When joining cast iron to mild steel, many welders face a unique set of challenges due to the distinct properties of each material. Cast iron's brittle nature and carbon content differ significantly from the more malleable and less carbon-heavy mild steel. Choosing the correct welding rod is crucial for a successful and durable weld.
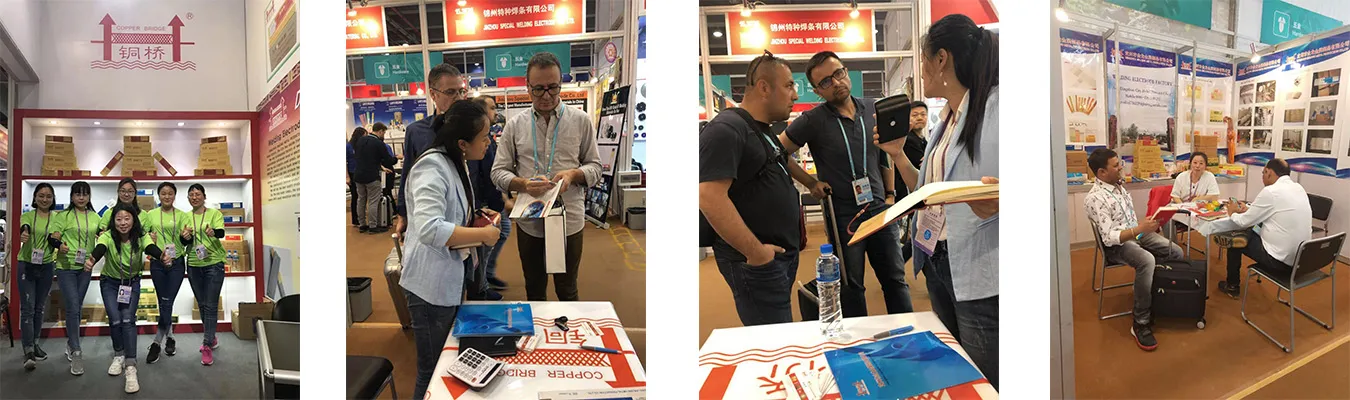
Experience has shown that nickel-based welding rods are often the best choice for this task. Nickel has properties that accommodate the differences in expansion and contraction rates of cast iron and mild steel. Through hands-on projects, welders have witnessed that a high-nickel rod, such as ENiFe-CI, provides a sound fusion with both metals. Its versatility and adaptability to thermal cycling make it a preferred choice. This rod not only facilitates effective bonding but also adapts to the inherent brittleness of cast iron, minimizing the likelihood of future cracking.
Expertise in metallurgy reveals that the welding process's success is not solely dependent on the rod but also on the preparation and technique applied.
Preheating the cast iron is a critical step. In practice, it has been found that slowly raising the temperature of the cast iron to approximately 500°F helps reduce thermal shock during welding. Once welded, allowing the components to cool gradually further aids in minimizing stress and potential cracking. Experts recommend peening the weld bead to relieve stress, thus enhancing the weld's integrity.
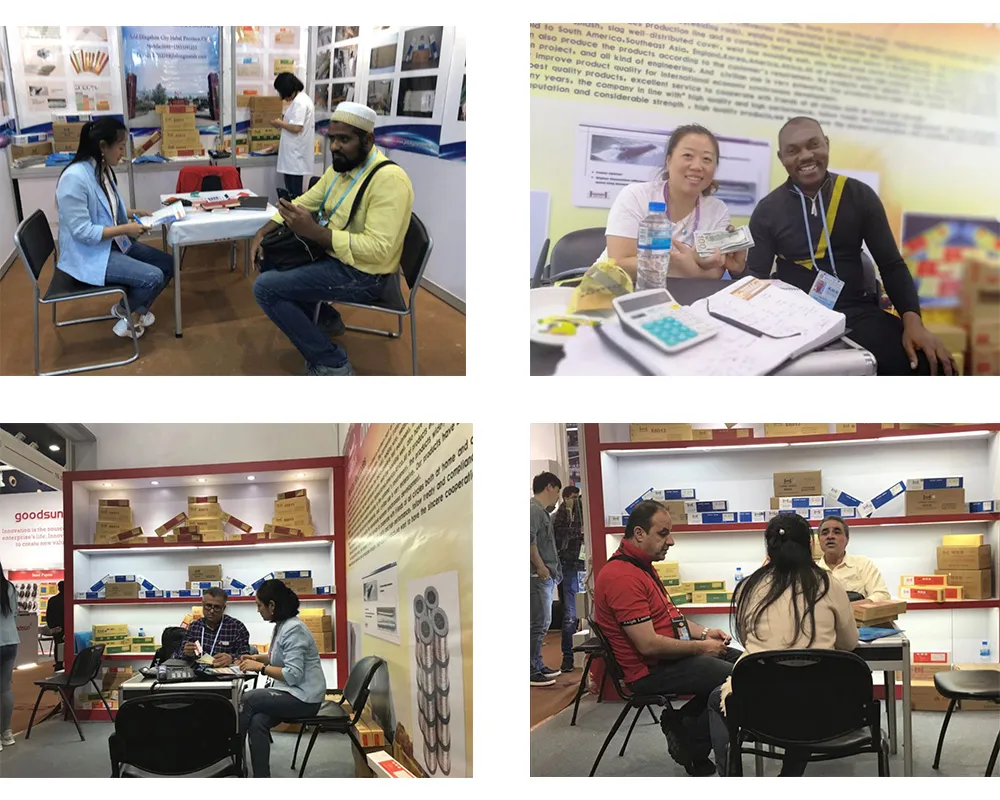
welding rod for cast iron to mild steel
In exploring the authoritative perspectives within welding communities, journals, and professional metalworking resources, the emphasis frequently returns to the compatibility of the filler material with both the cast iron and mild steel. Ni-rod 55 and Ni-rod 99, which contain about 55% and 99% nickel respectively, have emerged as authoritative choices. These rods are well-documented for their efficacy in such applications. Their high nickel content significantly compensates for the carbon disparity, ensuring that the weld is strong and reliable. The user feedback on these products consistently points to their exceptional performance, garnering trust across professional domains.
Trustworthiness in welding rods comes from consistent quality and predictable outcomes. These come from reputable manufacturers with a history of excellence in producing electrodes that meet industry standards. Such trust is essential, especially in critical applications involving cast iron, which when fractured, can lead to costly repairs or hazardous failures. For welders looking to purchase welding rods, recommendations often include researching product certifications and reviews from credible sources to ensure a reliable purchase that lives up to its claims.
In conclusion, welding rods for connecting cast iron to mild steel require careful selection and consideration of metallurgical factors. Through empirical experience, proven expertise, and reliable sources of authority, welders can achieve optimal results. The focus is always on minimizing the inherent risks associated with these distinct metals, leveraging high-quality, nickel-based rods, and adhering to recommended procedures like preheating and managed cooling. Such strategies not only ensure a strong bond but also extend the service life of the welded assembly, ultimately leading to successful projects and satisfied clients.