Choosing welding rods, particularly between the 6011 and 7018, hinges upon understanding their unique properties and use-cases within welding applications. Both rods have their distinctive qualities, making them suitable for specific tasks, material types, and conditions. This knowledge empowers welders, both novice and experienced, to make informed decisions, enhancing the quality and durability of their work.
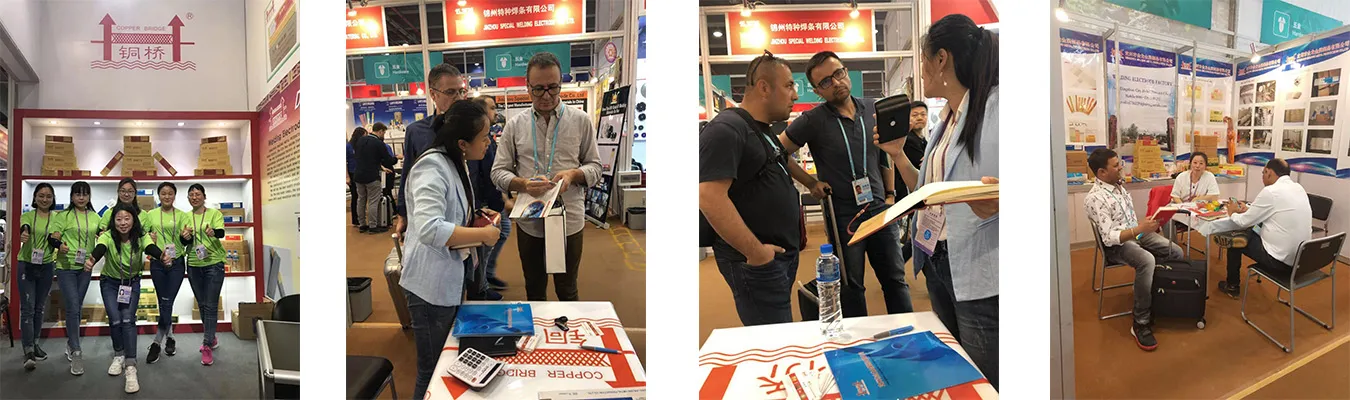
The 6011 welding rod stands out for its versatility and deep penetration capabilities. Often used where welding surface conditions are less than ideal, such as in repair welding and maintenance tasks, the 6011 excels thanks to its ability to work through paint, rust, and dirt without compromising weld quality. This rod is an AC/DC rod, making it flexible when working with different power sources and is particularly favored for its all-position welding abilities. This characteristic is crucial when conducting fieldwork on projects that involve varied and awkward angles, making the 6011 an invaluable tool for farm equipment repairs, fencing, and other worksite applications.
On the other hand, the 7018 rod is revered for its strength and smooth arc characteristics, suitable for projects demanding a high-quality finish on clean surfaces. The 7018 is often used in structural welding due to its low-hydrogen flux coating, enhancing its strength and preventing cracking, especially in structural applications. Its smooth, stable arc, and easy slag removal enhances aesthetically pleasing welds, favored in industries that prioritize visual inspection as part of quality control. Unlike the 6011, the 7018 is primarily a DC-positive electrode, which necessitates more attention to the electrical settings but offers superior mechanical properties in return. Welders in manufacturing, shipbuilding, and structural steel industries appreciate the 7018 for its ability to produce strong, ductile welds on particularly thick materials.
