The term e 316L 16 might sound esoteric to the uninitiated, yet it is a beacon of quality and reliability in specialized industrial applications. E 316L 16 is a classification of welding electrode designed for the fusion and joining of 316L stainless steel materials. Understanding the unique features and applications of this electrode can significantly enhance one's expertise in fields requiring precise welding specifications.
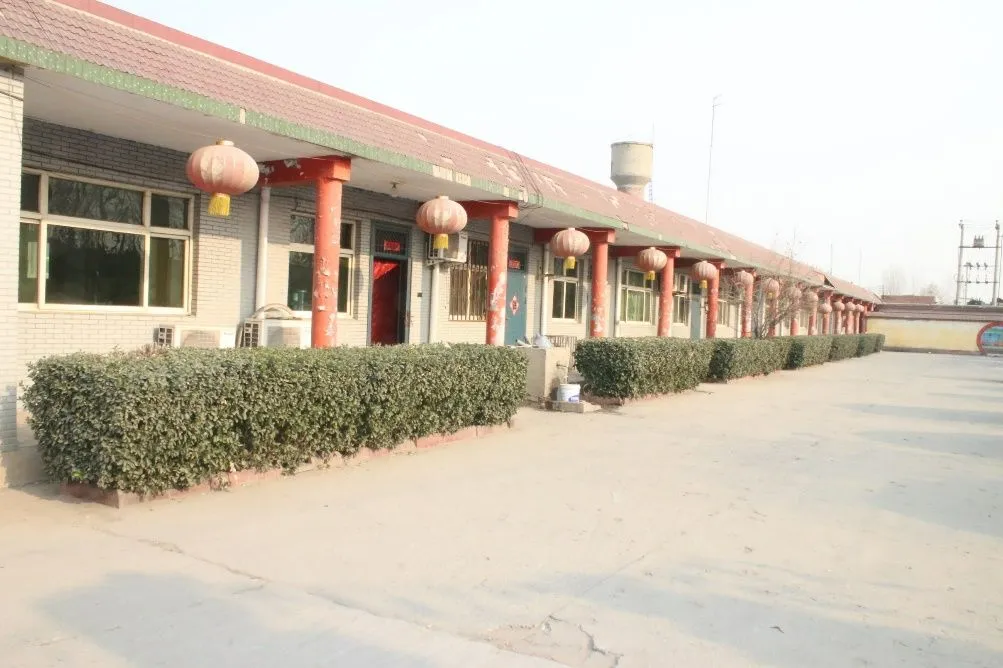
316L stainless steel is celebrated for its exceptional corrosion resistance and strength at elevated temperatures, making it the material of choice in industries ranging from chemical processing to food preparation. The L signifies the low carbon content which confers superior resistance to sensitization during welding, a critical factor that prevents intergranular corrosion. When such metals require joining, E 316L 16 electrodes prove critical by ensuring the welds maintain these key properties.
Any experienced welder will attest to the challenges posed by 316L stainless steel. Using general-purpose electrodes could lead to welds that are prone to cracking, corrosion, and structural failure under stress. E 316L 16 electrodes, however, provide seamless integration with the parent metal. They are formulated with chromium, nickel, and molybdenum, contributing to welds that mirror the base metal's resistance to acidic environments and mechanical stability.
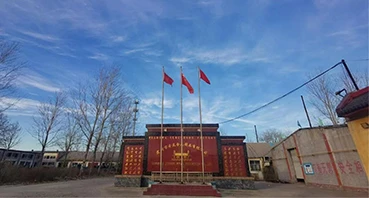
From an expertise perspective, welders recognize the importance of these electrodes in maintaining the structural integrity and aesthetic quality of stainless steel projects. The E 316L 16 electrode is engineered to produce a stable arc and minimal spatter – factors that reduce slag inclusions and post-weld cleaning time, thus improving workplace efficiency. This characteristic is essential when conducting large-scale industrial welds, where the precision and repetition of uniform welds are non-negotiable.
Trustworthiness is vital in welding processes, especially in industries where human safety and environmental risks are at stake.
One common sector that relies on the durability of E 316L 16 is the pharmaceutics industry. Tanks, valves, and pipework in this domain must adhere to the highest sanitary standards; welding imperfections can prove catastrophic. The E 316L 16 guarantees that the welds will perform without compromise in sterility-sensitive environments.
e 316l 16
Furthermore, the authoritativeness of E 316L 16 can be seen at educational levels, where leading technical institutions include this specific electrode in advanced welding modules. It illustrates quality assurance through compliance with stringent manufacturing codes, such as those set by the American Welding Society (AWS). These certifications reinforce the material’s authority and suitability for high-stakes projects and offer peace of mind to procurement specialists and project managers choosing materials for their tasks.
Incorporating real-world experiences from seasoned professionals provides an additional layer of credibility to the effectiveness of E 316L 16. Welders with decades of hands-on experience often advocate for this electrode based on its performance in intense operational environments – such as offshore platforms and chemical refineries. They often cite its reliability and adaptability in dealing with the nuances of different welding positions, from flat to overhead, which showcases its versatility.
Moving forward, those involved in procurement, design, or implementation of welding projects should contemplate factors like cost-efficiency, project timelines, and specific environmental conditions. E 316L 16 electrodes stand out as an investment not just in monetary terms, but in quality, resilience, and long-term structural soundness.
The effectiveness of E 316L 16 brands can vary, so due diligence is recommended when selecting manufacturers to ensure alignment with project specifications. Ultimately, those committed to excellence in their welding endeavors would be remiss to overlook the unique benefits that E 316L 16 electrodes bring to both construction and repair of stainless steel assemblies. As industries continue to expand and evolve, incorporating cutting-edge materials like E 316L 16 will remain a cornerstone of quality and operational success.