Navigating the world of welding and metalwork can often feel daunting with the myriad of tools and materials available. Among the essential components for professionals and hobbyists alike is the welding electrode, a critical element in ensuring optimal performance and results. Specifically,
the “7018 electrode 1/16” stands out as a vital tool, offering unique benefits that set it apart. Here’s why industry professionals trust it and how it exemplifies the highest standards of quality and reliability.
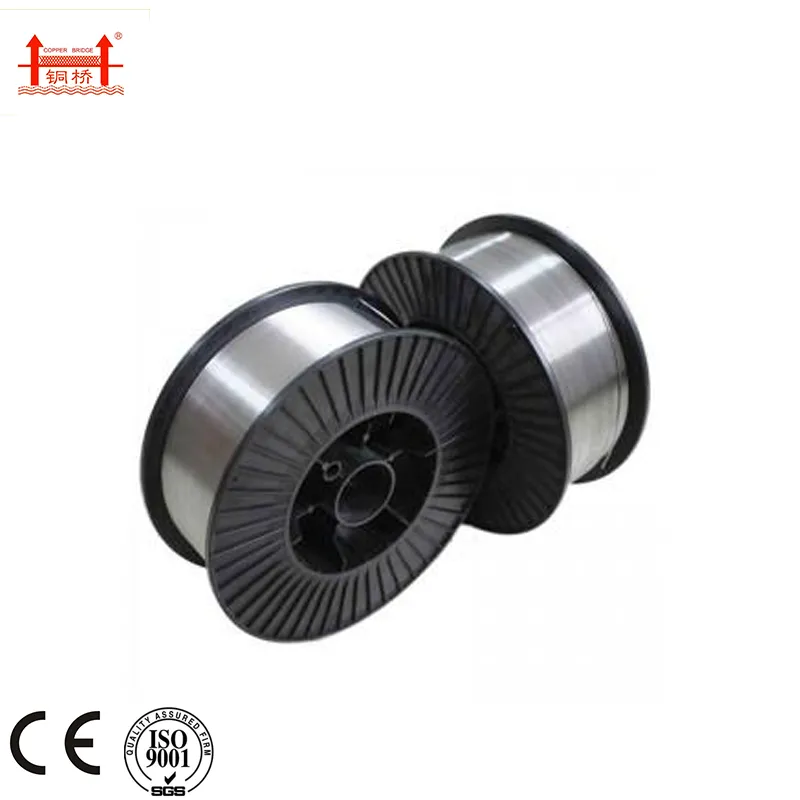
The 7018 electrode is renowned in the welding community for its low-hydrogen, iron powder flux coating, which dramatically reduces the potential for cracking in the welded area. Its composition is particularly beneficial for working with carbon and low-alloy steels, making it indispensable in construction, shipbuilding, and various manufacturing applications. The 7018 designation refers to the American Welding Society (AWS) classification, signifying the electrode's tensile strength (70,000 psi), its all-position capabilities, and minimal hydrogen content.
The specific 1/16” diameter version of the 7018 electrode addresses delicate or intricate tasks where precision is paramount. Its slender build allows for usage in tight or awkward spaces without compromising the integrity of the weld. In scenarios where thin materials are involved or detailed welds are necessary, the 1/16” electrode is a perfect match, providing a smooth bead with minimal spatter. This precision is a hallmark for artisans creating fine metalwork and engineers requiring exact joins in technical fields.

Professional welders often highlight the user experience with the 7018 electrode 1/16” as remarkably steady and forgiving. The arc is consistent, reducing unnecessary rework and enabling a cleaner finish. Its dependable nature minimizes the chances of porosity and suboptimal fusion, which can otherwise compromise structural integrity. Moreover, many professionals appreciate how the electrode’s stable arc simplifies the learning curve for newcomers to the trade, thereby enhancing skill acquisition.
7018 electrode 1 16
From an expertise standpoint, understanding the technical specifications and optimal usage scenarios for the 7018 electrode is crucial. Heat control, for instance, becomes especially critical when using a smaller diameter electrode like the 1/16. Proper technique will ensure that there’s no warping or overheating of the material. Experienced welders achieve this by maintaining a precise travel speed and angle, which minimizes the heat input—key to maximizing the electrode’s potential.
Authoritativeness in the use of the 7018 electrode comes from recognition and trust established by authoritative bodies and industry veterans. This electrode is certified by the AWS, a highly respected organization that sets the standard for welding quality around the globe. This certification assures users of its reliability and safety, built on rigorous testing and refinement over decades.
Trustworthiness is further bolstered by testimonials and case studies from the global welding community. Hydroelectric plants, bridge constructors, and pipeline developers often cite the 7018 electrode as an irreplaceable asset in their toolkit. Its durability in extreme conditions—withstanding stress from temperature fluctuations and heavy loads—demonstrates why it remains the electrode of choice for rigorous projects and environments where failure is not an option.
In conclusion, the 7018 electrode 1/16” is not merely a tool; it's a testament to the evolution of welding technology and a trusted ally for those who demand excellence in their craft. Whether for personal projects or large-scale engineering feats, its contribution to safe, robust, and high-quality welds cannot be overstated. Familiarity and experience with this electrode not only enhance the skills of a welder but also amplify their ability to innovate and produce work of unparalleled quality. Because in welding, as in all crafts, the right tools are the cornerstone of trust and success.