The E316L electrode, a vital component in stainless steel welding, is highly regarded for its remarkable performance and reliability. Understanding its specification is critical for professionals looking to optimize their welding projects, ensuring longevity and structural integrity.
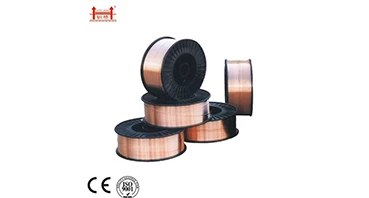
The E316L electrode is designed specifically for welding 316L stainless steel materials, presenting an excellent choice when corrosion resistance is paramount. It contains low carbon levels, typically less than 0.03%, which reduces the risk of carbide precipitation during welding. This crucial feature makes the electrode ideal for applications where temperatures range between 500 to 800 degrees Celsius, such as in the chemical and petrochemical industries.
A standout aspect of the E316L electrode is its inclusion of molybdenum, an alloying element that enhances its resistance to pitting and crevice corrosion. These characteristics are essential for environments with high chloride exposure, such as in marine applications and in the construction of chemical processing equipment. Molybdenum fortifies the electrode, providing additional protection against harmful chemical reactions.
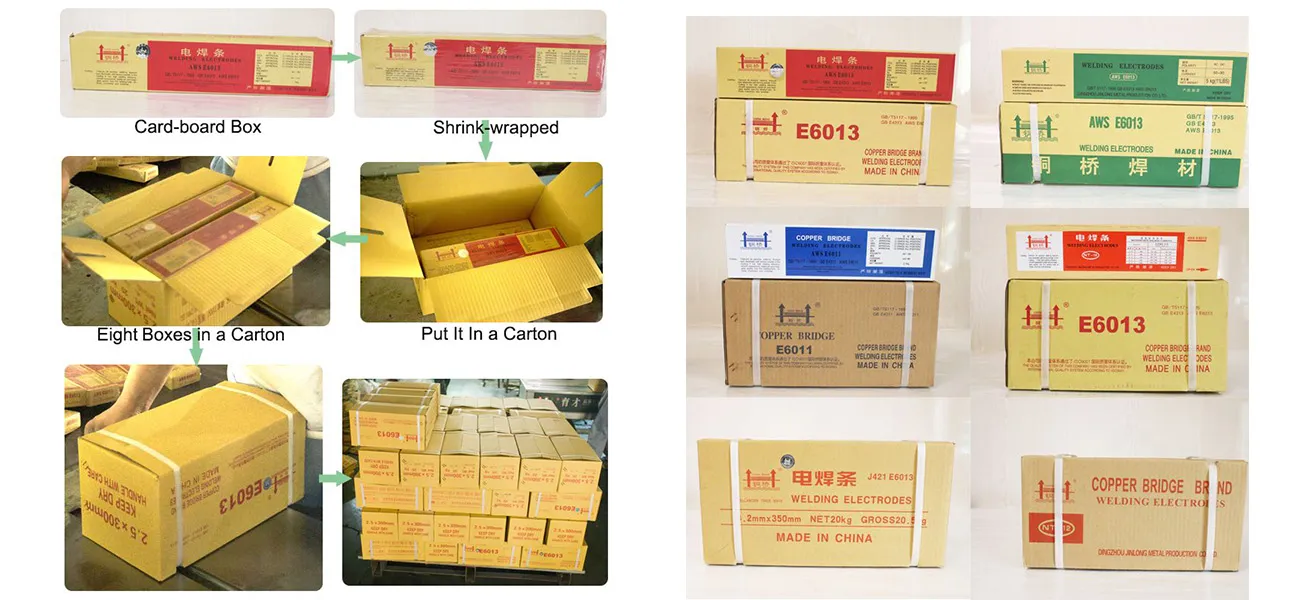
The E316L electrode also exhibits low spatter levels and stable arc properties, which significantly contribute to improved work efficiency and a cleaner welding environment. This stability ensures smooth bead appearance, an important aesthetic and functional requirement in many industrial applications. Such seamless application not only reinforces joint areas but also minimizes the necessity for excessive cleanup or post-weld machining, thereby conserving time and resources.
Expertly engineered to produce austenitic stainless steel weld deposits, the E316L maintains its structure under thermal expansion, providing robust resistance against thermal-induced stress or cracking. This structural integrity is beneficial in ensuring leak-proof joins in piping systems and vessels that transport gasses or fluids under varying pressure conditions.
e316l electrode specification
The electrode's welding positions, including flat, horizontal, vertical, and overhead, enhance its versatility. This flexibility accommodates the diverse demands of welding projects, ensuring the E316L electrode can be applied efficiently across different industries without sacrificing quality or performance.
From an authoritative appearance in safety compliance, the E316L electrode conforms to international welding standards such as the American Welding Society (AWS) A5.
4 specifications. Adhering to these stringent guidelines guarantees that professionals can trust this electrode for critical welding processes in demanding environments.
Trustworthiness in welding is indelibly linked to product reliability. E316L electrodes are produced following robust quality controls and rigorous testing, ensuring each batch meets specified mechanical properties and chemical composition. This assurance of quality control fosters trust among engineers, welders, and construction managers, who depend on consistent performance for their projects' success.
In conclusion, the E316L electrode specification meets the high demands of modern welding requirements and remains a trusted choice for projects where lasting durability, excellent corrosion resistance, and reliable performance are essential. Its professional engineering, adherence to global standards, and proven track record make it a stalwart in the world of welding, serving as a testament to the advances in metallurgical production and quality assurance for industry specialists seeking trusted welding solutions.