Welding stainless steel with a stick welder, often termed shielded metal arc welding (SMAW), is a crucial skill for many fabricators and DIY enthusiasts. This process, while distinct from other welding methods like MIG or TIG, offers unique advantages, enabling the creation of sturdy joints even in less-than-perfect conditions. Here's a comprehensive insight on how to master the art and science of welding stainless steel with a stick welder.
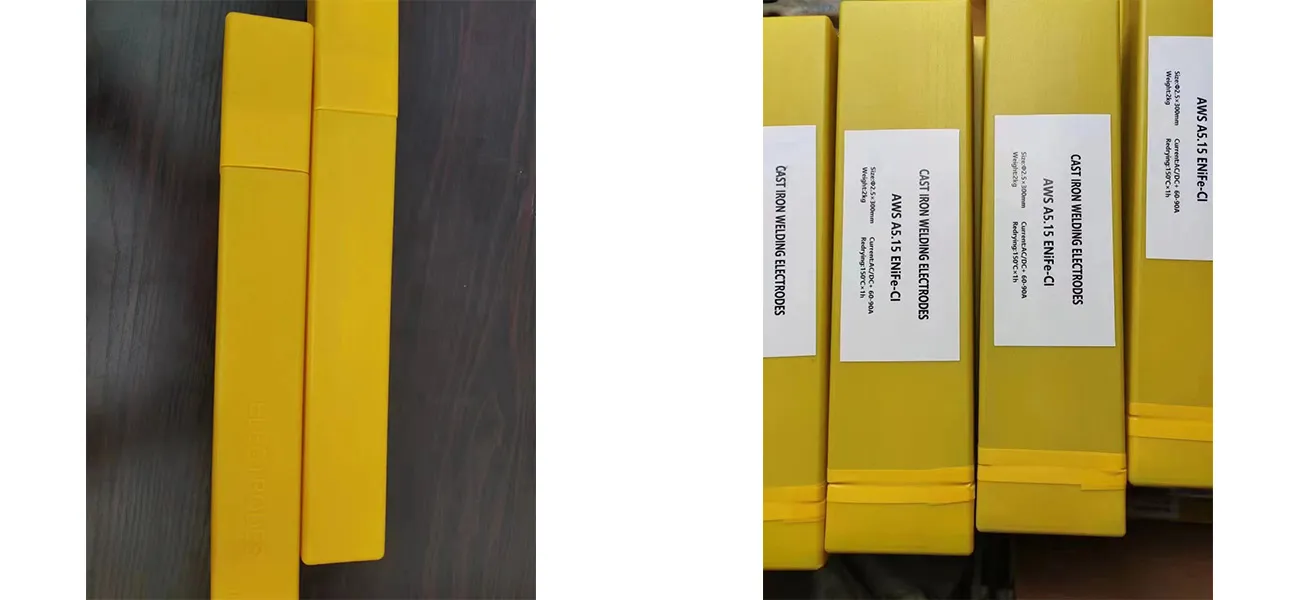
Selecting the Right Electrode
When welding stainless steel, choosing the correct electrode is paramount. The commonly used electrode for this process is the E309L-16 or E316L-16. They are specifically formulated to provide the necessary corrosion resistance and maintain the integrity of stainless steel. It's important to select an electrode with a matching or superior alloy content compared to the base metal.
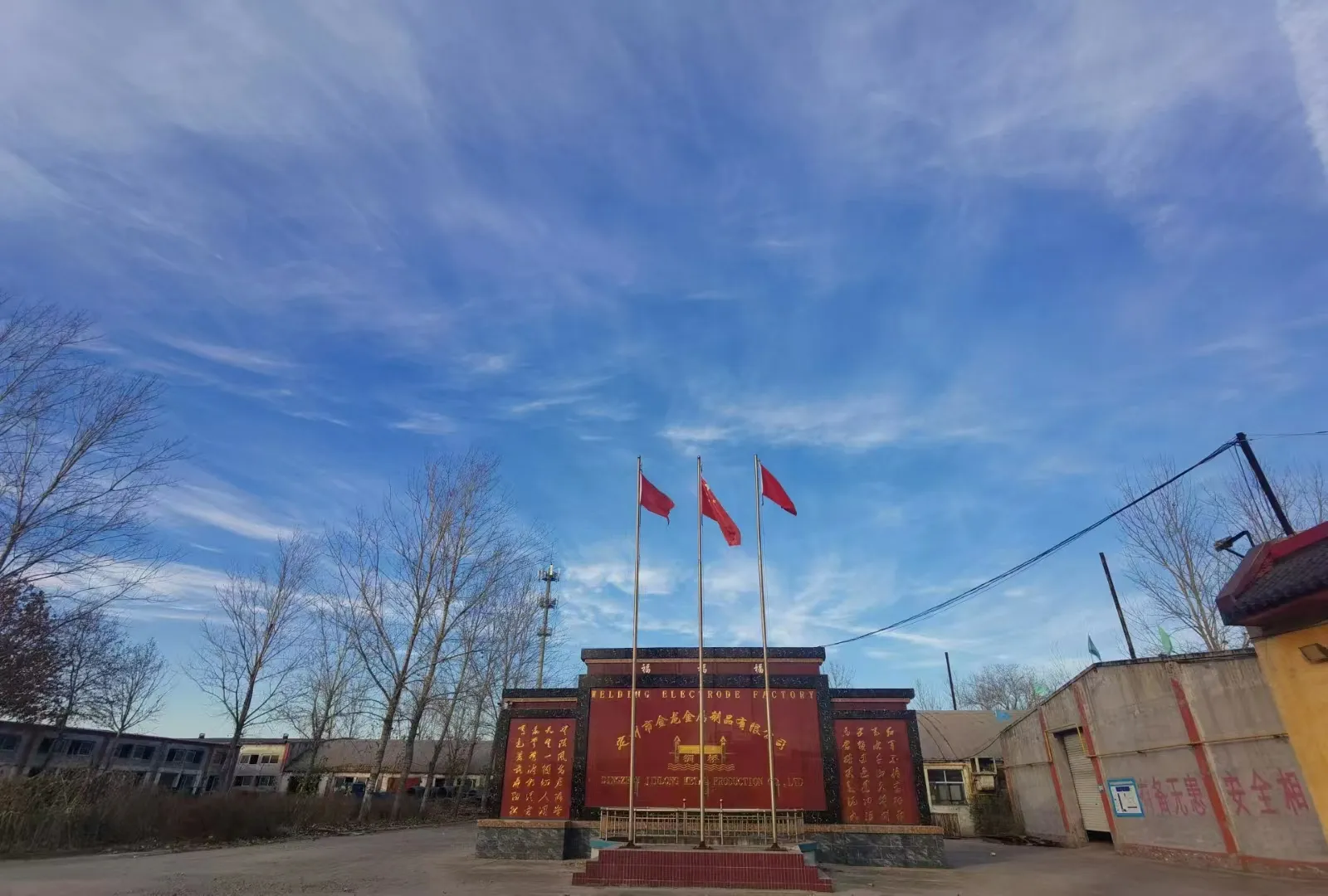
Power Settings and Machines
The choice of a welder and its settings significantly influences the quality of the weld.
Stick welding stainless steel requires a direct current electrode positive (DCEP) setting. Ensuring your machine is capable of this polarity is crucial. Additionally, fine-tuning the amperage based on electrode diameter is necessary; a general rule is that thicker electrodes need higher amperage.
Surface Preparation
Surface preparation is often an overlooked aspect of welding but is vital for stainless steel. The surfaces must be cleaned thoroughly to remove oil, grease, dirt, or oxide layers. A stainless steel brush is recommended to avoid contamination, as cross-contamination with carbon steel particles can undermine the stainless steel's corrosion resistance.
Welding Technique
Mastering the technique entails understanding the correct travel angle and speed. Holding the electrode at a 15-30 degree angle from vertical and maintaining a steady hand ensures a stable arc and reduces spatter. The key is to weld with a slightly faster travel speed than one might use with carbon steel. This method minimizes heat buildup and reduces the risk of warping or altering the metallurgical properties of the stainless steel.
