In the world of welding, cast iron poses unique challenges due to its brittle nature and the high carbon content that makes it susceptible to cracking. As a result, selecting the right electrode is crucial for those who seek durable and reliable repairs or fabrications using cast iron materials. The topic of cast iron electrode numbers is one of particular interest, offering insights into their usage, applications, and best practices.
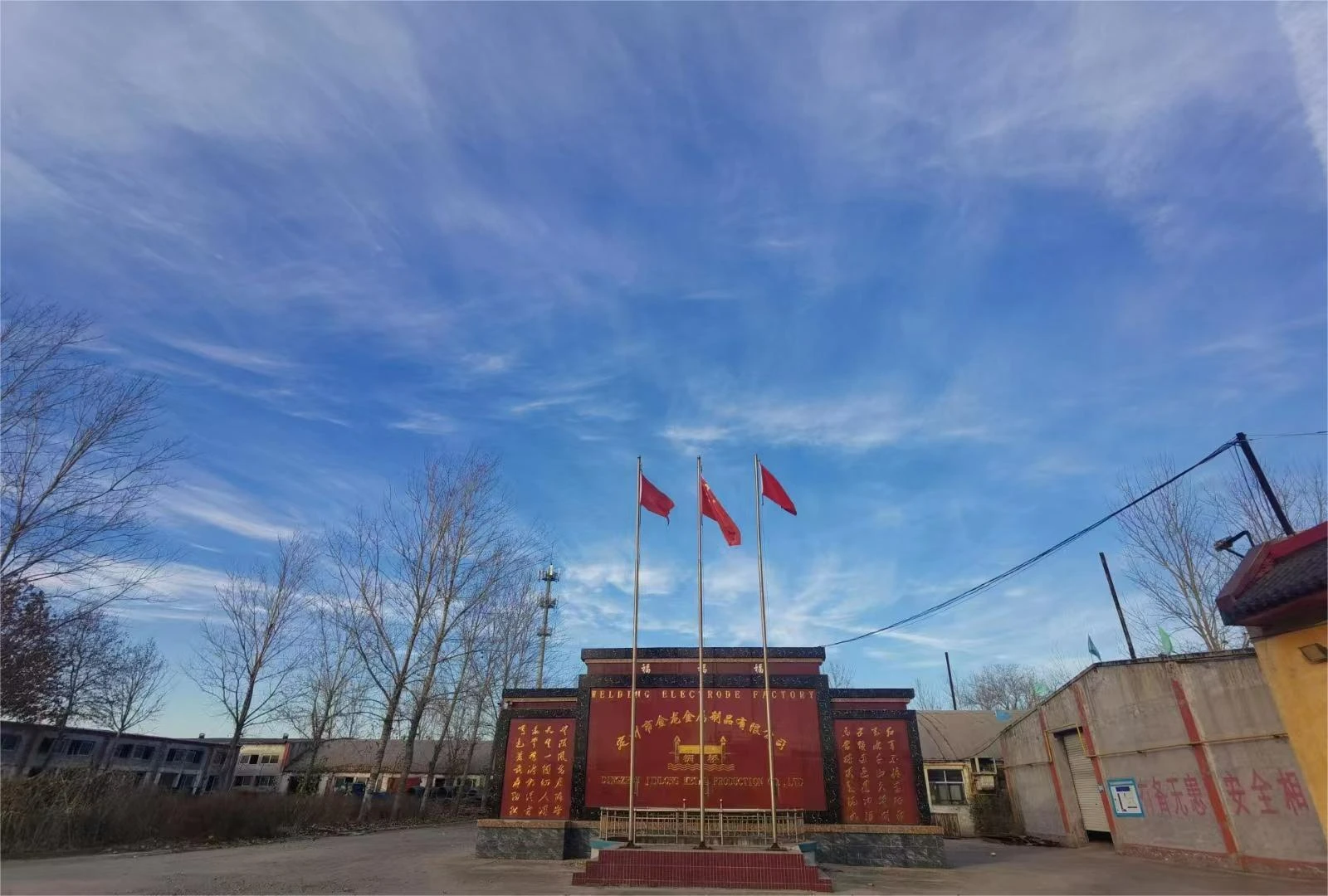
Understanding the nuances of cast iron electrodes begins with recognizing the significance of electrode numbers. These numbers serve as identifiers for specific electrode types, each tailored for various procedures and outcomes. They are pivotal for ensuring optimal compatibility with the workpiece, leading to successful welds.
The classification and functionality of cast iron electrode numbers are influenced by several factors, including the composition of the electrode material, the coating type, and the anticipated welding conditions. Most commonly, these electrodes are categorized by a numerical code that signifies their intended use cases. For instance, nickel-based electrodes, often denoted by numbers in their nomenclature, are widely recognized for their proficiency in welding cast iron. These electrodes are prized for their ability to produce machinable welds, making them suitable for applications demanding high precision.
