In the ever-evolving world of welding technology, the transition from carbon steel (CS) to stainless steel (SS) showcases how innovation meets practicality. Selecting the correct welding electrode for joining CS to SS is crucial as it influences the integrity and longevity of the final weld.
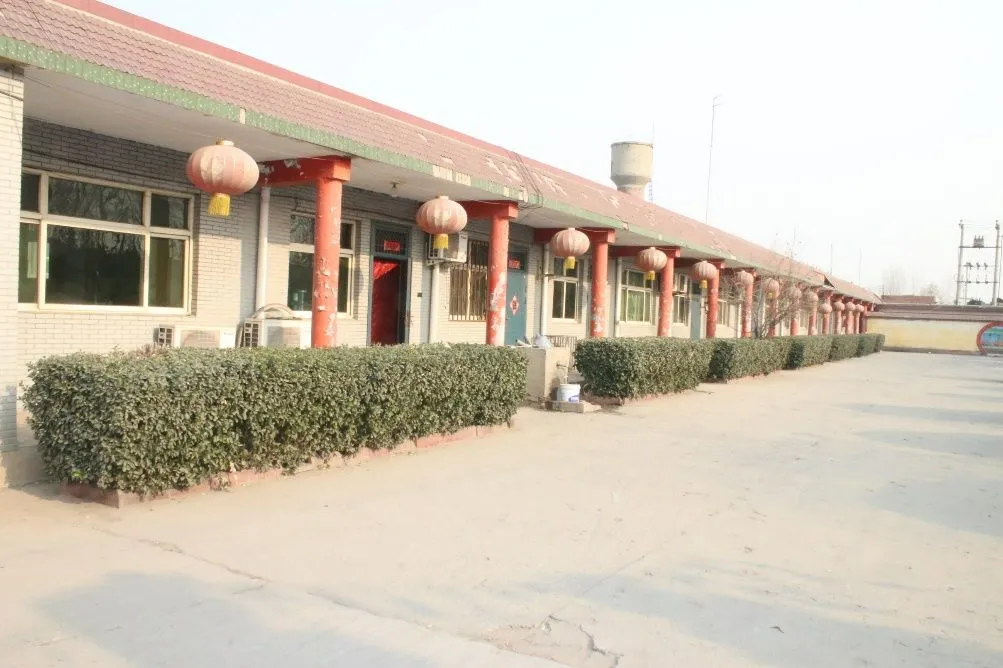
Welding between carbon steel and stainless steel involves joining dissimilar metals, which presents its unique set of challenges, such as differences in melting points, thermal expansion rates, and chemical compositions. This calls for precise expertise and professional guidance to ensure that the weld not only meets the structural requirements but also adheres to industry standards.
When it comes to electrode choice, using an electrode that matches the stainless steel component is often recommended.
For welding CS to SS, the E309L-16 electrode is frequently the go-to choice. This electrode offers a high level of resistance to corrosion and provides excellent strength and durability, which makes it ideal for hybrid metallic applications.
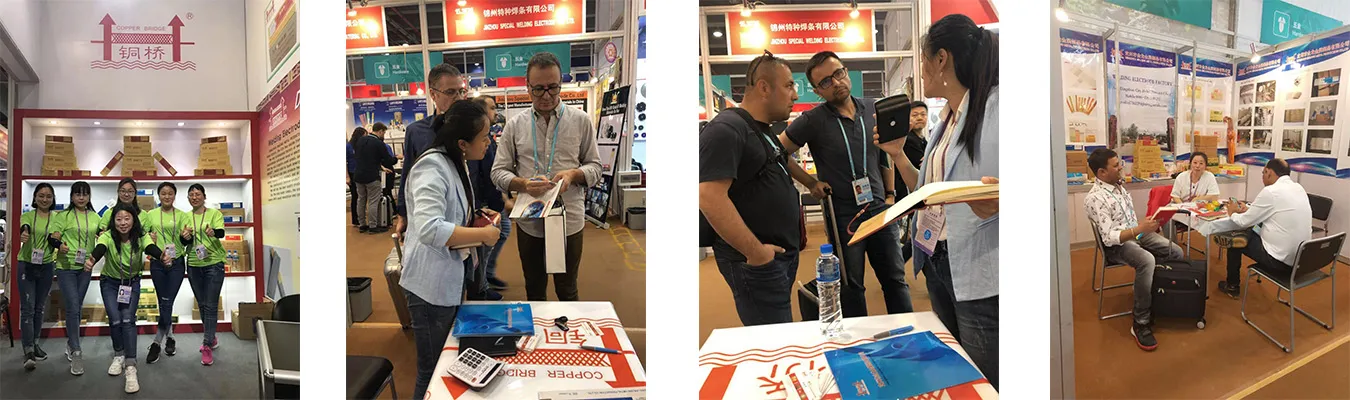
From a technical standpoint, the E309L-16 electrode is coated and contains alloys that help to mitigate the challenges of welding dissimilar metals. They achieve this by creating a buffer layer that prevents excessive carbon migration from the steel to the stainless steel, which can lead to carbide formation and eventual weld failure.
Experience in the field underscores the importance of preparation in the welding process. Surface preparation and cleanliness cannot be overstated. Removal of surface contaminants like rust, oil, or dirt ensures that the weld pool is pure and free from impurities, yielding a strong bond. Grinding or brushing the weld area can be beneficial in achieving the desired level of cleanliness.
Maintaining the correct welding technique, such as angle and speed, is another crucial factor. A standard procedure involves positioning the electrode at a consistent angle between 10 to 15 degrees from the vertical, which aids in achieving a consistent weld bead. Proper training in managing heat input and controlling interpass temperatures also plays a significant role in preventing distortion and ensuring the quality of the weld.
cs to ss welding electrode
Authoritativeness in choosing the right electrode is often supported by adhering to established welding standards specified by organizations like the American Welding Society (AWS) and the American Society of Mechanical Engineers (ASME). These standards not only outline the requisite mechanical properties of welds but also provide testing guidelines to ensure weld integrity.
Testing the weld is a final step that cannot be overlooked. Non-destructive testing (NDT) methods such as ultrasonic testing (UT) or radiographic testing (RT) are commonly employed to confirm the weld's quality without compromising its structural integrity. This step offers confidence in the weld's performance over its lifespan.
As a trusted advisor in welding technology, it's pertinent to stay informed on the latest advances, which include new electrode formulations and enhanced welding techniques that promise both improved efficiency and reduced operational cost. Continuous professional development, through workshops and certification programs, ensures that you remain an authoritative source in welding practices.
Navigating the challenges of CS to SS welding demands a high degree of trustworthiness from both the materials used and the skills applied. Ensuring consistency in supply chains for high-quality electrodes or consulting with certified welding experts can mitigate risks associated with weld failures.
In conclusion, welding electrodes play a pivotal role in ensuring the success of CS to SS welding. Only through a blend of carefully chosen materials, expert handling of tools and machinery, and thorough quality assurance methods can one achieve a successful, long-lasting weld. Trust, experience, and expertise remain the foundational pillars in the realm of welding technology. As the demand for hybrid metallic constructs grows, so does the need for authoritative guidance on the best practices in welding, ensuring structures that are safe, reliable, and capable of standing the test of time.