welding stainless steel stick
Controlling Heat Input
Stainless steel's lower thermal conductivity compared to carbon steel means it retains heat, making it susceptible to warping. To control heat input, one should use a smaller electrode size and employ intermittent welding techniques. Tack-welding at regular intervals can hold the workpieces in place and prevent distortion. Allowing the previous welds to cool before continuing can also maintain the structural integrity of the project.
Shielding Considerations
Although stick welding inherently provides its own shielding, atmospheric contamination remains a risk. Utilizing a slight back-and-forth motion at the conclusion of a weld bead can adequately cover the crater, sheltering it from air ingress during cooling. Performing welding operations in a draft-free environment further reduces the exposure to contaminants.
Post-Weld Cleaning
The finishing process is just as critical as any other stage in welding. To maintain corrosion resistance, post-weld cleaning should be meticulous. Any discoloration or oxidation that appears can be removed with a stainless steel wire brush or a suitable chemical passivation process. This not only enhances the aesthetic appeal of the stainless steel but also restores its resistance to corrosion.
Safety Precautions
Safety cannot be overstated—welding emits UV radiation and hazardous fumes. Proper protective gear, including auto-darkening helmets, gloves, and respirators with appropriate filters, ensures the safety of the welder. Also, maintaining a well-ventilated workspace is crucial in preventing the build-up of potentially harmful fumes.
Mastering the craft of welding stainless steel with a stick welder requires an understanding of both the material characteristics and the subtleties of the welding process itself. Through meticulous preparation, the right equipment, and a commitment to safety, one can achieve high-quality, robust welds on stainless steel structures. By continually refining one's technique and embracing new advancements, welders can ensure that their projects stand the test of time both in function and form.