Selecting the right welding rod is critical not only for the success of your welding project but also for ensuring the structural integrity and longevity of the finished piece. This task, though complex, becomes straightforward when guided by a well-structured welding rod selection chart. With various options on the market, understanding which welding rod fits your specific needs can dramatically affect your work quality and efficiency.
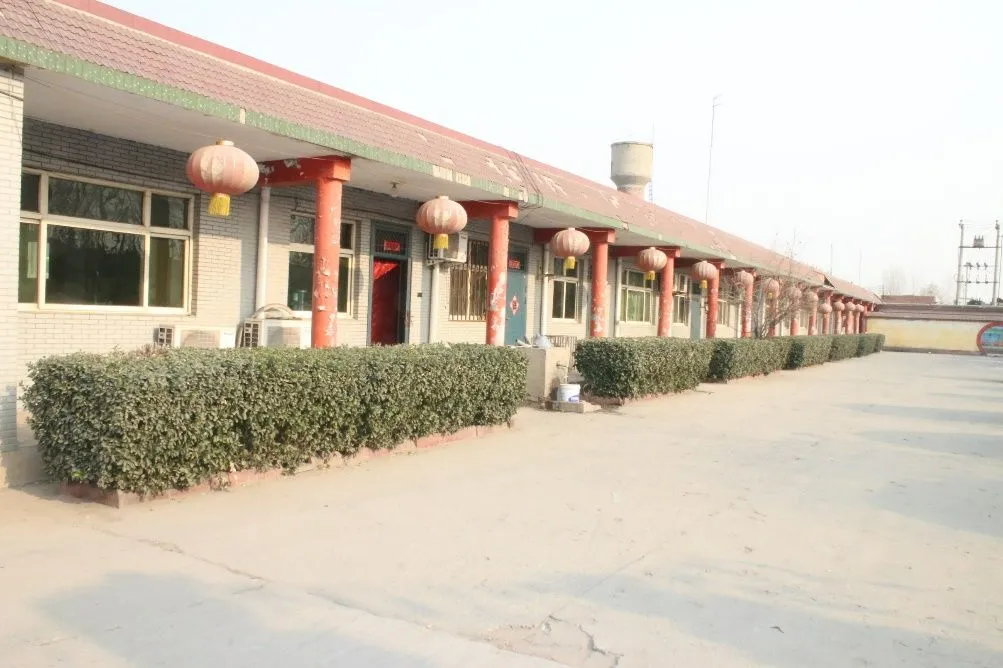
Understanding Welding Rod Specifications
Welding rods, often referred to as electrodes, are fundamentally categorized based on their coating and core material, which influence the weld's deposition rate, penetration, and overall weldability. Familiarity with key designations like E6010, E6011, E7018, and others isn't merely academic; it conveys significant insights into the electrode's tensile strength, position, and coating material.
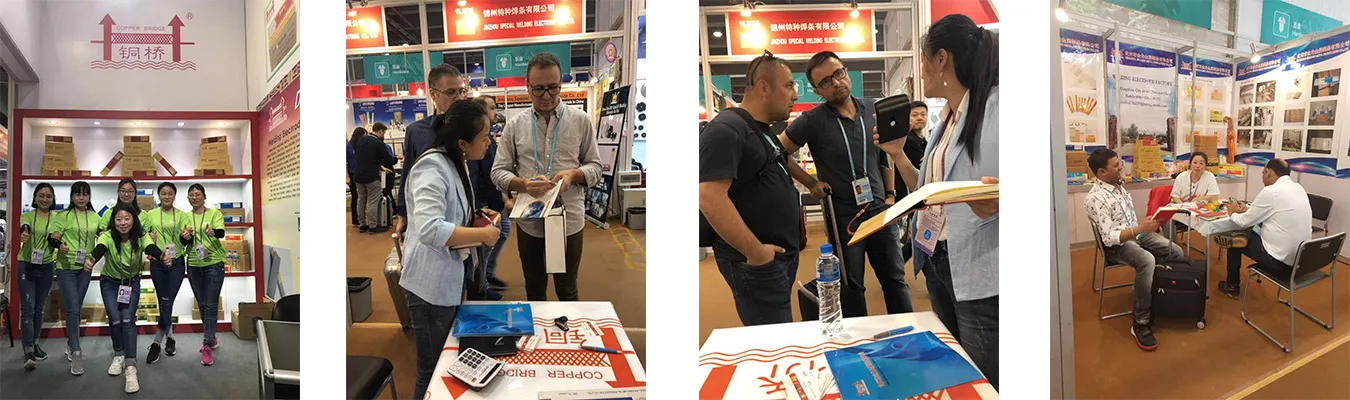
Important Factors in Welding Rod Selection
1. Base Material The first step in selecting the appropriate welding rod is to consider the material you are welding. For mild steel, E6010 or E6011 is suitable due to their deep penetration capabilities ideal for rusty or dirty steel surfaces. For high-pressure applications or structural steel, E7018 is invaluable due to its low hydrogen content and superior arc stability.
2. Welding Position The electrode's usability in different positions (flat, horizontal, vertical, overhead) should align with project requirements. For instance, E7018 offers excellent all-position capabilities, making it a versatile choice for various welding applications.
3. Current Type The type of current available—Alternating Current (AC) or Direct Current (DC)—determines electrode compatibility. E7018, for example, performs optimally on DC, although some varieties are AC compatible.
4. Welding Conditions Consider environmental factors such as wind exposure and the potential for moisture. Some rods perform better in windy or damp conditions, maintaining weld integrity, such as E6010, known for its adaptability in outdoor welding by producing a stable arc even under less favorable conditions.
welding rod selection chart
Experienced Insights into Effective Rod Selection
Welding experts often stress the importance of testing and familiarity. Trying out a variety of rods under different conditions helps to understand their behaviors, such as bead appearance, ease of slag removal, and overall fit for the task. For instance, while E7018 is preferred for its smooth finish and easy clean-up, the skill required to maintain a stable arc might not suit beginners. In such cases, E6011 might offer better control, especially for less experienced welders needing more practice.
Authoritative Guidelines for Professional Projects
Professionals often rely on codified standards and manufacturer specifications for welding rod selection. Adhering to guidelines from organizations like the American Welding Society (AWS) ensures compliance with industry standards, guaranteeing both safety and quality. Designer charts provided by manufacturers also offer critical information, detailing not just the mechanical properties but also suggesting optimal uses and settings for each type of rod.
Building Trust through Consistency
Crucial to maintaining trust in welding practices is consistency and reliability in outcomes. This can be achieved by combining quality equipment with appropriate welding rods tailored to each project’s needs. A well-thought selection process reinforced by reliable equipment maximizes productivity and minimizes the risk of post-weld failures, solidifying the welder’s professional reputation.
In sum, welding rod selection is an intricate process benefitting from a blend of technical knowledge and practical experience. Utilizing a selection chart enhances decision-making, guiding through nuances of material compatibility, position variance, and environmental concerns. Proper selection not only optimizes performance but also underscores professionalism, ensuring a robust and lasting weld.