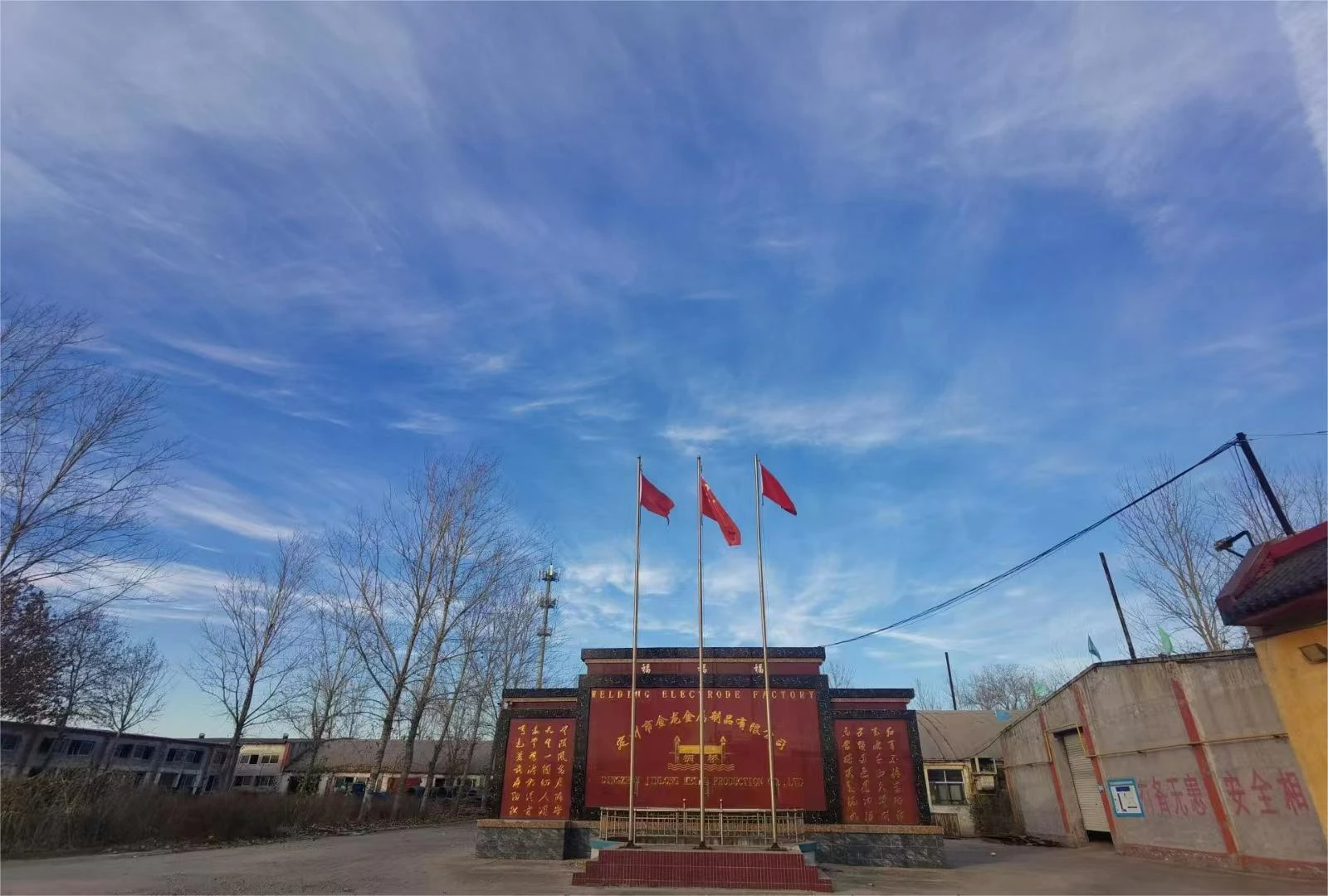
One of the main differences lies in the storage requirements. The 7018 rods demand careful storage to prevent moisture absorption, which could introduce hydrogen into the weld and lead to cracking. Therefore, these electrodes are often stored in an oven or a tightly sealed container. This aspect underscores the importance of handling and preparation, especially in projects where weld integrity is paramount. In contrast, the 6011 rods, due to their cellulose-based flux, are more forgiving and can be stored without these stringent conditions, allowing for more flexibility and ease of use, particularly in outdoor environments.
6011 vs 7018 rod
The choice between these rods significantly impacts welding performance and outcome. Novice welders often start with the 6011 due to its forgiving nature and minimal requirement for surface preparation. Meanwhile, the 7018 requires the welder to have a firm grasp of the material preparation and welding technique, bringing out the best in its use-case scenarios by enhancing the durability and longevity of welds.
Aside from the technical aspects, considering the welder's comfort with each rod is crucial. Some professionals prefer the tactile feedback and burn-off rate of the 6011, finding it aligns with their welding style and offers them better control in challenging conditions. Conversely, those who seek precision and have calibrated their skills to deal with low-hydrogen electrodes might find the 7018 to be more suited to their advanced projects and demands for high-strength welds.
In conclusion, the decision between using a 6011 or 7018 welding rod comes down to the specific requirements of the welding job and the environment. Understanding the nuances of these rods helps optimize performance, ensuring both robust structural integrity and efficiency. For welders, mastering the application of each rod type signifies advancing their craft, paving the way for improved project outcomes and sustained credibility in their trade. Whether tackling farm repairs or constructing vast industrial plants, the judicious application of either rod is instrumental in achieving the desired welding performance.