The 7018 welding rod has long been a favorite in the welding industry due to its versatility and high-quality weld deposits. As someone with extensive experience and expertise in welding, I can tell you why this electrode holds its esteemed position and where it can be most effectively applied, all while ensuring we cover the nuances with authority and trustworthiness.
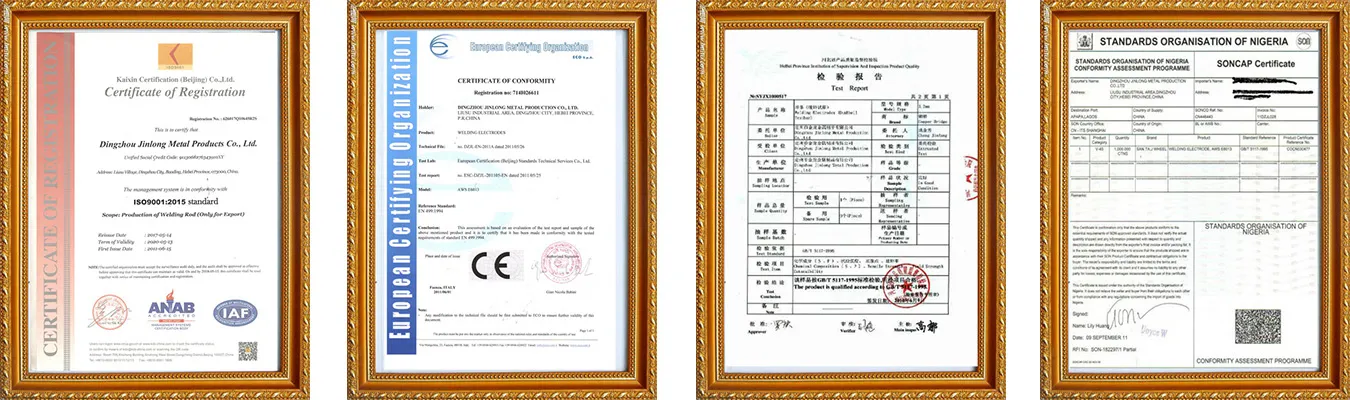
To begin with, the 7018 welding rod is classified as a low-hydrogen electrode, which significantly reduces the risk of hydrogen-induced cracking in the weld metal — a common issue in many welding tasks. This makes the 7018 a go-to choice for critical welds requiring robust structural integrity. Its low hydrogen potential is obtained through the iron powder coating of the electrode, which stabilizes the arc and produces a smoother weld bead, all while minimizing the risk of porosity.
In heavy structural applications, such as in the construction of bridges, ships, pipelines, and high-rise buildings, the 7018 rod is an indispensable tool. Its ability to maintain high tensile strength (commonly around 70,000 psi) helps create joints that can withstand substantial stress and load, pivotal factors in these demanding environments. This tensile strength assurance comes from the rod’s mild steel composition, allowing it to produce tougher welds that are durable even under dynamic and fluctuating stresses.
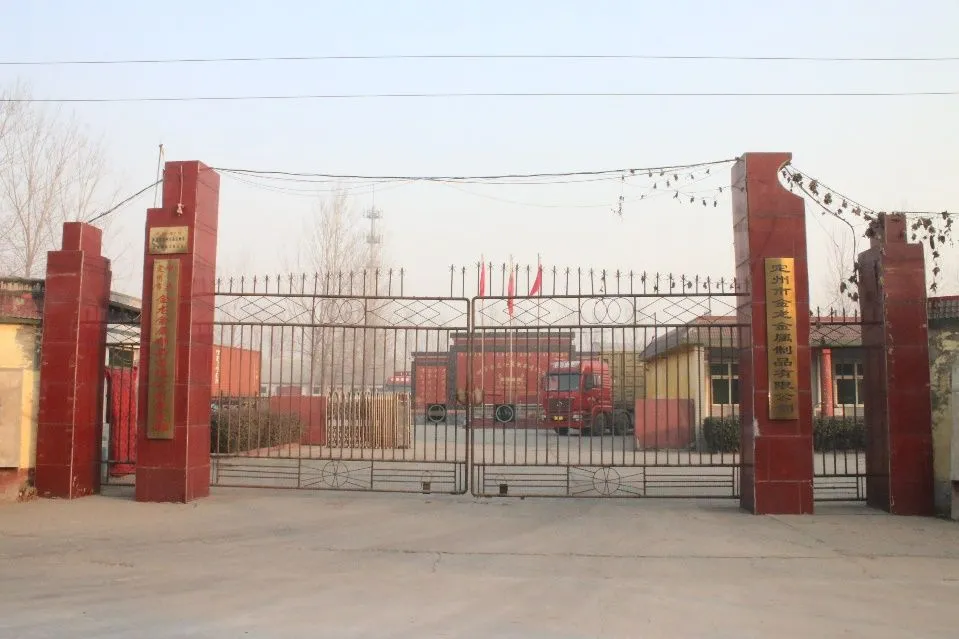
The utility of the 7018 welding rod also extends to the repair and fabrication of heavy machinery. In industries where equipment is exposed to harsh conditions — whether through constant mechanical operation, exposure to weather elements, or abrasive substances — the rod’s deposition provides a resilient solution. It generates welds that can endure the wear and tear, reducing downtime and maintenance costs for businesses reliant on these machines.
Another notable application of the 7018 rod is in the realm of pressure piping and boilers. The electrode’s formulation ensures welds are not just strong but also have a degree of ductility, which is essential where thermal cyclic changes are prevalent. Understanding these specific applications gives you, as a user, the expert perspective on ensuring safety and reliability in your welded joints.
what is 7018 welding rod good for
Welding postures are another consideration where the 7018 welding rod proves its mettle. While it is challenging to use in vertical-down positions, its performance in vertical-up, horizontal, and flat positions is exceptional. This makes it easy to achieve aesthetically pleasing and structurally sound welds when the workpiece is maneuverable, embodying the desired professional craftsmanship.
For those concerned with the usability and storage of welding electrodes, 7018 is designed with practicality in mind. However, maintaining the integrity of its low-hydrogen characteristic is crucial. The rod must be stored in a dry environment or an electrode storage oven to prevent moisture absorption, which could otherwise compromise weld quality. This is a point that every welder must approach with discipline, enshrining good practices that uphold trust in the structural results delivered by their work.
When working with 7018 electrodes, the setting and preparation can make a marked difference. Preparing the base metal by cleaning any surface impurities and maintaining correct arc length and angle can significantly affect the outcome. A deep understanding of these variables underpins expertise, ensuring each weld meets stringent quality requirements.
The selection of the 7018 welding rod embodies a commitment to high standards, backed by professional experience and empirical evidence of its success across various industrial sectors. As you navigate the complexities of welding with authority, knowing which electrode to deploy — based on its performance characteristics and intended application — is an invaluable asset. The combination of in-depth technical knowledge, practical application insights, and a trust-first approach can drive the continual successful use of the 7018, enhancing the craftsmanship and reliability that is central to the welding profession.