Electrode wire welding is a pivotal technique in the modern manufacturing landscape, offering precise and efficient solutions for joining metals and alloys. As industries constantly evolve, the integration of electrode wire welding in production lines has become indispensable, and understanding its nuances ensures optimal results and heightened productivity.
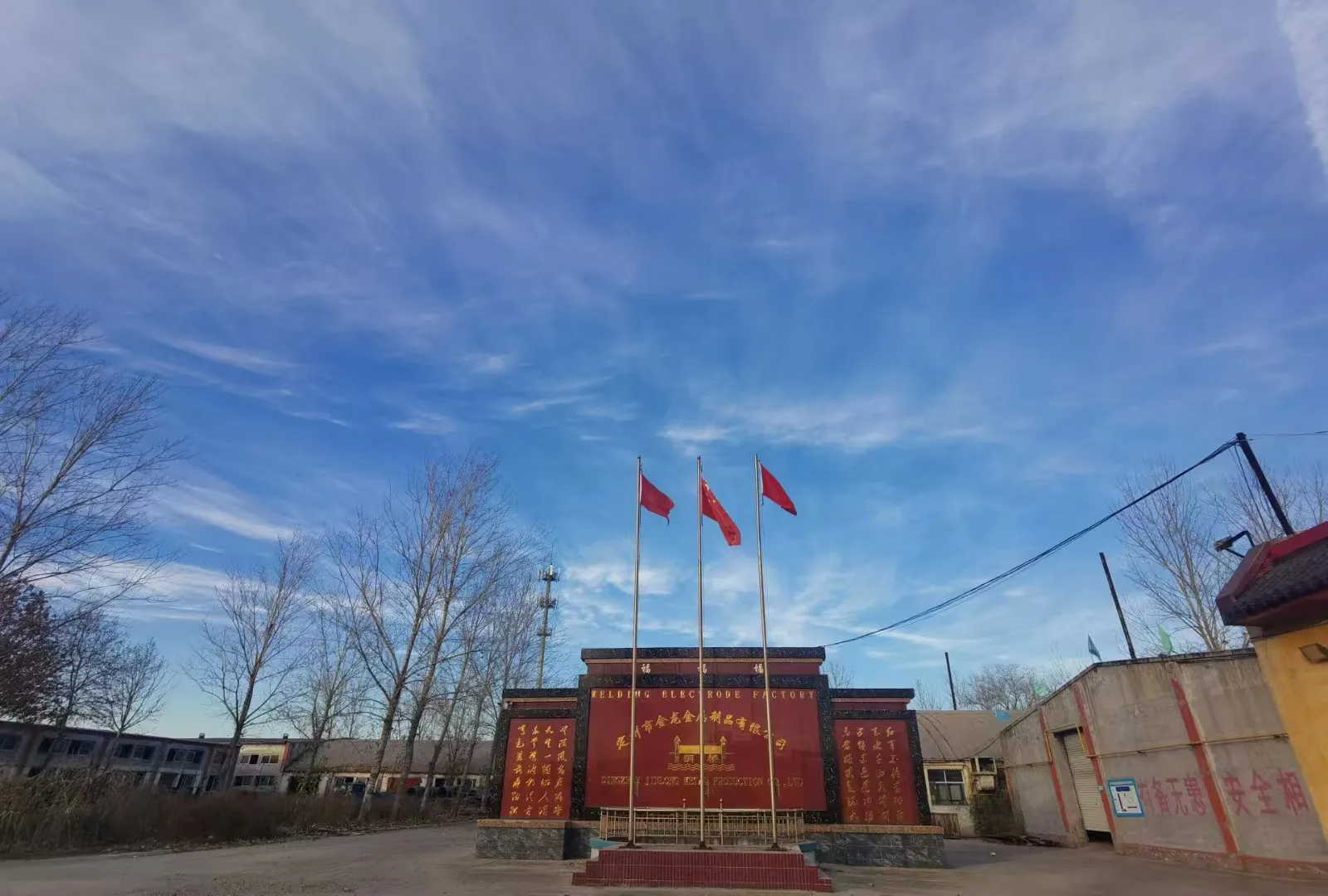
Experience is a cornerstone in mastering electrode wire welding. Seasoned welders appreciate the subtleties that come with years of practice—such as the feel of the electrode wire feeding through the machine or the precise angle necessary to maintain a steady arc. For instance, expert welders discern the sound and sight of the arc, adjusting parameters in real-time to accommodate nuances in material thickness or composition. This experiential knowledge translates into welds that are strong, durable, and visually appealing.
The expertise required in electrode wire welding transcends basic operational know-how. It involves an in-depth understanding of metallurgical concepts, such as the heat-affected zone (HAZ), and how different materials react to welding temperatures. Welders with expertise know how to mitigate potential issues like warping or weakening of the base material. They can choose the appropriate electrode wire type and diameter based on the specific requirements of a job, optimizing for both structural integrity and aesthetics.
