The E6013 welding rod, a staple in the arsenal of welding professionals, presents a unique combination of reliability, versatility, and ease of use. It stands out in the welding industry due to its unique composition and application potential, catering to both seasoned experts and hobbyists.
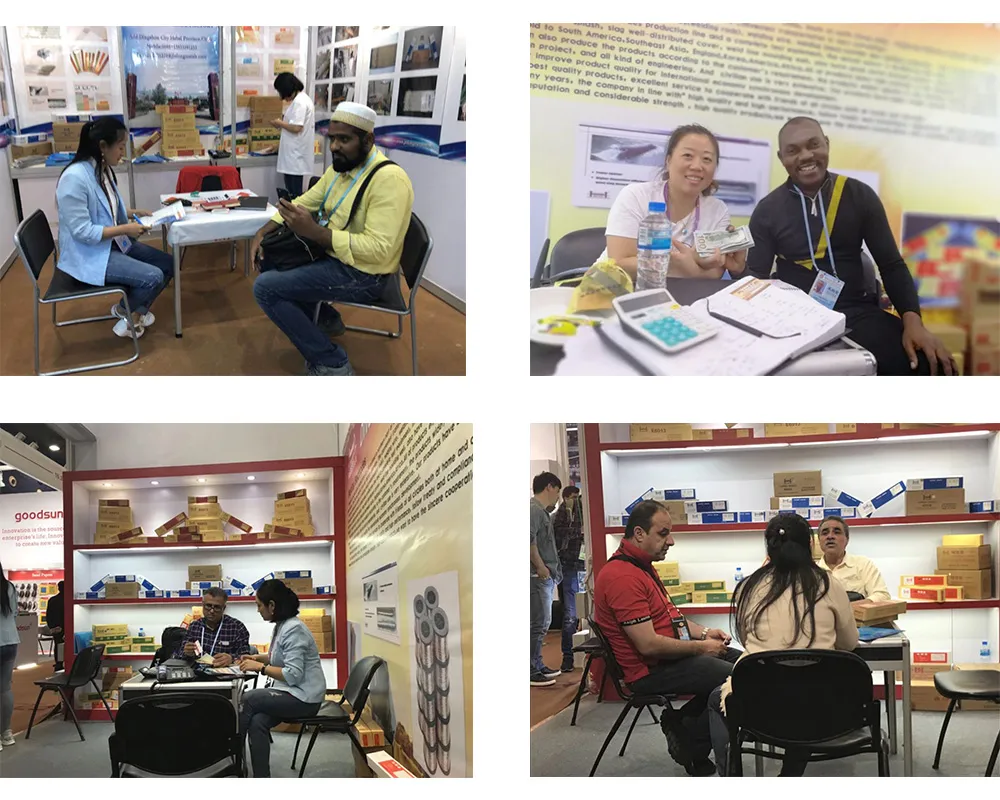
E6013 electrodes are renowned for their exceptional welder-friendly characteristics. These electrodes are designed to produce a stable arc, smooth action, and minimal spatter, which makes them particularly accessible for beginners while still providing precise control for skilled professionals. As a result, it is the preferred choice in educational and light industrial settings, providing a forgiving welding experience that encourages skill development.
A fundamental advantage of E6013 welding rods is their ability to adapt to a variety of welding environments. Their versatility is evident in their all-position welding capability, meaning they can be used on flat, horizontal, vertical, and overhead surfaces with ease. This adaptability ensures that E6013 rods are effective across diverse scenarios, from large-scale manufacturing projects to smaller, intricate tasks. The rods perform exceptionally well with AC or DC current and are compatible with electrodes of varying power supplies, enhancing their universal applicability.
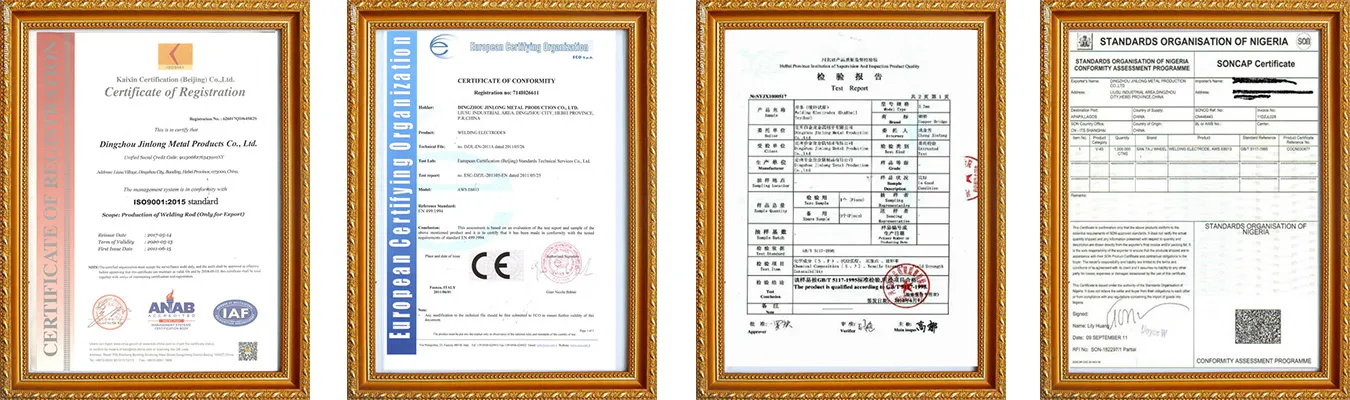
The electrode efficiency of the E6013 is another noteworthy feature. When fused, these rods generate a significant amount of slag, which, while needing to be chipped off after cooling, significantly protects the molten weld as it cools. This slag formation contributes to cleaner welding outcomes, reducing post-welding cleanup efforts and improving overall productivity. Such efficiency is invaluable in commercial applications, where time and cleanliness translate directly into profitability and aesthetic appeal.
In the context of material compatibility, E6013 welding rods are particularly effective on thin sheets of metal, such as mild and low alloy steels. They provide a soft arc with minimal penetration, ideal for applications requiring a delicate touch to prevent burn-through, which is a common challenge in welding thin metals. This makes them ideal for automotive repairs, agricultural machinery maintenance, and even artistic metalwork, where precision and material conservation are paramount.
e6013 welding rod uses
The distinct composition of E6013 rods contributes to their consistent and reliable performance. The electrodes comprise a mild steel core coated with a high titania potassium covering, which is responsible for their excellent arc behavior and deposition properties. The coating stabilizes the arc, reduces spattering, and assists in the generation of a visually pleasing, uniform bead appearance. This chemical makeup not only ensures strong joint integrity but also enhances weld aesthetics, an essential factor in visible or decorative applications.
Experienced welders value E6013 rods for their forgiving nature during use, which accommodates a variety of welding speeds and conditions. This tolerance allows welders to adapt the welding process to suit specific project requirements without compromising quality. Professionals often leverage these features in on-site repairs and installations, where variable conditions and stressed deadlines demand both flexibility and reliability.
Trust in the E6013 welding rod is bolstered by its long-standing reliability and universal acceptance among welding professionals. It is a rod that has stood the test of time, continuously favored in industries from construction to home improvement. Its widespread use is testament to its effectiveness, driving confident welding practices that produce steadfast results.
In conclusion, E6013 welding rods offer a comprehensive solution to both novice and experienced welders. Their adaptability, efficiency, and superior arc qualities make them a cornerstone product in diverse welding applications. Whether beautifying sculptures or securing critical connections in machinery, the E6013 remains a trusted tool, bridging the gap between capability and reliability, and reinforcing its position as an indispensable resource in the world of welding.