Understanding the tensile strength of 7018 welding rods is crucial for professionals in the welding industry, whether they are involved in construction, manufacturing, or any other field where joining metals is essential. The 7018 welding rod, also known as the low-hydrogen electrode, is famed for its versatility and strength, playing an integral role in delivering reliable and durable welds that can withstand significant stress and strain.

The number 7018 in the welding rod’s designation provides important information about its tensile strength and usability. The first two digits, 70, indicate that this electrode produces welds with a minimum tensile strength of 70,000 pounds per square inch (psi).
This level of tensile strength ensures that the weld can endure substantial pulling or stretching forces without failing. Such strength is particularly vital in applications like bridge construction, high-rise buildings, and pressure vessels, where safety and durability cannot be compromised.
Quality assurance in welding requires understanding both the material properties and the environmental conditions under which those materials perform best. The 7018 welding rod is designed to work with Direct Current Electrode Positive (DCEP), although it can also operate on Alternating Current (AC), offering versatility across various welding tasks. One of the critical aspects of the 7018 rod is its low-hydrogen coating, which is crucial in minimizing the risk of hydrogen-induced cracking, a common problem in ferrous metals. This feature not only enhances tensile strength but also ensures the structural integrity of the weld by reducing porosity and increasing resistance against galvanic corrosion.
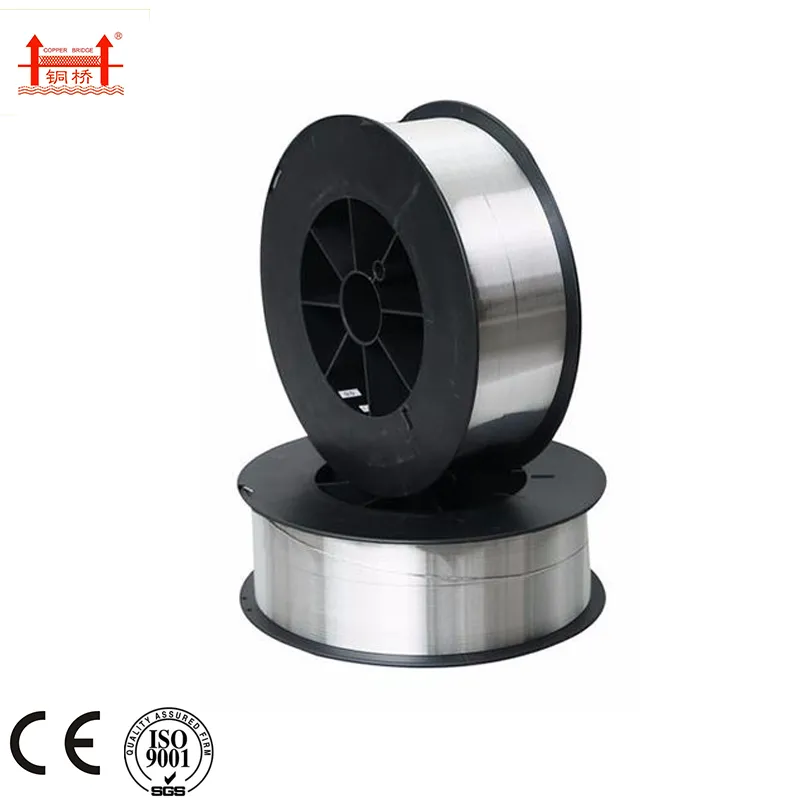
From an experiential perspective, seasoned welders often note that the 7018 rod provides a smooth arc and minimal spatter, making it user-friendly and efficient in complex welding scenarios. The electrode excels in situations demanding a clean and aesthetically pleasing weld bead, which explains its widespread use in fabrication settings that require both strength and appearance. Professionals appreciate not only the rod’s performance but also its adaptability to different working conditions. However, it's essential to store 7018 electrodes properly in a warm, dry environment and reconstitute them if exposed to moisture, to maintain their low-hydrogen properties and prevent weld defects.
tensile strength of 7018 welding rod
Expertise in welding involves selecting the right consumables—like the 7018 welding rod—tailored to specific tasks. Specialists in metallurgy and welding engineering advocate for a precise understanding of electrode classifications and material compatibility. The 7018 rod’s compatibility with a wide range of carbon steel materials makes it versatile. Moreover, the rod is known for its ability to weld in all positions—flat, horizontal, vertical, and overhead—making it an excellent choice for diverse and demanding projects.
Whether building robust infrastructure or delicate machine parts, ensuring the reliability of welds comes down to choosing the right electrode. The qualities of the 7018 welding rod underscore its authority in the field; when evaluated against industry standards, it consistently meets and exceeds expectations for tensile strength and performance. Such endorsement from both field experts and governing agencies strengthens its credibility.
To weld with confidence, professionals must trust their tools, and the 7018 welding rod delivers that trust through proven results and consistent performance. The data underpinning its tensile strength and operational capabilities highlight why it remains a favorite among welders. This rod not only supports structural loads with ease but also continues to be a tool of choice due to its predictable performance and adaptability to various welding challenges.
Choosing the 7018 welding rod means investing in a product that upholds the values of experience, expertise, authoritativeness, and trustworthiness in metallurgy and welding. Ultimately, understanding its tensile properties and best-use scenarios ensures that each weld is not only strong and durable but safe and dependable. This knowledge empowers welders, engineers, and constructors to realize projects that stand the test of time, ensuring both safety and efficiency in every weld performed.