Nickel welding on cast iron is a topic that demands not only technical expertise but also a deep understanding of material properties and the intricacies of welding methods. For professionals seeking to optimize the performance and longevity of cast iron repairs, nickel welding offers a robust solution. This article delves into the unique challenges and advantages of using nickel electrodes in cast iron welding, ensuring reliable outcomes in industrial applications.
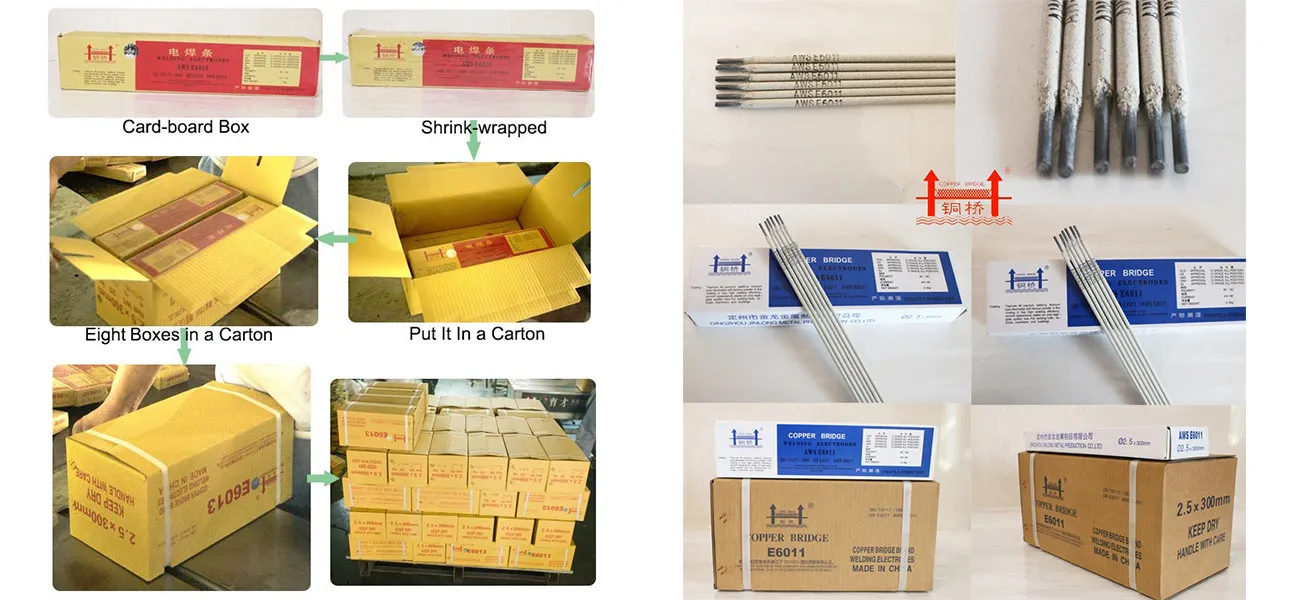
Cast iron, characterized by its high carbon content, presents certain challenges when it comes to welding. Its brittle nature, coupled with varying compositions, demands a welding approach that accommodates these properties, minimizing the risk of cracking. Nickel, renowned for its ductility and strength, emerges as an ideal filler material for welding cast iron, primarily due to its compatibility with the heterogeneous microstructure of cast iron.
A primary advantage of using nickel welding consumables is their ability to reduce residual stresses formed during the cooling process. Nickel's low thermal expansion coefficient ensures that as a welded part cools,
it contracts at a similar rate to cast iron. This compatibility minimizes stress concentrations and prevents crack formation, a common pitfall when attempting to weld cast iron with less suitable materials.
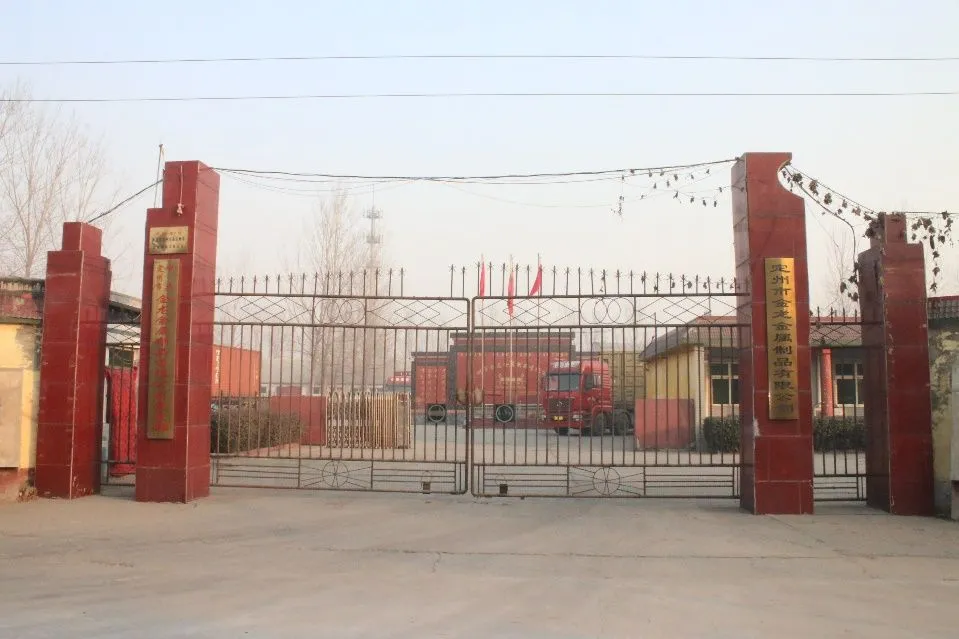
In terms of process, nickel welding of cast iron can be performed using various methods, such as shielded metal arc welding (SMAW), gas metal arc welding (GMAW), and flux-cored arc welding (FCAW). Among these, SMAW, frequently employed with nickel-based electrodes, offers advantages in terms of versatility and accessibility. For critical applications, however, GMAW can provide higher control over the welding parameters, ensuring precision and consistency.
nickel welding cast iron
Preparation is paramount in nickel welding cast iron. Prior to welding, the area to be repaired must be thoroughly cleaned to remove any oils, paint, or rust, which could interfere with the welding process. Preheating the cast iron component is also recommended, especially in cases where the material is particularly thick. A gradual, even preheat helps to alleviate thermal shock, further mitigating the risk of post-weld cracking.
Furthermore, choosing the right nickel alloy is essential. Pure nickel electrodes are suitable for most general-purpose repairs, but for applications requiring enhanced machinability or added corrosion resistance, nickel-iron or nickel-copper alloys may be preferable. The choice of alloy can significantly influence the mechanical properties and performance of the repaired cast iron component.
Post-weld heat treatment is another critical factor in the success of nickel welding cast iron. A slow, controlled cooling process allows the weld and surrounding material to relieve internal stresses naturally. By allowing the component to return to ambient temperature gradually, the risk of stress-induced cracking is considerably reduced.
In conclusion, nickel welding cast iron is a technique that, when executed with precision and understanding, results in durable, long-lasting repairs. The expertise in selecting appropriate nickel alloys, coupled with meticulous preparation and post-weld heat treatment, underscores the importance of handling this process with the utmost care. For industries reliant on the integrity of cast iron components, integrating nickel welding as a standard practice not only extends the service life of machinery but also solidifies trust in repair efficacy.