuilding projects.
Flux-cored arc welding electrodes are valued for their versatility, offering high deposition rates that boost productivity. The self-shielded variants excel when there’s no provision for external gas shielding, making them a go-to in field repairs and heavy-duty industrial welding, where speed without compromising weld quality is crucial. GMAW electrodes or MIG wires offer superior control and require less skill from the operator, making them suitable for beginners and available in varieties like solid and metal-cored wires, each catering to different needs based on welding positions and types of joints.
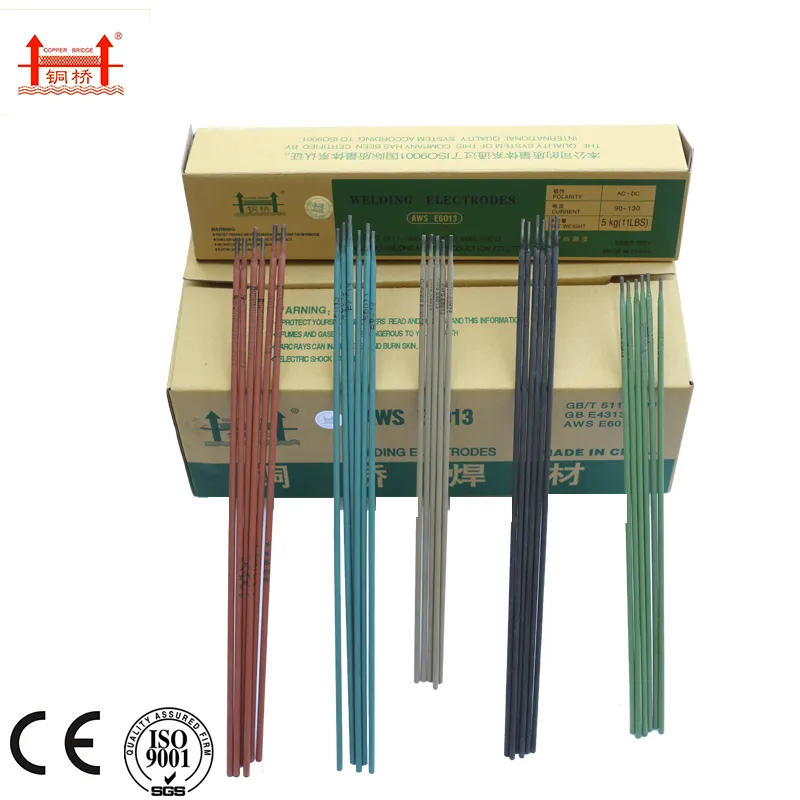
Non-consumable electrodes, mainly used in gas tungsten arc welding (GTAW or TIG) processes, are typically made from tungsten. Their main advantage lies in providing a clean and precise weld, which is essential in industries where precision and aesthetics are paramount, such as aerospace and automotive manufacturing. The challenge here is the skill level required, as TIG welding demands a steady hand and great expertise to manage the tungsten electrode effectively without contamination.
Innovation in welding electrodes has seen the development of low-hydrogen electrodes that significantly reduce the likelihood of cracking in high-strength steels. These electrodes are essential in the fabrication of pressure vessels and pipelines, where structural integrity is a priority. In contrast, high deposition rate electrodes optimize efficiency in large scale productions, reducing time and cost while maintaining quality.
different welding electrodes
Understanding the specifics of material compatibility and environmental requirements is crucial. Stainless steel welding, for instance, has its unique demands. Employing electrodes that mirror the alloy composition can prevent corrosion and ensure the longevity of the weld. Nickel-based alloys, used extensively in chemical processing industries, highlight the need for electrodes that withstand extreme temperatures and corrosive environments, affirming the importance of matching electrode composition to base materials for the best results.
The selection process should also consider the mechanical properties required in the finished piece, such as tensile strength, corrosion resistance, and ductility. Efficient electrode usage not only enhances performance but also brings down overall costs, from material savings to reduced labor time.
Every weld is a testament to the combination of choice and skill, underscoring the need for continuous learning and adaptation to new technologies in welding electrodes. Staying informed through manufacturers’ specifications, welding forums, and field tests helps fabricators and welders make informed decisions, ensuring the structural soundness and reliability of their projects.
For consumers, relying on certified welding professionals who understand different electrode types guarantees optimal outcomes. Trust in their expertise ensures that every welding task is executed with precision and care, leveraging the best-suited electrodes for specific welding challenges.