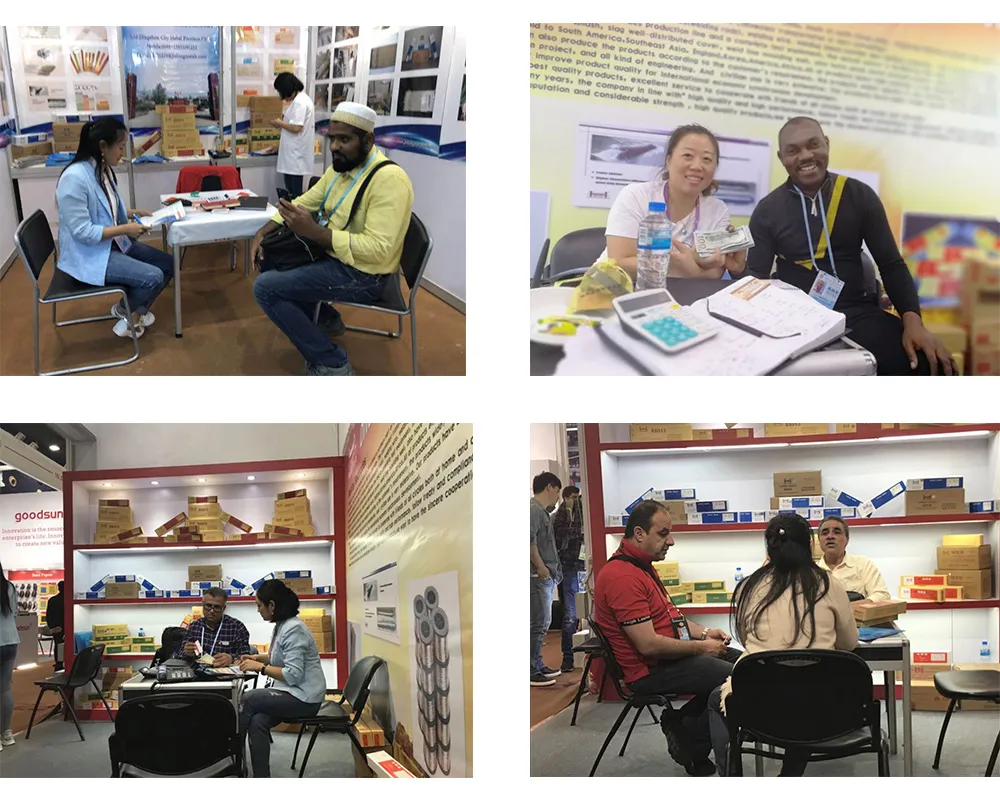
For welding practitioners, expertise in selecting electrode numbers can significantly impact the integrity and longevity of their work. Nickel-iron electrodes, which carry different numerical identifiers, offer a balance between strength and ductility. They are ideal for applications that require dependable structural integrity without excessive hardness, which can be a problem with some high-carbon welds.
Another consideration when dealing with cast iron electrode numbers is the electrode coating. The coating plays a crucial role in stabilizing the arc, controlling penetration, and affecting the appearance of the weld bead. It's not just the core composition of the electrode that matures these identifiers, but the coating type as well, which illuminates reasons behind preferences among experienced welders for certain numbered electrodes over others.
cast iron electrode number
Choosing the right electrode number for cast iron welding also involves understanding the welding positions and techniques. Typically, position dictates electrode diameter and type, as certain configurations require electrodes designed specifically for vertical or overhead operations. This is often reflected in the number or code associated with the electrode, which communicates its optimal conditions for use.
Technical mastery and the credibility of using properly designated cast iron electrodes are enhanced by familiarizing oneself with the specifics of post-weld treatments. Many projects call for a thorough understanding of stress relief techniques which, when combined with appropriate electrode use, mitigate against cracking and enhance the performance of the repaired or fabricated part.
The significance of cast iron electrode numbers extends beyond merely completing the task at hand. They ensure that welding practices adhere to quality standards and professional guidelines, fostering trust in the job's outcome. For businesses and craftsmen alike, honing the knowledge required to interpret these numbers fixes their reputation for quality and durability, reinforcing their authoritative stand in the industry.
In the competitive landscape of welding services and products, having an in-depth awareness of cast iron electrode numbers is more than a technical requirement; it is an essential component of sustainable craftsmanship and innovation. This expertise not only establishes authority with clients but reinforces trust, ensuring that welding professionals and hobbyists alike deliver outcomes that stand the test of time.
Professionals in the field advise that ongoing education and staying abreast of the latest electrode advancements are crucial to maintaining such expertise. Continuous learning and practice ensure that you remain ahead in optimizing your techniques with the right electrode choices, leading not only to improved performance but also to enhanced reputational authority and trustworthiness in the welding community.