Choosing the right amperage for 6013 welding rods is a critical decision that can significantly impact the quality and integrity of your welding projects. For welding enthusiasts and professionals alike, understanding the nuances of using 6013 rods is essential for achieving optimal results. Delve into the world of 6013 welding rods with a focus on expertise, trustworthiness, and practical experiences shared by industry veterans.
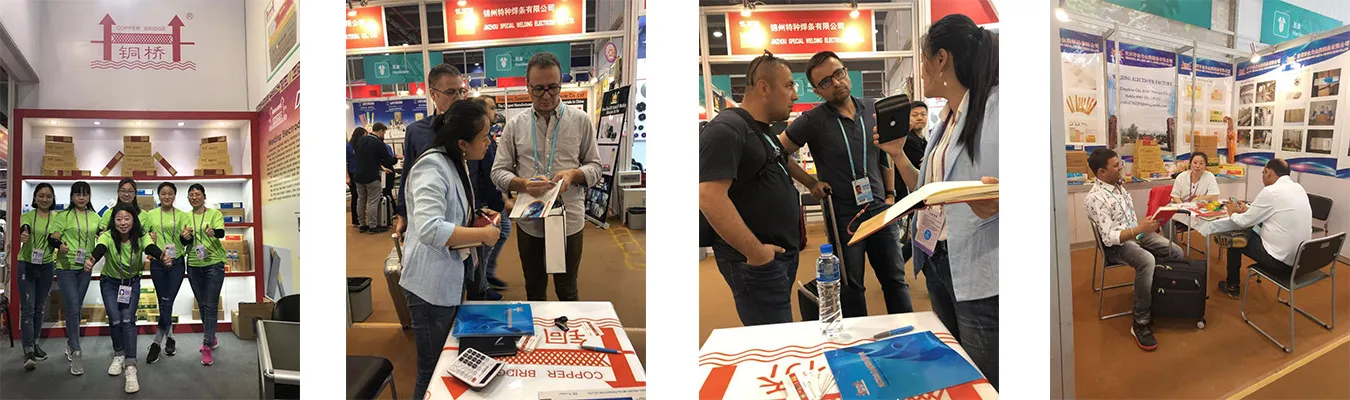
The 6013 welding rod is widely regarded for its versatility and ease of use, making it an ideal choice for both novice and seasoned welders. The numbers in its name shed light on its distinct characteristics. The first two digits, ‘60’, signify a tensile strength of 60,000 psi, indicating the robust nature of the electrode. The third digit, ‘1’, highlights its all-position usability, which allows welders the flexibility to execute welds horizontally, vertically, flat, or overhead. The final number, ‘3’, informs us about the specific coating and slag type, affecting the rod's behavior and usability.
When selecting the appropriate amperage settings for 6013 rods, it’s crucial to consider the diameter of the rod. For example, a 1/8 inch (approximately 3.2 mm) 6013 rod typically functions well within an amperage range of 80-130 amps, whereas a 3/32 inch (approximately 2.
4 mm) rod operates efficiently between 40-90 amps. These ranges are not just numbers; they are the result of rigorous testing and user feedback, ensuring precision and reliability in every weld.
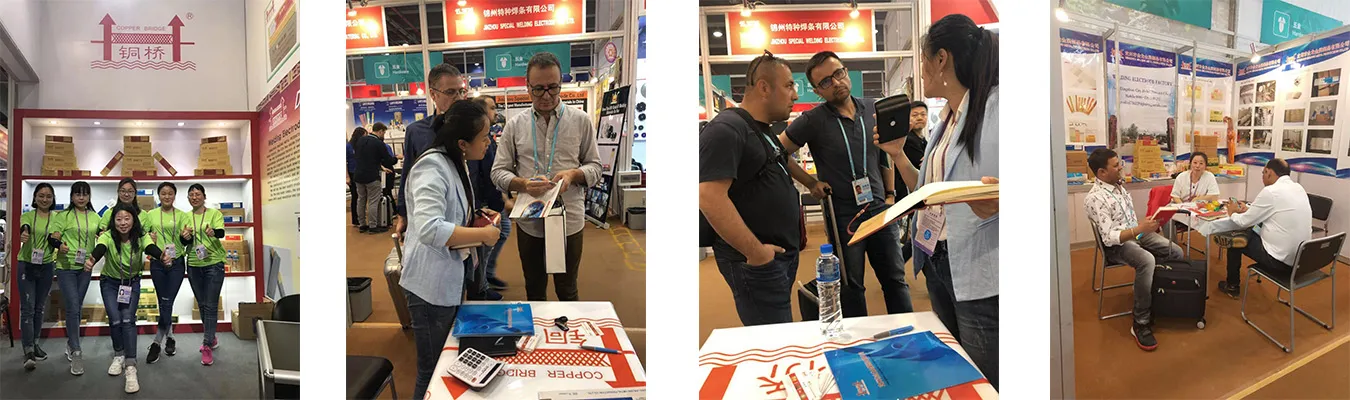
Successful welding with 6013 rods relies on maintaining a stable arc with minimal spatter, a hallmark of quality welds. Welders have shared their real-life tips for achieving this. Proper amperage adjustment is the cornerstone; setting the amperage too low may result in a weak arc that struggles to penetrate the metal effectively, leading to a brittle weld. Conversely, too high an amperage can result in excessive spatter and potential burn-through, compromising the metal's integrity. A well-balanced approach ensures a smooth, aesthetically pleasing weld.
Expert advice underscores the importance of matching the amperage with both the rod diameter and the material thickness. For thin materials, a lower amperage within the recommended range is preferable to prevent warping or burn-through, whereas thicker materials may require dialing up the amperage to secure full penetration and durability. The material composition, cleanliness, and ambient conditions further influence the ideal settings, emphasizing the need for seasoned judgment in selecting precise amperage.
6013 welding rod amps
Trustworthiness in welding communities often emanates from shared experiences and empirical results. Seasoned welders frequently advise conducting test welds on scrap metal to fine-tune amperage settings before embarking on the main project. This practice not only builds confidence but also guarantees higher success rates and reduces unforeseen complications.
Beyond technical adjustments, attention to consumables and equipment also plays a pivotal role. Consistent electrode quality can drastically affect amperage efficiency. Investing in high-quality 6013 rods from reputable manufacturers ensures uniform coating and slurry composition, reducing variables that could affect amperage responsiveness.
In the quest for superior welds, the authoritative voices in the welding domain advocate continual learning and adaptation. Keeping abreast of innovations and peer reviews in welding techniques, equipment advancements, and material sciences offers welders a competitive edge. Moreover, fostering a culture of safety and best practices fortifies the trust placed in welders by clients and peers alike.
The 6013 welding rod, with its forgiving nature and adaptability, stands as a testament to effective engineering and user-centered design. Mastering the amperage nuances of these rods is not merely a technical exercise; it is a journey that blends precise calculations with human intuition, informed by every weld perfected and every lesson learned.