In the world of welding, the 7018 welding rod is revered for its remarkable versatility and efficiency. This particular electrode is indispensable for professionals seeking strength, reliability, and precision. Understanding its diverse applications and the science behind it is crucial for maximizing its potential in various industries.
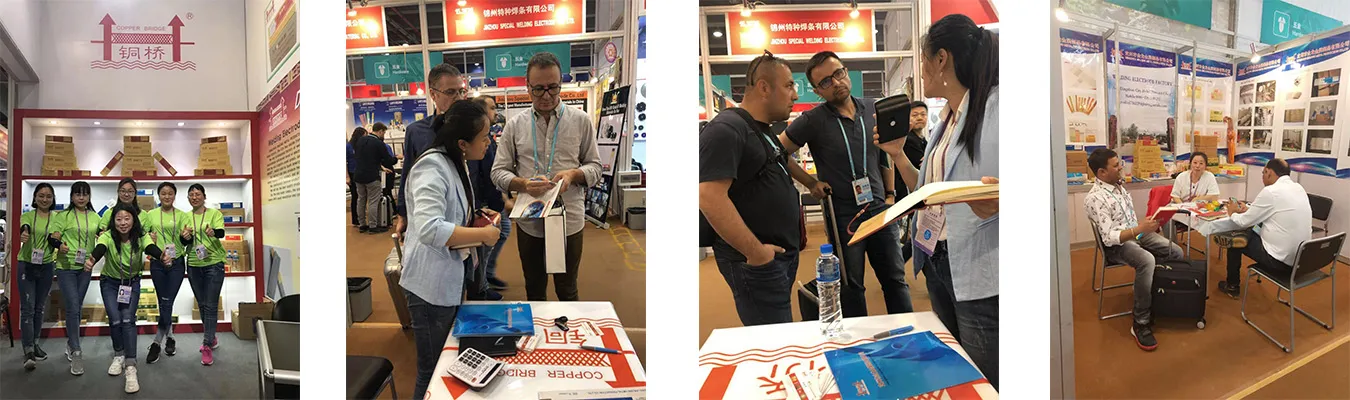
The 7018 welding rod, classified under the AWS (American Welding Society) system, is an all-position, low-hydrogen rod commonly used in structural welding projects. Its flux is designed to produce a smooth arc, minimal spatter, and easy slag removal, which enhances the aesthetics and quality of the weld. But its benefits extend far beyond the welding process itself; they significantly impact the longevity and integrity of the welded structure.
One of the primary applications of the 7018 welding rod is in the construction of bridges, buildings, and other infrastructure projects. Its low-hydrogen nature minimizes the risk of cracking, a critical concern in structural applications where the integrity of a weld can affect the safety of an entire structure. The rod's high tensile strength (typically around 70,000 psi) ensures that it can withstand significant stress, making it ideal for load-bearing applications.
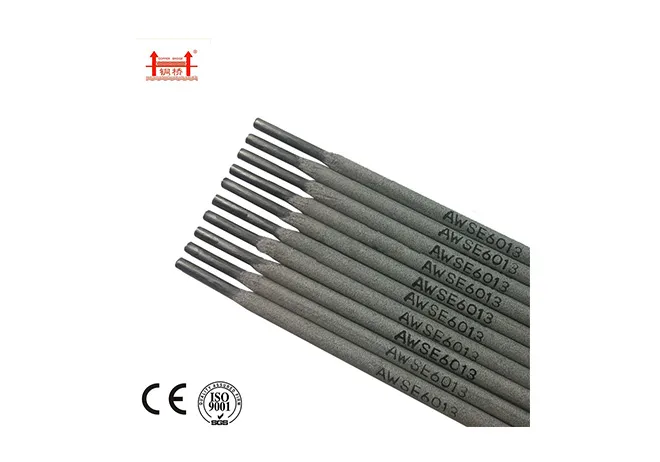
Furthermore, the 7018 welding rod is extensively used in the shipbuilding industry. The marine environment presents unique challenges, including exposure to high moisture and saline conditions that can lead to corrosion. The low-hydrogen characteristic of the 7018 helps mitigate these concerns, ensuring longer-lasting welds that can endure harsh conditions.
In the realm of automotive repair and fabrication, the 7018 welding rod proves invaluable. The rod’s ability to produce strong and clean welds makes it suitable for repairing frames and constructing custom vehicle parts. Given that automotive components often experience dynamic loads and vibrations, the durability offered by the 7018 rod is a distinct advantage.
7018 welding rod applications
Moreover, the petrochemical industry finds the 7018 welding rod indispensable. With the industry's critical emphasis on safety and reliability, the rod's consistency in producing high-quality, defect-free welds meets the stringent standards required for pipes and tanks carrying volatile substances. Low sulfur content in the rod’s coating ensures that there are minimal chemical reactions that could lead to compromised weld integrity.
The expertise of professionals using the 7018 welding rod is crucial, as improper handling can negate its benefits. Preheating the base material in certain conditions and maintaining a dry storage environment for the rods are essential practices to prevent issues such as porosity or hydrogen-induced cracking. Such precautions underline the necessity of combining the right equipment with expert knowledge.
Authoritative endorsements from welding institutes and documented case studies further underscore the trustworthiness of the 7018 welding rod. Institutions like the American Welding Society provide comprehensive guidelines that reinforce its reliability, ensuring that users can confidently apply it across varying scenarios.
For anyone involved in serious welding applications, the 7018 welding rod is an eminent choice, supported by its robust properties and diverse usability. Its proven track record in numerous demanding environments cements its status as a go-to electrode in the professional welding community. Through leveraging its full potential, industries can enhance not only the strength and longevity of their projects but also refine the craft of welding to an art form.