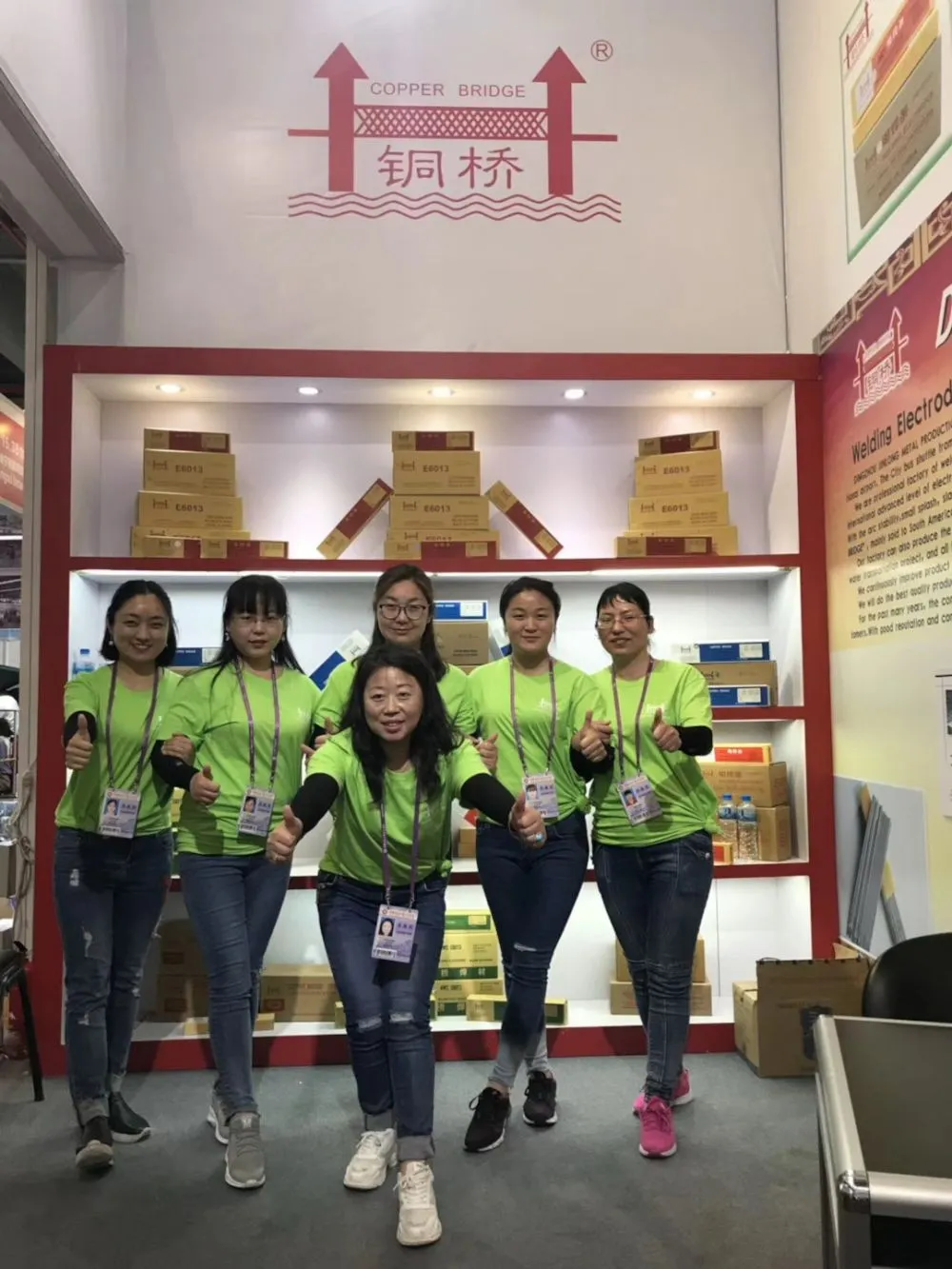
Authoritativeness in electrode wire welding is characterized by adherence to standards and protocols. Actively participating in continuous education and certification processes, authoritative figures in the welding industry ensure that they are abreast of the latest technological advancements and safety regulations. In addition, they contribute to knowledge dissemination by publishing in reputable journals and presenting at technical conferences. Their insights shape industry standards and practices, making their endorsement of methods or tools highly valuable.
electrode wire welding
Trustworthiness is non-negotiable in electrode wire welding. The reliability of welds can significantly impact the safety and functionality of the final product, particularly in critical applications such as automotive, aerospace, or infrastructure. Establishing trust involves rigorous testing and validation of welding techniques to ensure compliance with stringent quality control measures. Welders and companies dedicated to trustworthiness often employ third-party verification for their processes, instilling confidence in clients and stakeholders about the consistency and reliability of their welds.
In product development, the choice of electrode wire can significantly impact production efficiency and cost-effectiveness. Developers must consider factors such as melting rate, deposition efficiency, and ease of handling when selecting electrode wire.
High-quality electrode wires yield fewer welding defects, reducing waste and rework time, while ensuring robust and high-strength welds. Manufacturers who provide comprehensive product specifications and are transparent about the performance characteristics of their electrode wires further enhance consumer trust and satisfaction.
In conclusion, the domain of electrode wire welding is rich with opportunities for mastery and innovation. By focusing on experience, expertise, authoritativeness, and trustworthiness, professionals in this field can dramatically improve the quality and efficiency of their welds. Each weld not only represents technical skill but also the culmination of experience and knowledge, creating stronger, more durable, and aesthetically pleasing metal structures.